Made my mind up to sort this out so started again
Back to basics run a plug tap down all the 8 and 10mm holes in the casing, then dress the mating flanges slightly and clean up again
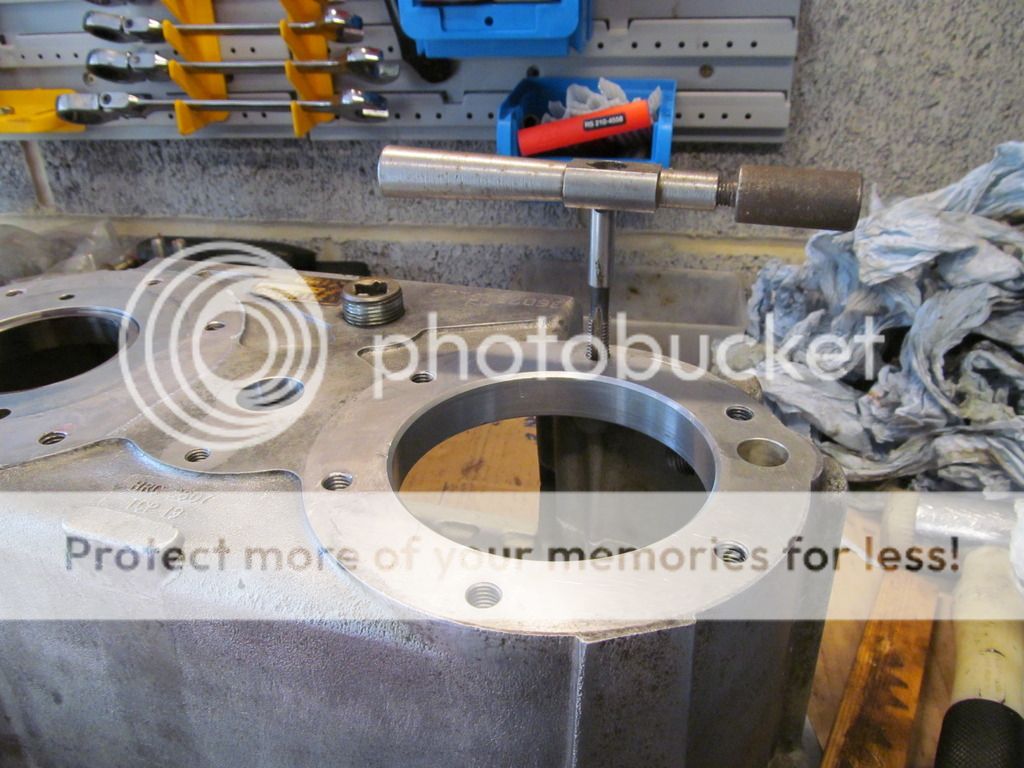
Install output shaft, fit bearing flange and nip it with two bolts, then I checked that it was tight to the casing with feeler gauges ( must get some new ones)
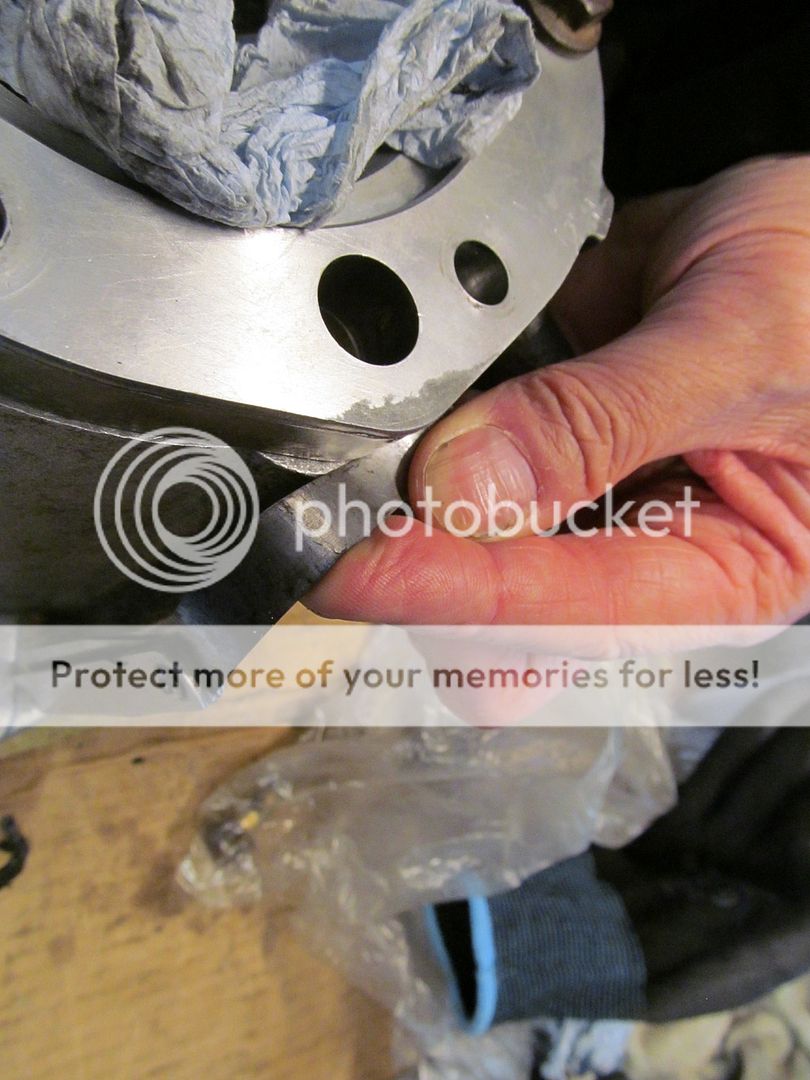
I set up the DTI and checked over and over but hard to get consistent readings, I have been putting the shaft vertical