Trewey
Cockernee, Pasty munchin bastid.
- Posts
- 20,093
- Location
- Kernow - Near England
Here's how I did mine.....
First I drained the oil from the Transfer Box..
Remove the filler plug (a 1/2" ratchet fits)
Then remove the drain plug...
and allow the oil to drain into a suitable container....
jacking up the front of the Landy will make access easier and allow you to rotate the propshaft by turning the wheel. Chock the rear wheels and support on axle stands too for safety...
Next, you need to remove the front propshaft. Mark the propshaft and the drive flanges, so that you can replace it in the same alignment.
There's not much room to get a socket or spanner on the nuts...
so, disconnect the diff end first (where there's more space). This then allows you to push the propshaft up (towards the oil filter) and create space to get a socket on the Transfer Box end nuts.
THE NUTS ARE 9/16" NOT 14mm - it makes a big difference!
Remove the propshaft and you will see a large nylock nut in the centre of the drive flange. Put the Landy in gear and undo this (30mm socket) - it's tight!
You can then remove the drive flange and spacer washer and expose the Oil Seal.
Prize the old oil seal out with a screwdriver, taking care not to damage it's seat.
This was my old Seal - the round spring, which holds it tight on the drive flange had completely detatched - that's why it was leaking so badly.
Clean up around the inside of the seal seat and the shaft of the drive flange. My drive flange was slightly burred, so I used some fine wet-n-dry to smooth it off.
Lubricate the outside of the new seal, and the inside of the seat, with some clean EP90.
Then push the new seal into place, taking care to keep it square and avoid damaging it. It's a tight fit - I used my 52mm hub-nut socket as a drift, whilst tapping it in with a hammer.
Then lubricate the inside of the seal, and the outside of the drive flange with some clean EP90, before pushing the drive flange back into place. Don't forget to fit the propshaft bolts through the drive flange before re-fitting it.
Refit the washer and big nyloc nut (best to use a new one if possible)...
...and re-tighten the nut to the specified torque (135 lbft or 2 good grunts on a 2ft breaker bar).
Re-fit the prop-shaft (Transfer Box end first) and tighten the bolts to 35 lbft (best to use new nuts if you can).
Re-fill the Transfer Box with fresh EP90 - one of these oil syphons makes the job a lot easier.
Remove the jack and take it for a test drive.
Job Done!
First I drained the oil from the Transfer Box..
Remove the filler plug (a 1/2" ratchet fits)
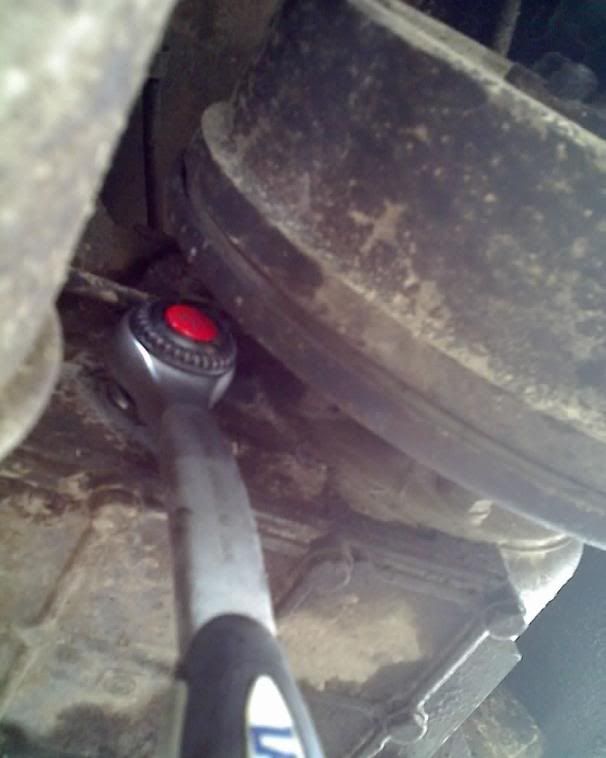
Then remove the drain plug...
