LincolnSteve
Well-Known Member
- Posts
- 1,201
- Location
- Lincoln
So in October 2014 I finally got myself a petrol 88inch series 3. I have no real reason to own one but I have wanted one since I was a boy. Of course because it's my first Land Rover it has turned out to be in much worse condition than I thought. If I had any sense I should have bitten the bullett and replaced the chassis. But because i'm daft I decided that I want to get it through at least a couple more MOT's with it's original chassis and bulkhead first.
[/URL][/IMG]
It looks pretty good if you don't get too close. At least James liked it.
[/IMG]
[/URL]
[URL='http://s1042.photobucket.com/user/lincolnsteve1/media/Mobile%20Uploads/DSC06767_zpstottrgxh.jpg.html']
[/URL]
Any way the more I poked about the more it became obvious that some major work was going to be needed so the strip down began.
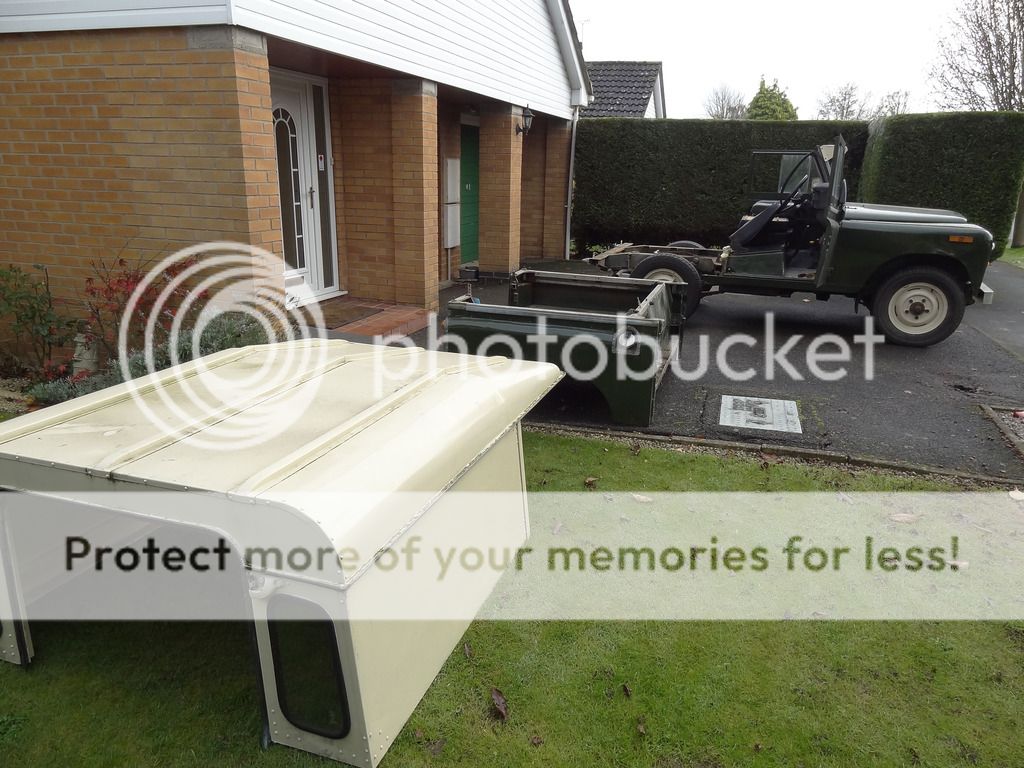
[URL='http://s1042.photobucket.com/user/lincolnsteve1/media/Mobile%20Uploads/DSC06931_zpswy8h3xgr.jpg.html']
[/URL]

It looks pretty good if you don't get too close. At least James liked it.