so I can zero the gauge with it in the bottom bearing push it down and then rotate it a bit to get it completely into the outer race, but I am still not happy with the consistency of the readings and the clock returning to zero. With this gap it is easy for the shaft to tip slightly and ruin the reading.
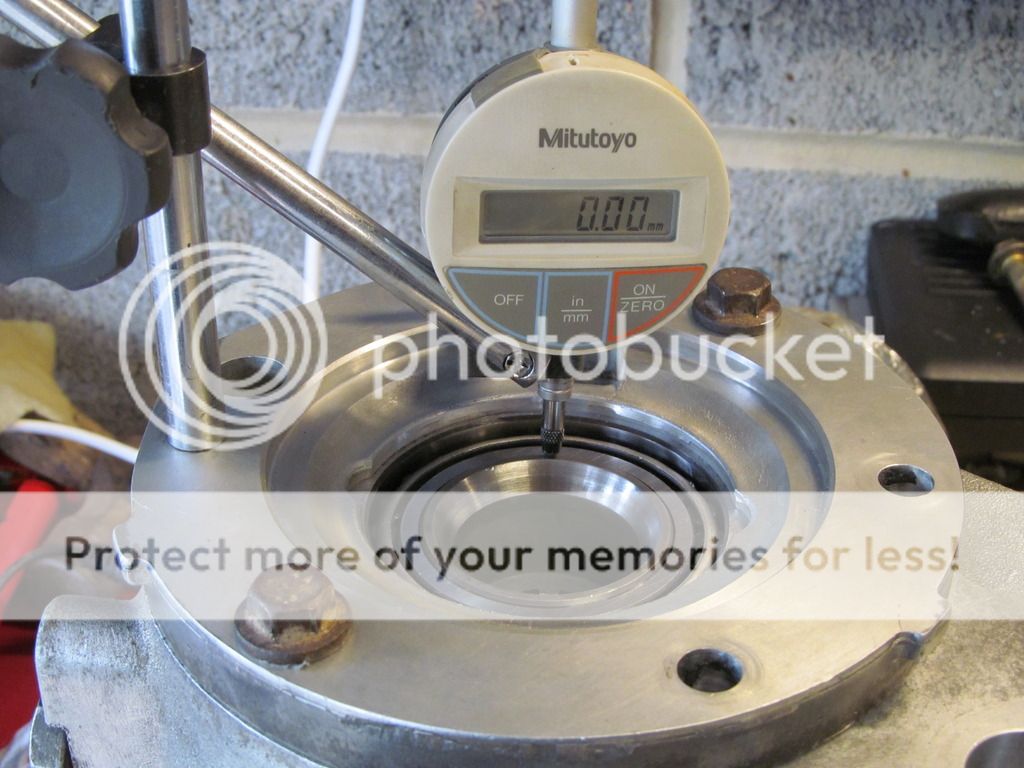
Decided to put it horizontal and pushed my flared dummy shaft into the back, that way I can push the shaft forward roughly from the center using my thumb, then push it back on the shaft at the front.
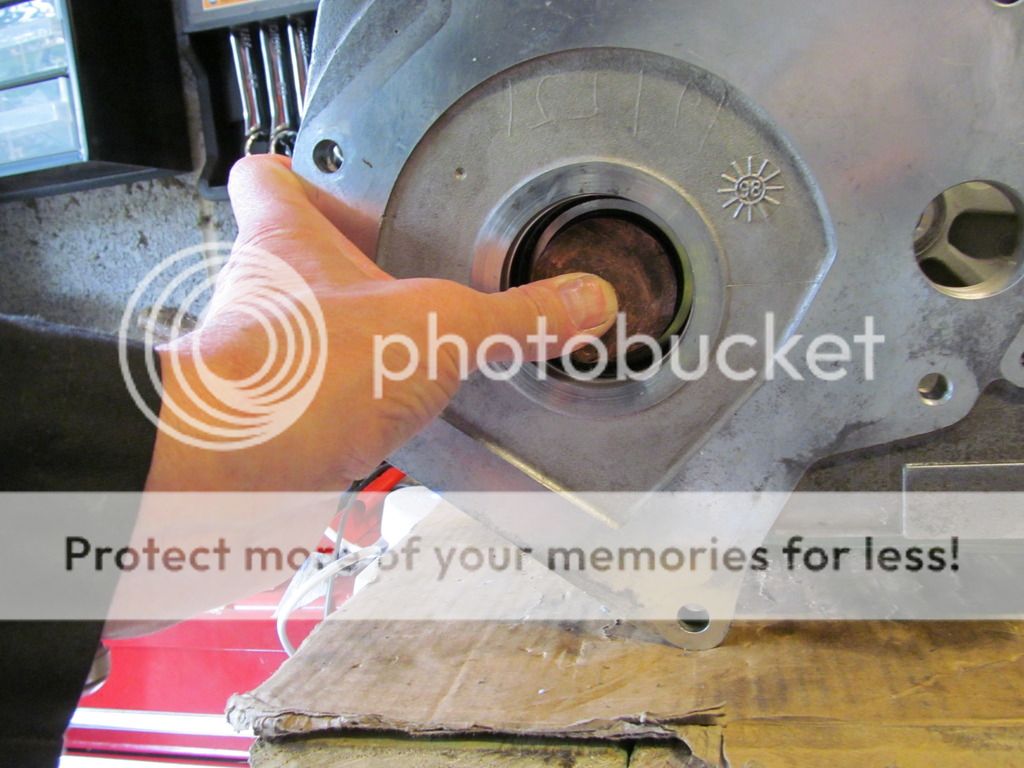
Now I am getting better readings and it seems to indicate 3.30 - 3.32 mm end float, different to my first efforts, I feel more at home with this so looks like I might get away with using a pre ground shim, a 3.35 mm shim is needed.
James any comment on the pre load, given I cant grind the shim and not every size is available, would you err on the high side or avoid any overload?
Well time to press on a bit, bearings in the freezer warm up the housing and knock in the bearing using one of the old races on the outer.
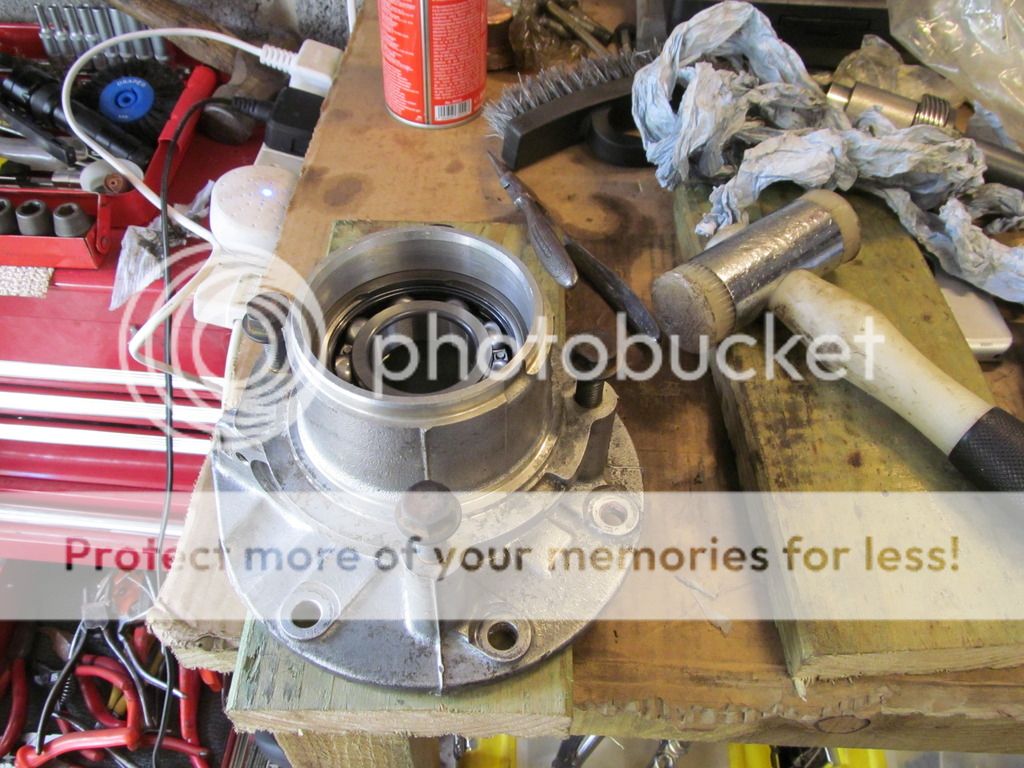
Would love a press but I don't have one, looking for a good way to get the shafts into the inner race.
Put the shaft in position, put the output flange onto the splines, add two washers.