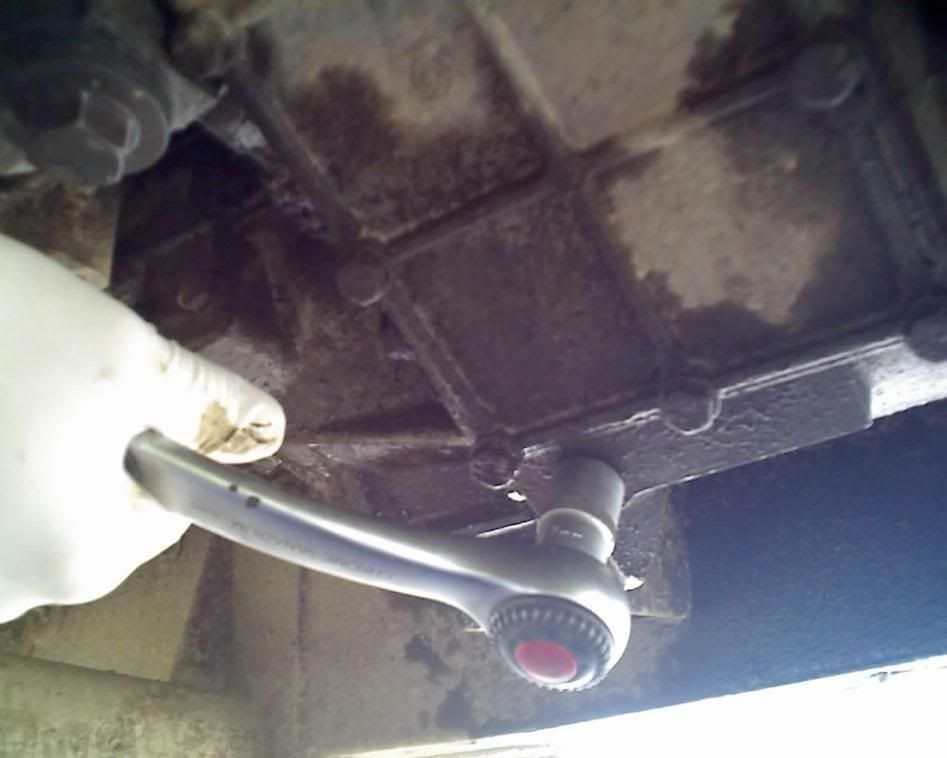
and allow the oil to drain into a suitable container....
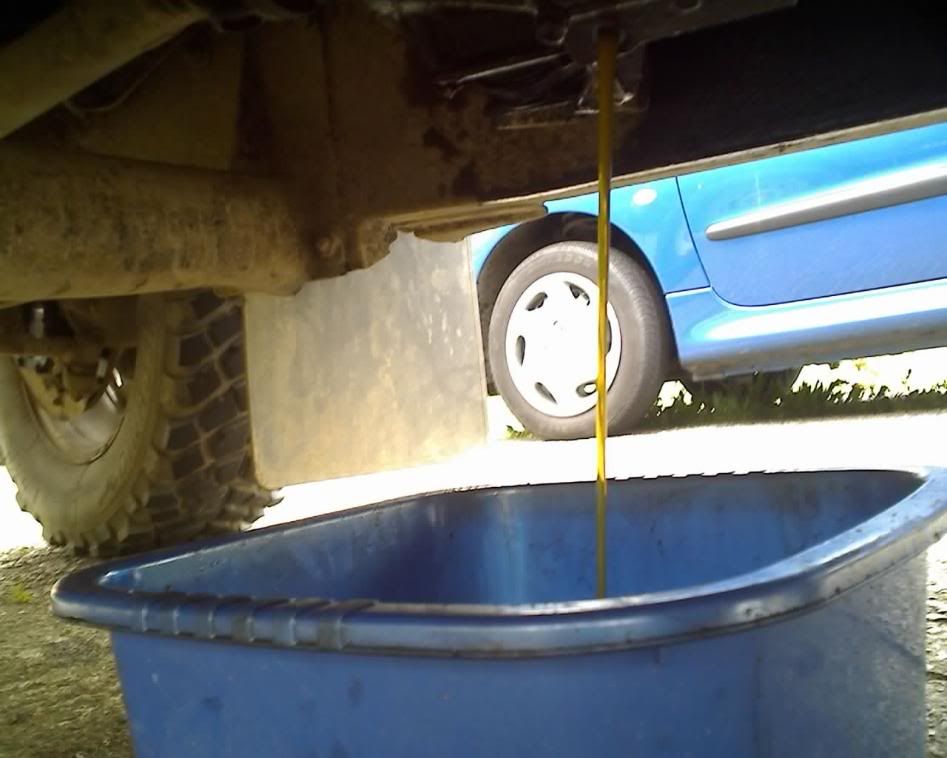
jacking up the front of the Landy will make access easier and allow you to rotate the propshaft by turning the wheel. Chock the rear wheels and support on axle stands too for safety...