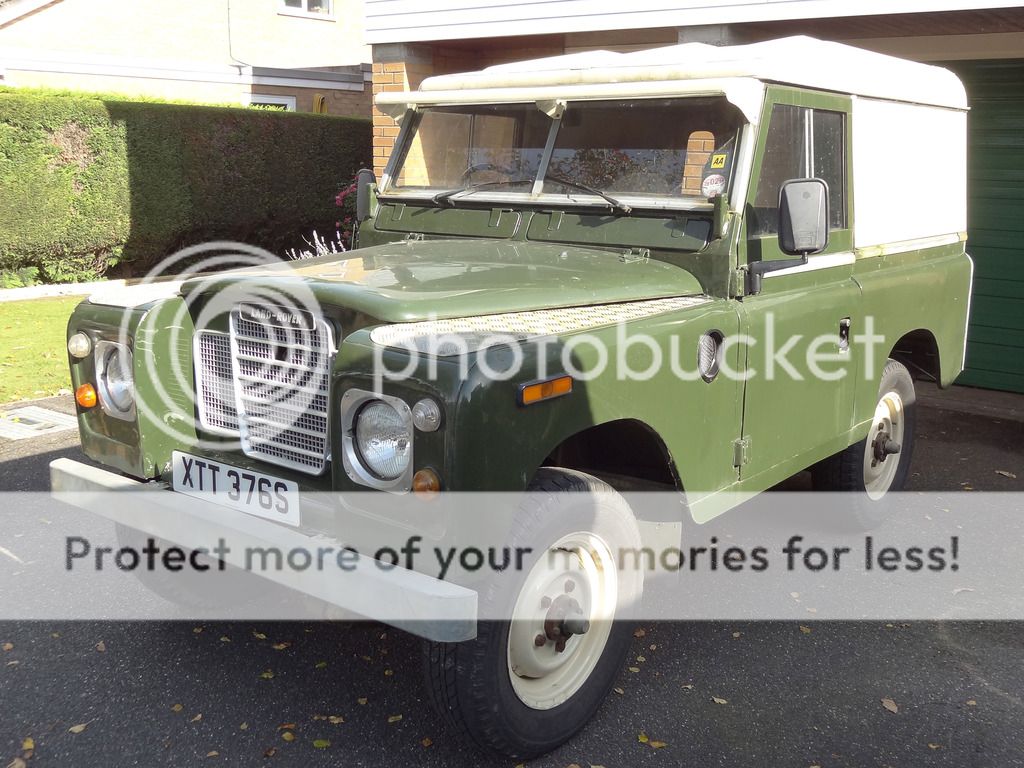
[URL='http://s1042.photobucket.com/user/lincolnsteve1/media/Mobile%20Uploads/DSC06767_zpstottrgxh.jpg.html']
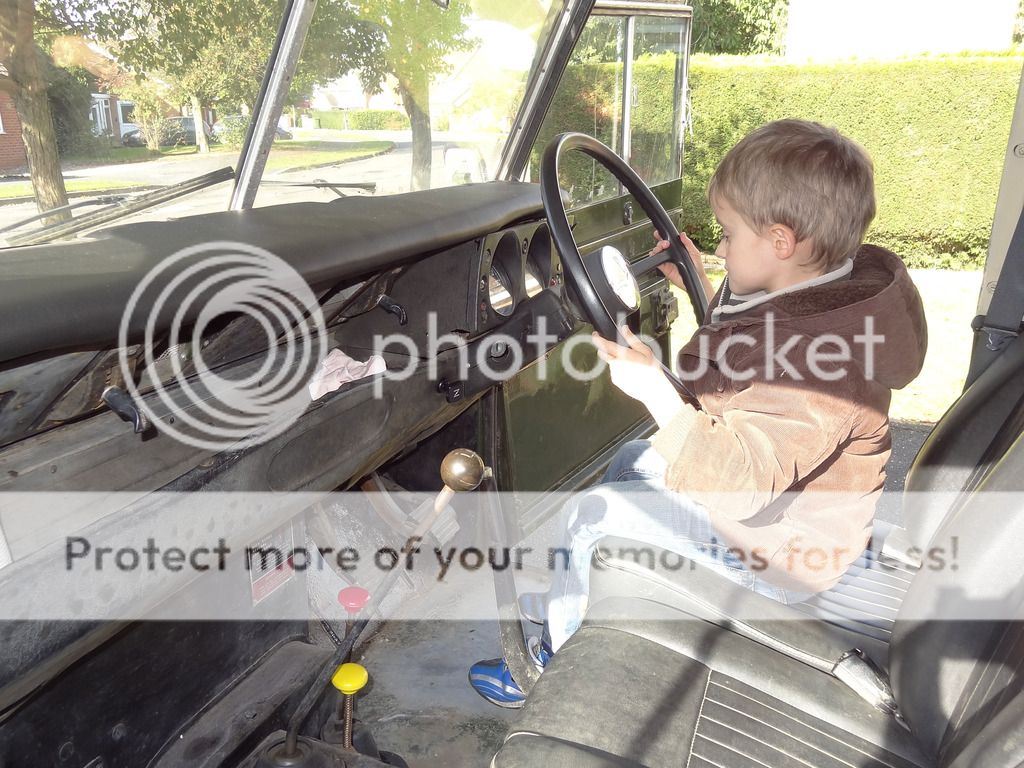
Any way the more I poked about the more it became obvious that some major work was going to be needed so the strip down began.