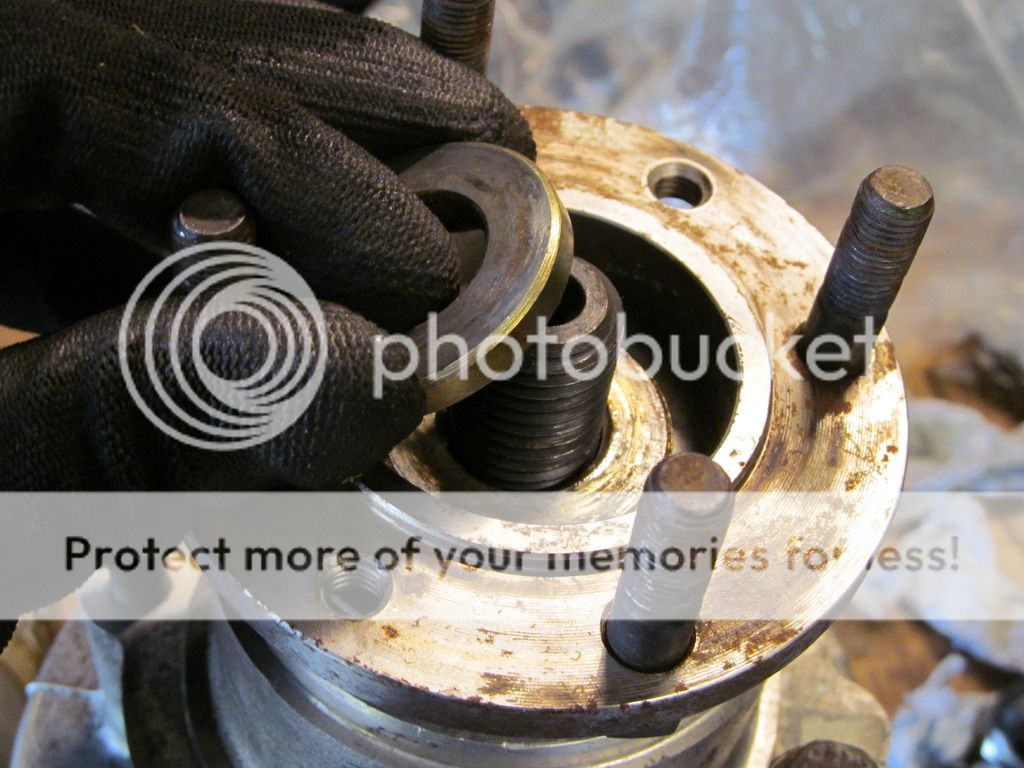
Then put the nut on and use it to draw the shaft into the bearing ( with a little help from my friend) it only pulls on the inner race, you can easily hold the shaft and stop the rotation just with your hand
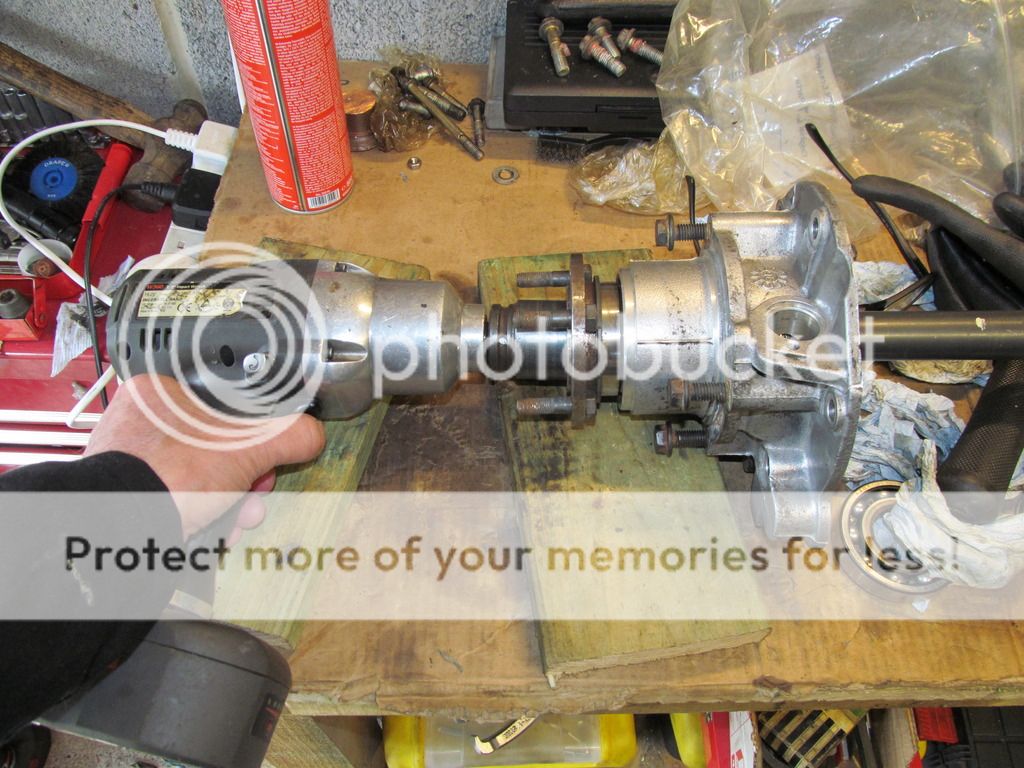
Just wanted to assemble a bit more, so get out the Hlyomar silicon.