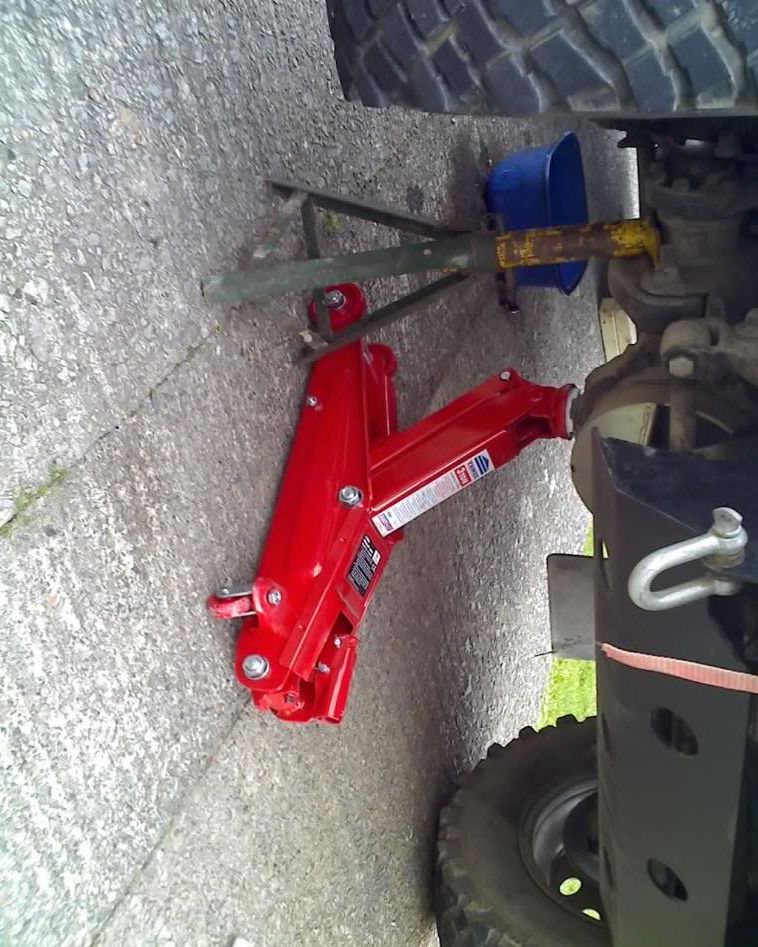
Next, you need to remove the front propshaft. Mark the propshaft and the drive flanges, so that you can replace it in the same alignment.
There's not much room to get a socket or spanner on the nuts...
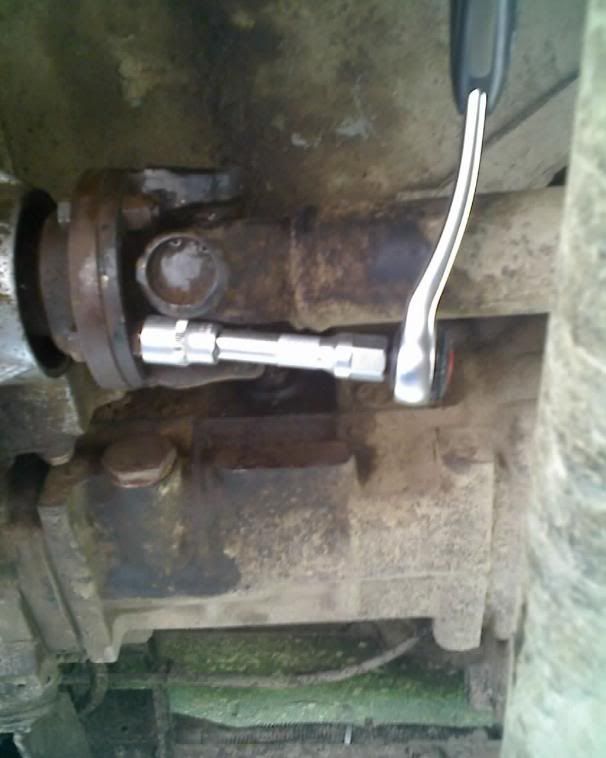
so, disconnect the diff end first (where there's more space). This then allows you to push the propshaft up (towards the oil filter) and create space to get a socket on the Transfer Box end nuts.
THE NUTS ARE 9/16" NOT 14mm - it makes a big difference!
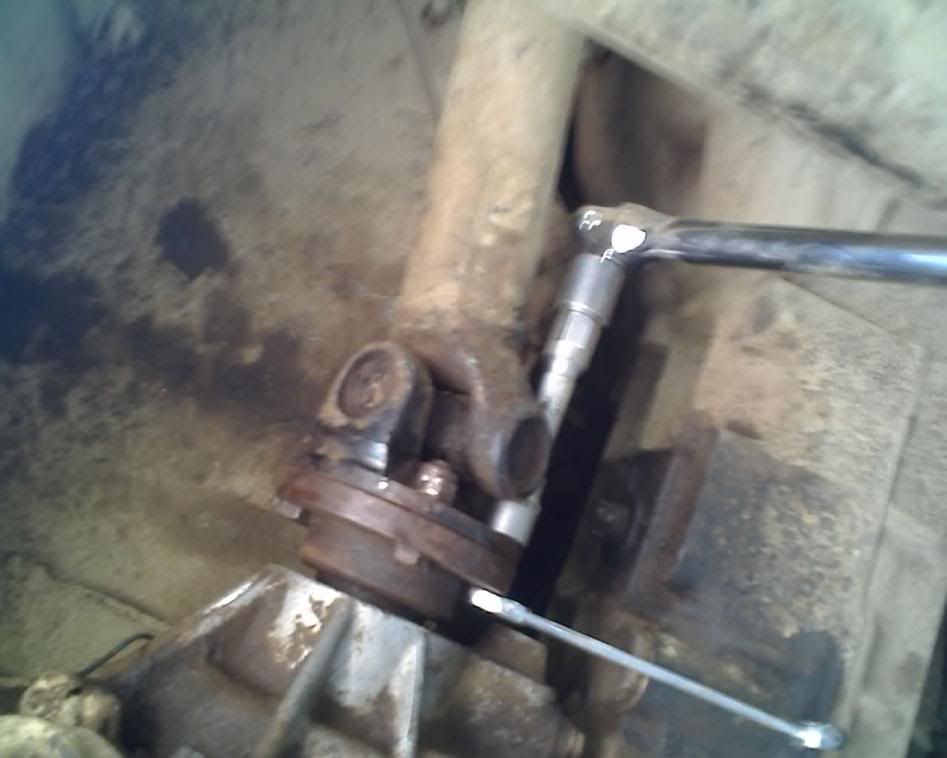
Remove the propshaft and you will see a large nylock nut in the centre of the drive flange. Put the Landy in gear and undo this (30mm socket) - it's tight!
