- Posts
- 14,902
- Location
- Doncaster
Yeah, it's what I read and re-read .. but thought I'd use it and show it for a Disco too .. 
To which end, it seems some of the rot is a bit worse than I first thought ... All the body mounts and pillars look OK, but a quick brush with a wire brush and some pulling about has revealed the following ..
Drivers side looking forwards underneath..
Drivers side rear underneath..
Nearside front underneath is fine, but nearside rear isn't ..
To which end, it seems some of the rot is a bit worse than I first thought ... All the body mounts and pillars look OK, but a quick brush with a wire brush and some pulling about has revealed the following ..
Drivers side looking forwards underneath..
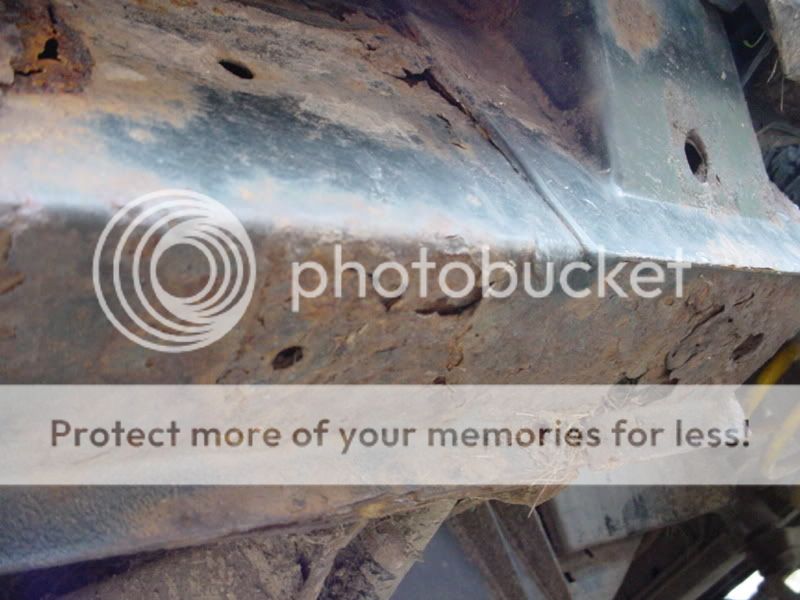
Drivers side rear underneath..
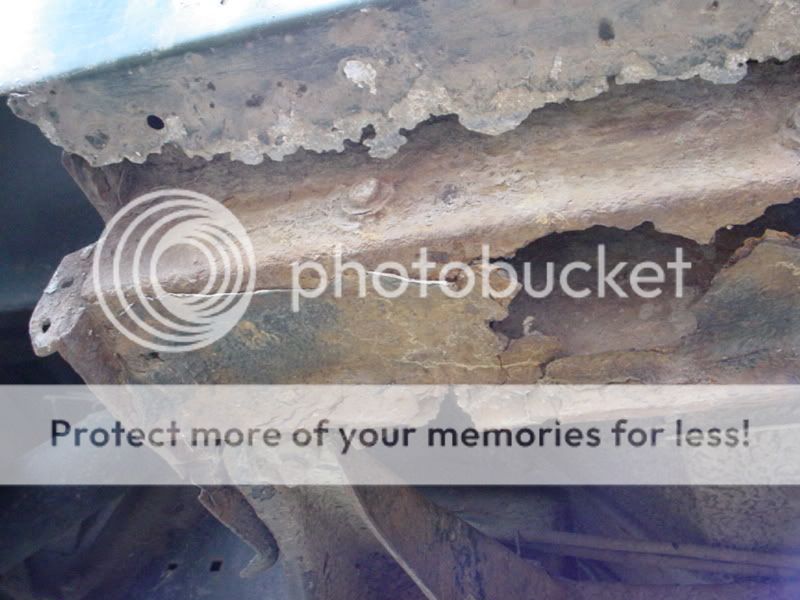
Nearside front underneath is fine, but nearside rear isn't ..
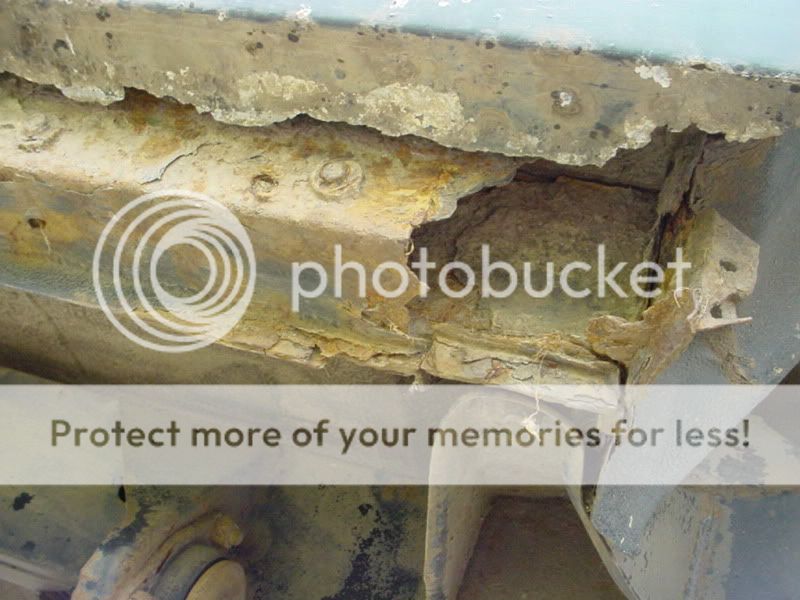
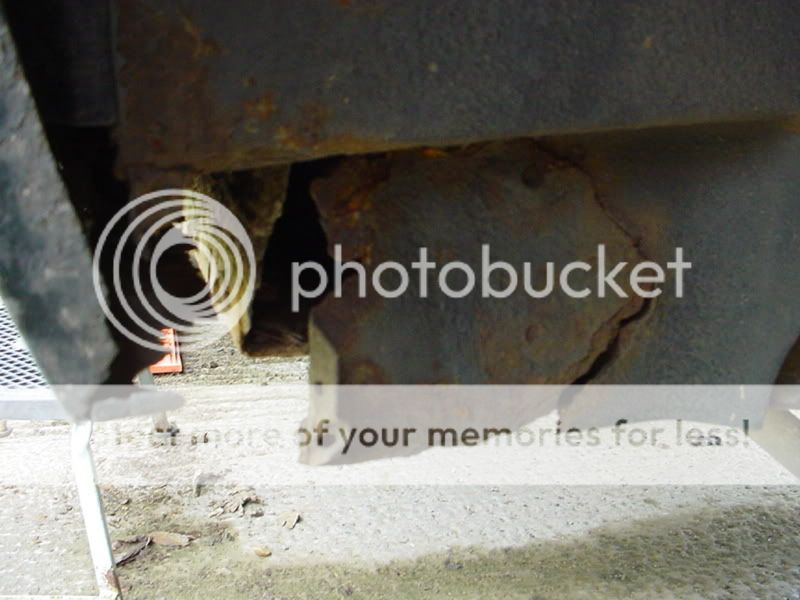