Found over time that if you want to seal with silicon
1 Clean off all traces of the old stuff
2 Minutes before you assemble it clean both faces with solvent
3 Don't go mad it's not the case that more silicon you use better the seal.
4 If possible leave the small bead of silicon which squeezes out when you tighten it up
Sorted out the Diff lock mechanism and put the ball spring and plug back with sealant on the plug.
Now this is where I am up to, need the difflock switch setting up but I am happy I can do that later don't want to break it while working on the casing.
All for now I have to get some health problems sorted next weekend so may be out of it for a short time, stuff some clean paper inside and put it to bed.
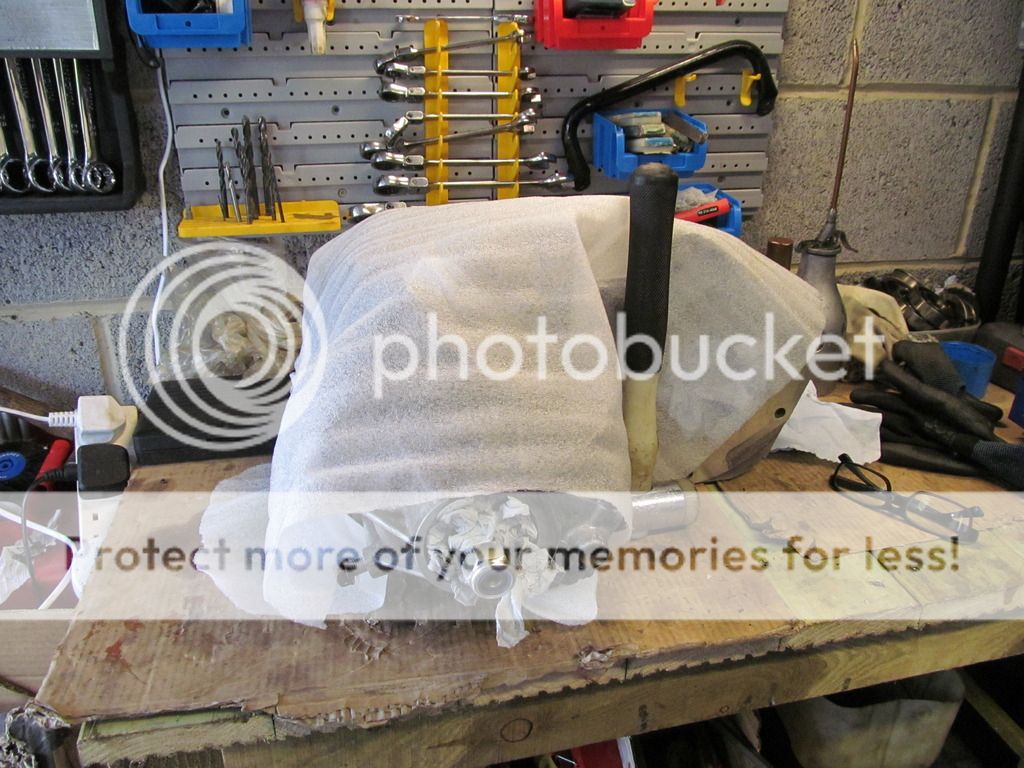