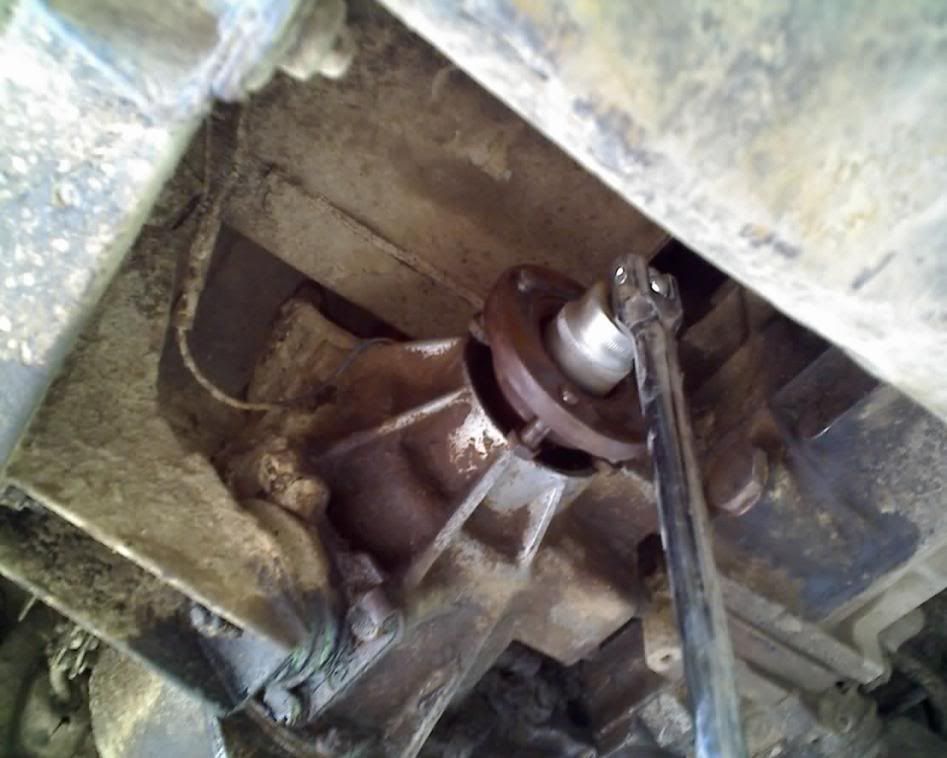
You can then remove the drive flange and spacer washer and expose the Oil Seal.
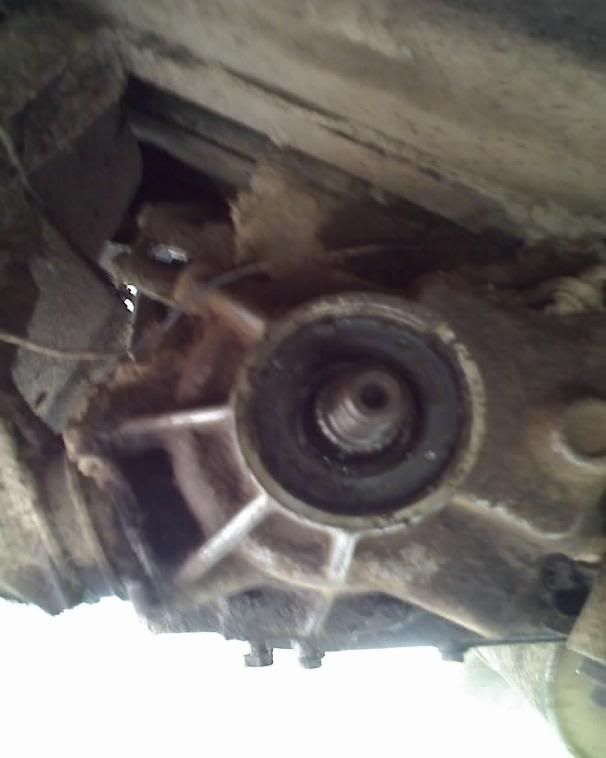
Prize the old oil seal out with a screwdriver, taking care not to damage it's seat.
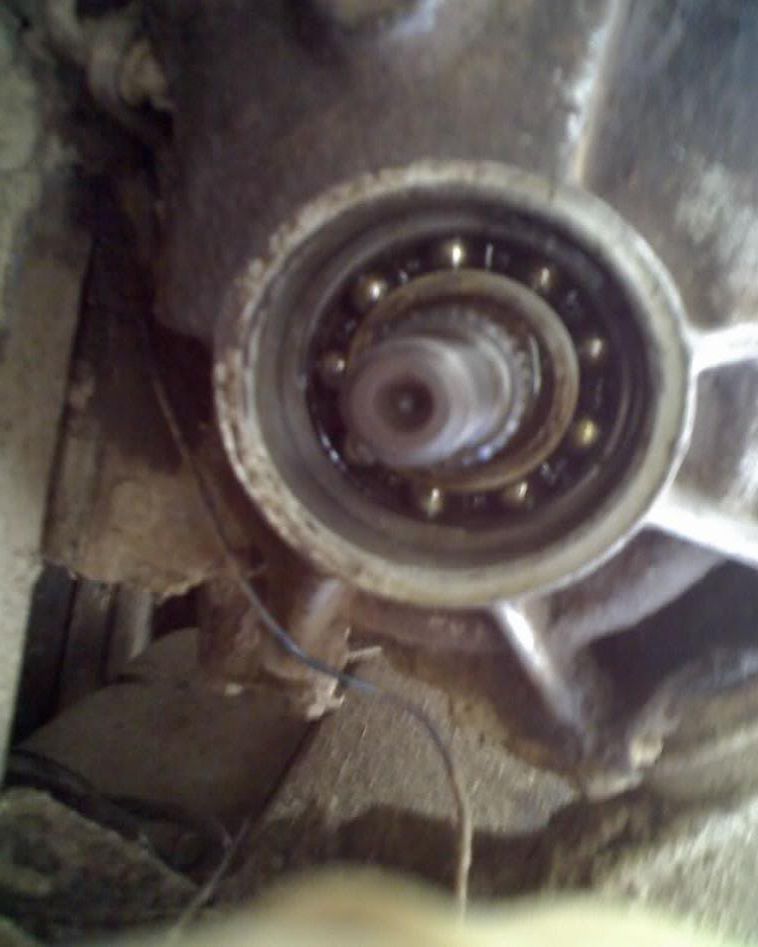
This was my old Seal - the round spring, which holds it tight on the drive flange had completely detatched - that's why it was leaking so badly.
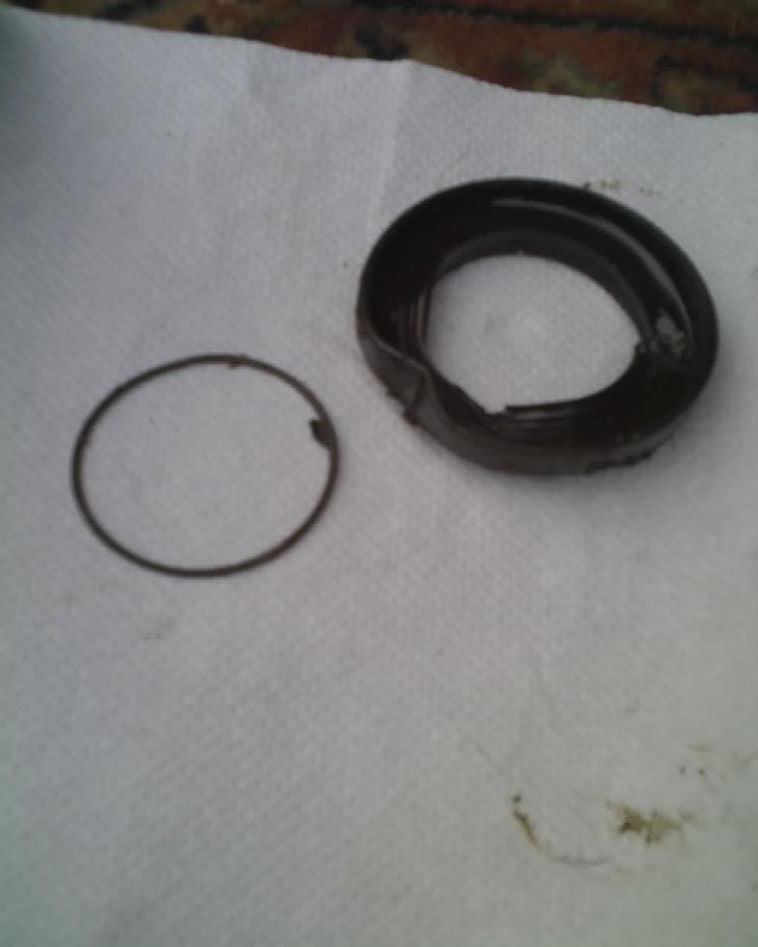
Clean up around the inside of the seal seat and the shaft of the drive flange. My drive flange was slightly burred, so I used some fine wet-n-dry to smooth it off.
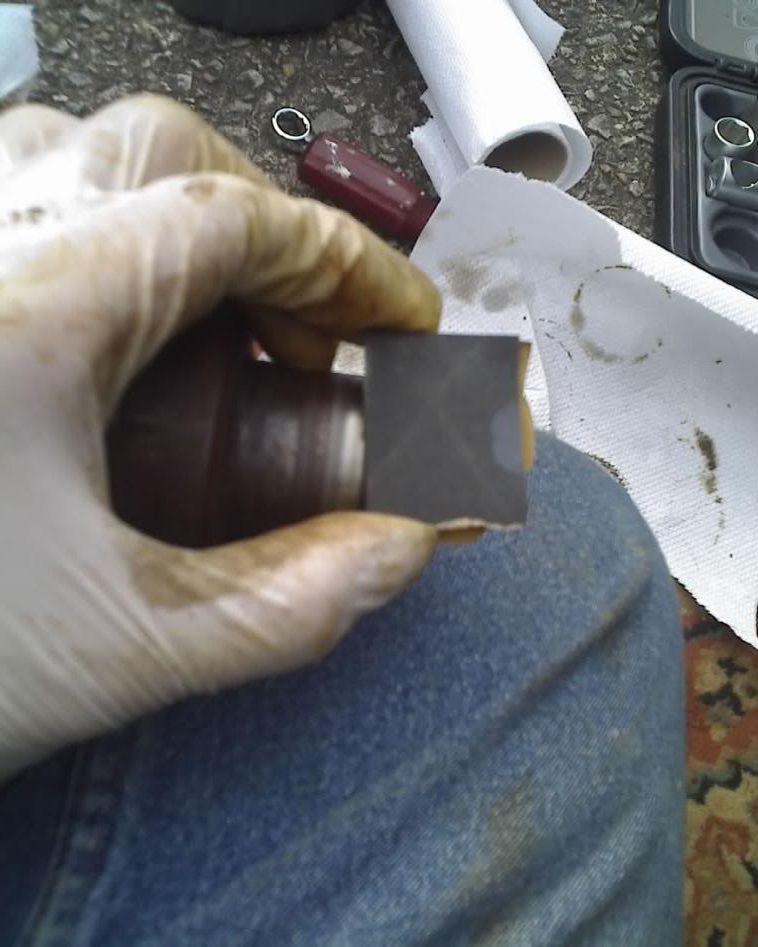
Lubricate the outside of the new seal, and the inside of the seat, with some clean EP90.
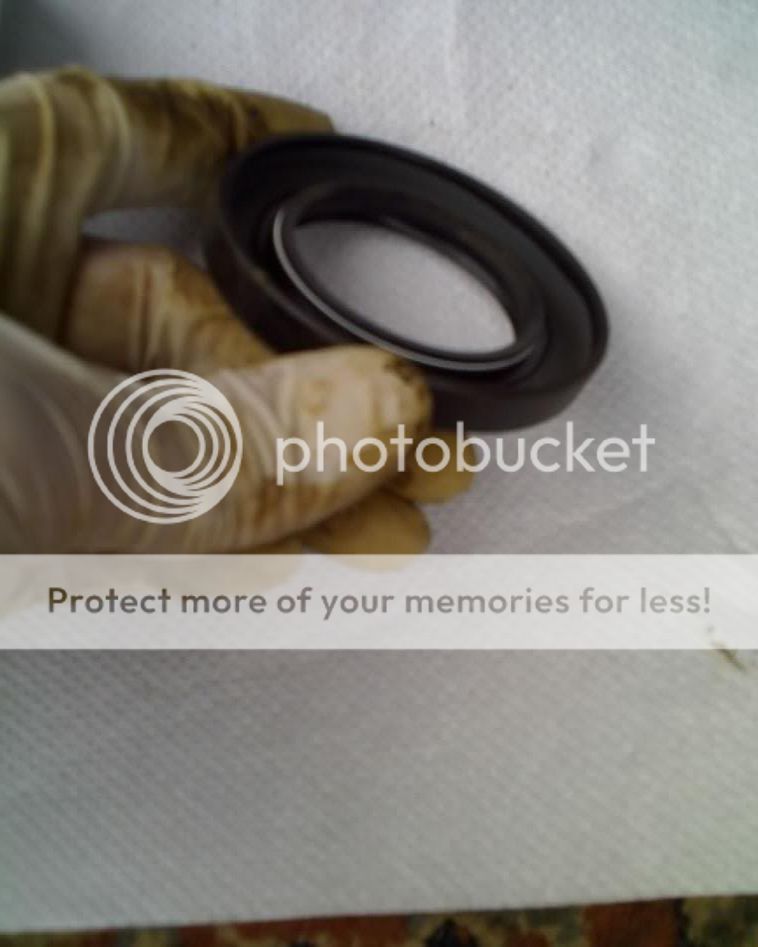
Then push the new seal into place, taking care to keep it square and avoid damaging it. It's a tight fit - I used my 52mm hub-nut socket as a drift, whilst tapping it in with a hammer.
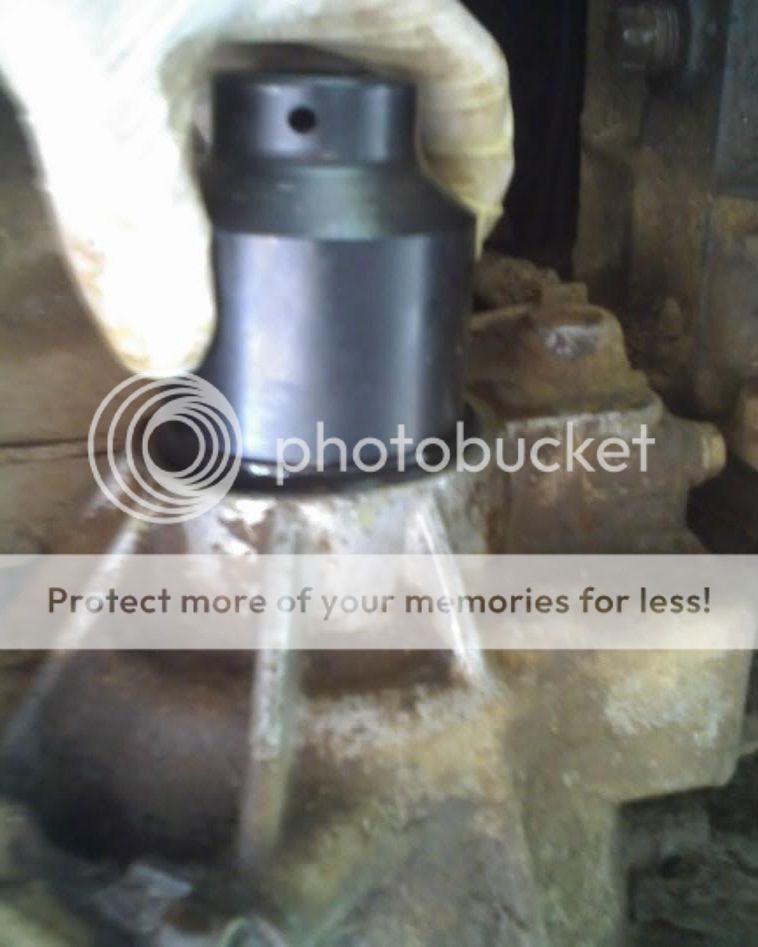
Then lubricate the inside of the seal, and the outside of the drive flange with some clean EP90, before pushing the drive flange back into place. Don't forget to fit the propshaft bolts through the drive flange before re-fitting it.

Refit the washer and big nyloc nut (best to use a new one if possible)...
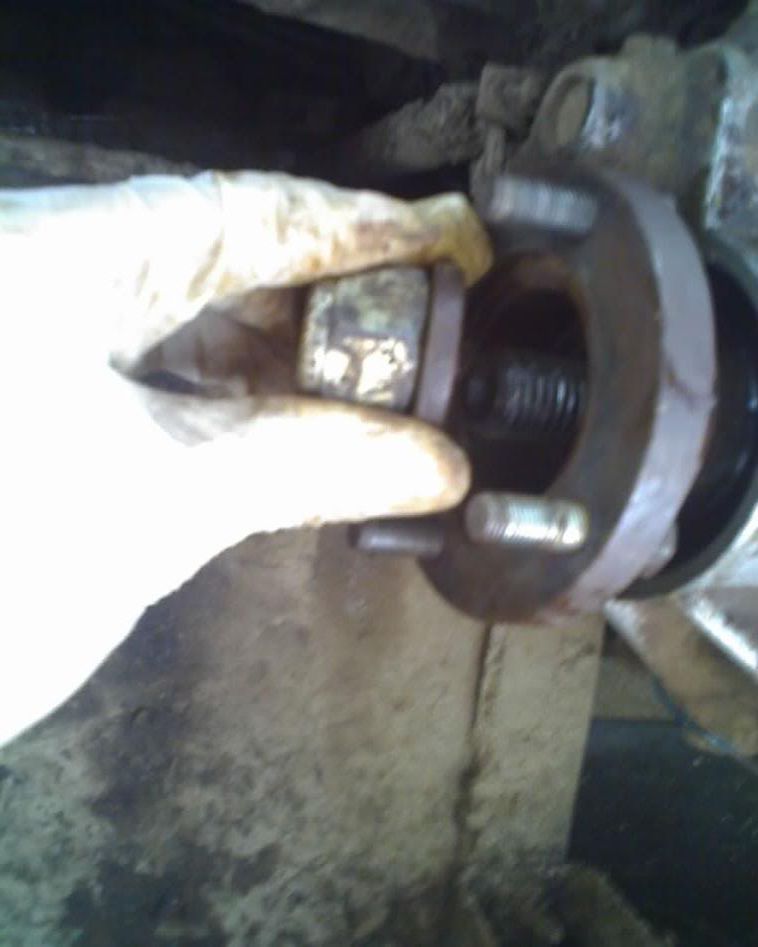
...and re-tighten the nut to the specified torque (135 lbft or 2 good grunts on a 2ft breaker bar).
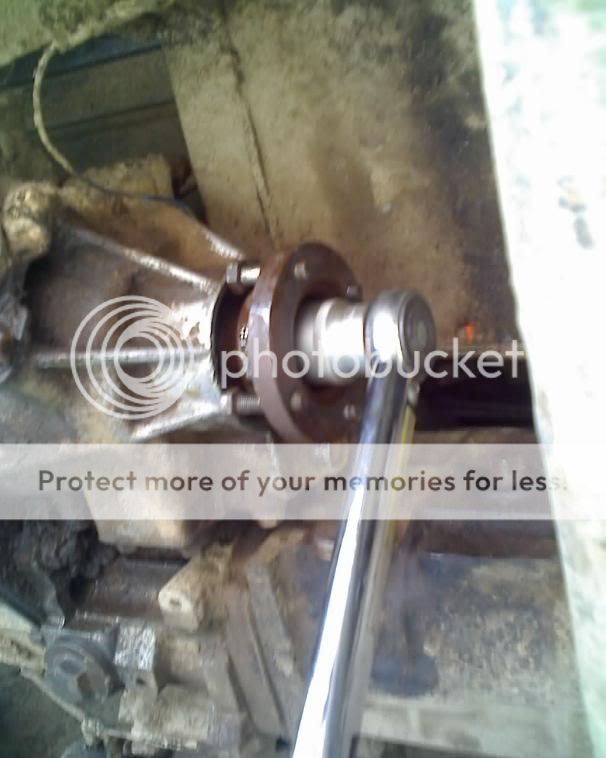
Re-fit the prop-shaft (Transfer Box end first) and tighten the bolts to 35 lbft (best to use new nuts if you can).
Re-fill the Transfer Box with fresh EP90 - one of these oil syphons makes the job a lot easier.
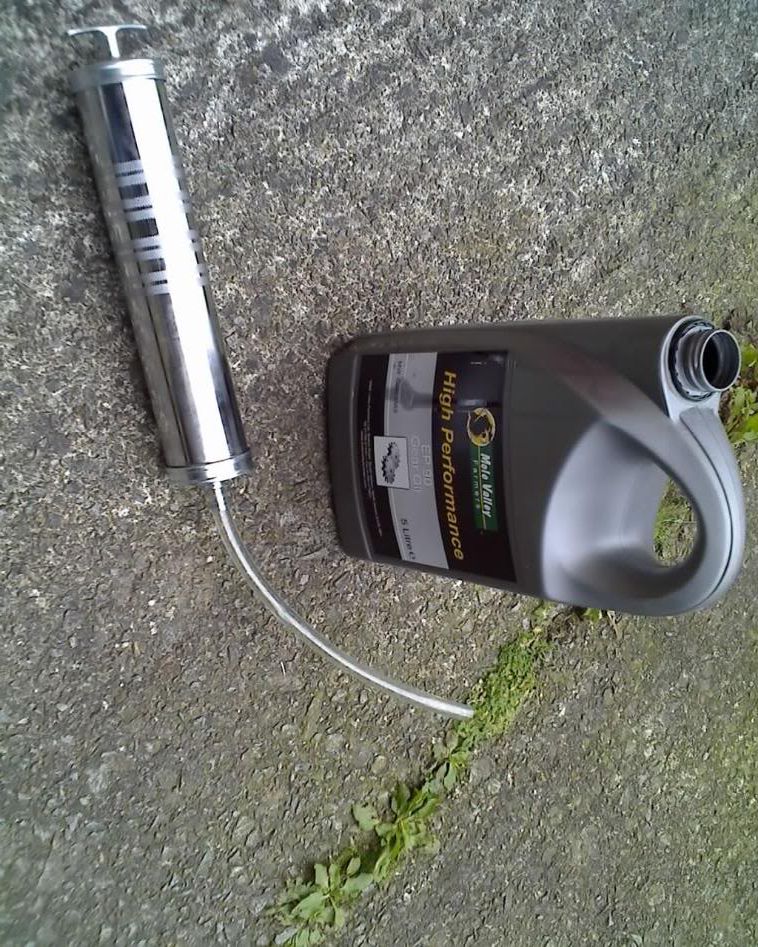
Remove the jack and take it for a test drive.
Job Done!