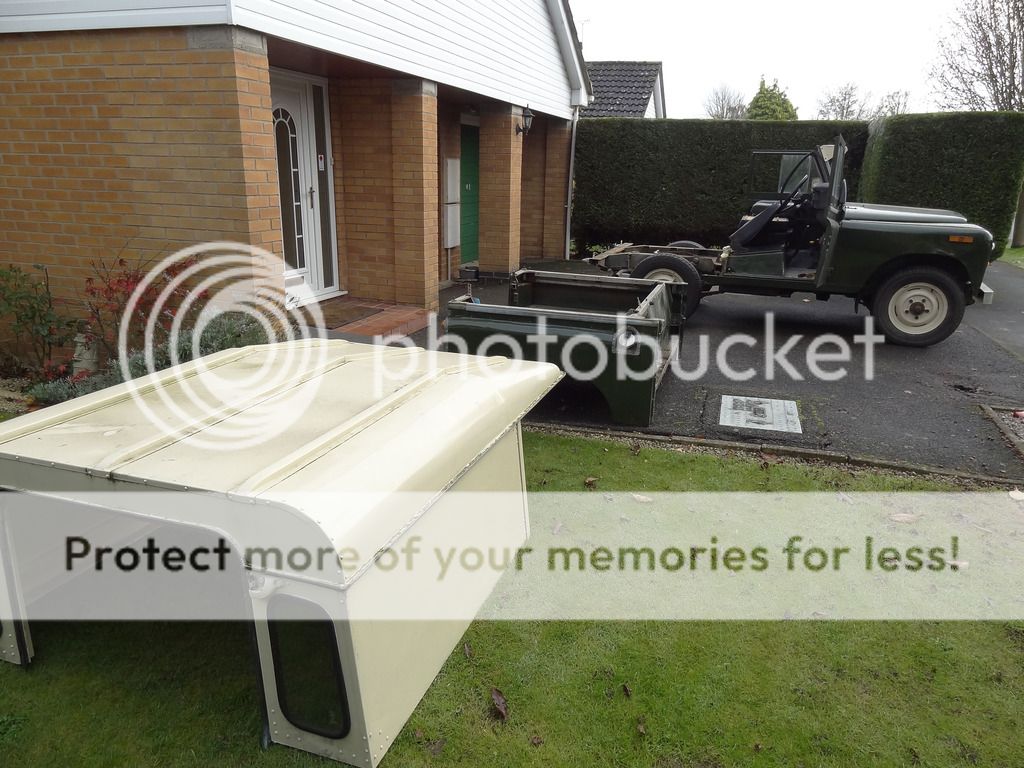
[URL='http://s1042.photobucket.com/user/lincolnsteve1/media/Mobile%20Uploads/DSC06931_zpswy8h3xgr.jpg.html']

Last edited: