Litch
Well-Known Member
- Posts
- 2,237
- Location
- Oxfordshire
Bad weekend really.
Finished removing the clutch / flywheel, adaptor ring etc but from then on it just didn't seem to go right.
Adaptor ring fits using some of the original fixings but others are not used as when the gearbox is offered up the bellhousing bolts direct through to the crankcase (so they are longer) and these didn't come in the kit. Managed to get around it but a bit peeved.
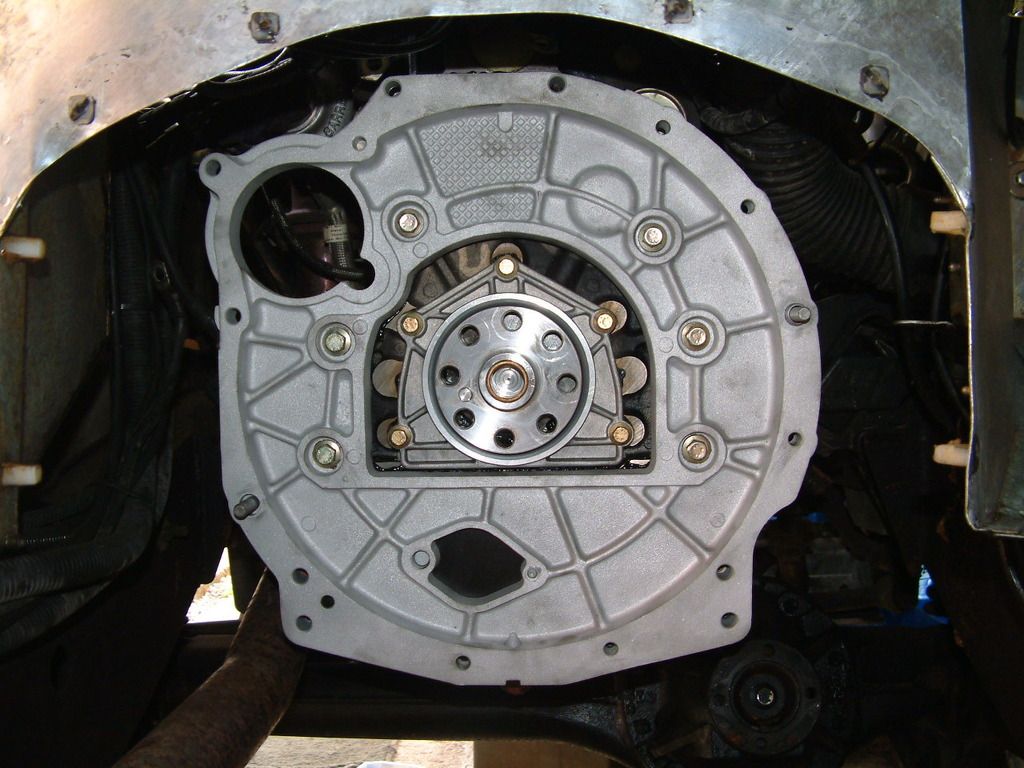
Flex plate fitted.
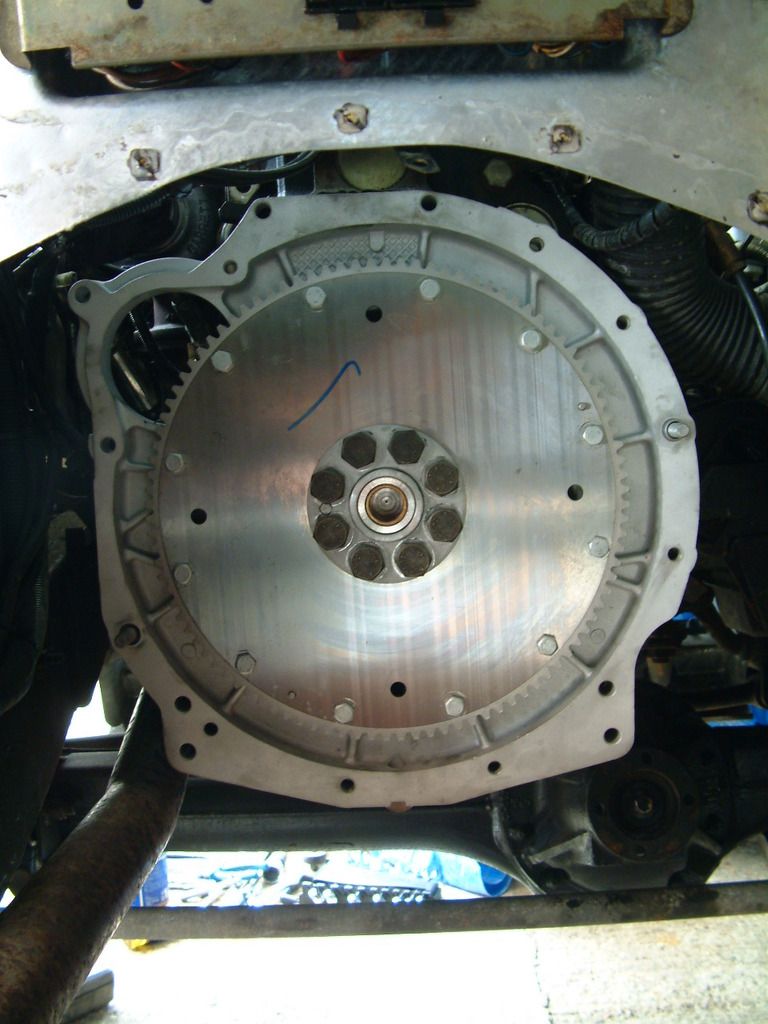
Fitting the gearbox was a pain.
Didn't want to go on at first and this turned out to be a locating dowel that wasn't a perfect fit. After that I bolted it together and went to bolt the flex-plate to the torque converter (you have to do this through the starter-motor hole) and I found that the torque converter would not spin to allow me to align the holes. I know it hadn't come dislocated when fitting as I left the clamp in situ right up until the last moment (I had the gearbox sliding fore & aft on four M10 long smooth-shank bolts and supported at the end by the crane so it was very stable). I pondered and eventually found that if I just backed off the bellhousing bolts a turn it was possible to spin the torque converter and align the holes, after that I nipped the bellhousing bolts up again and it turned over ok.
Did some online reading later and discovered that this is very common (just doesn't mention it in the manual).
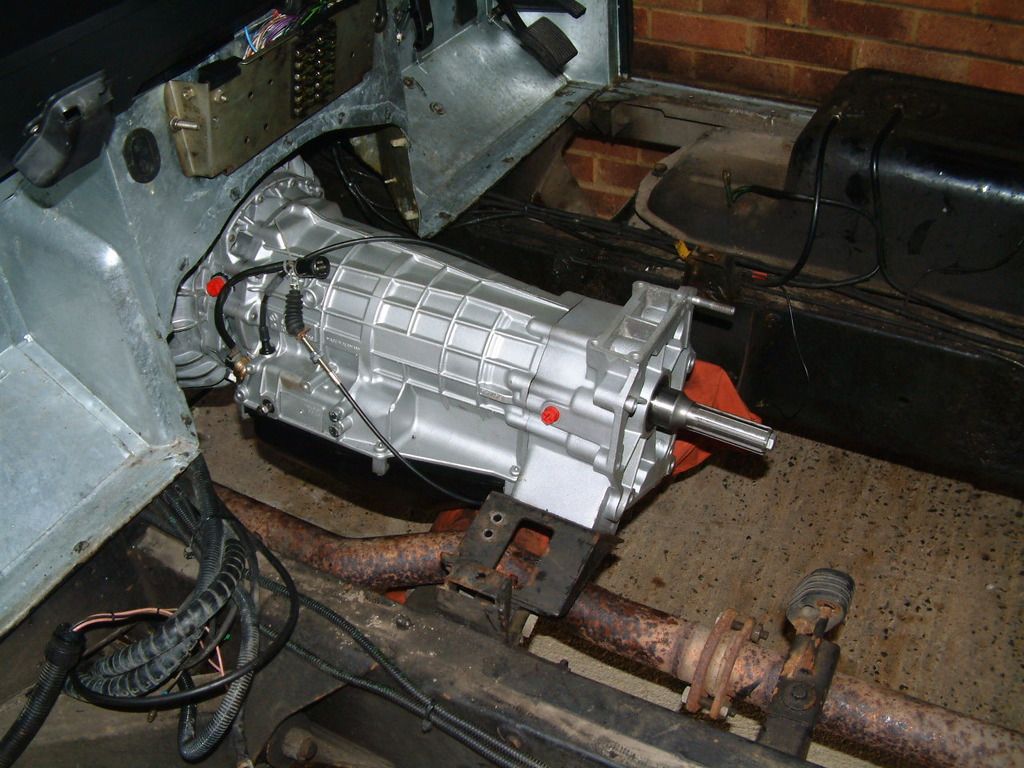
Final insult was when I went to fit the transfer-box.
I am familiar with my old R380 & LT230 as I had them off 3-years ago when I was having my bulkhead galvanised and made use of the time that it was away to remove the transmission to fit a new clutch and replace a couple of seals. It wasn't really necessary but I had time on my hands and with all that access so it seemed foolish not to. I know how they separate but could I move them apart, could I hell !. It is not RTV, there is the slightest movement and I have inserted a blade so it is not suction, it is a physical lock (and yes, I HAVE removed all the bolts / nut before anyone asks). Thought I would remove the input gear to see if that helps but that is stuck fast as well so I guess that is the culprit. Splines look to be in good order (it is cross-drilled and I can see through the bottom inspection cover that there is no rust holding them together) so I gave it up as a bad job and will look at it again next week.
In the mean time, if anyone has any ideas they will be greatly appreciated.
Finished removing the clutch / flywheel, adaptor ring etc but from then on it just didn't seem to go right.
Adaptor ring fits using some of the original fixings but others are not used as when the gearbox is offered up the bellhousing bolts direct through to the crankcase (so they are longer) and these didn't come in the kit. Managed to get around it but a bit peeved.
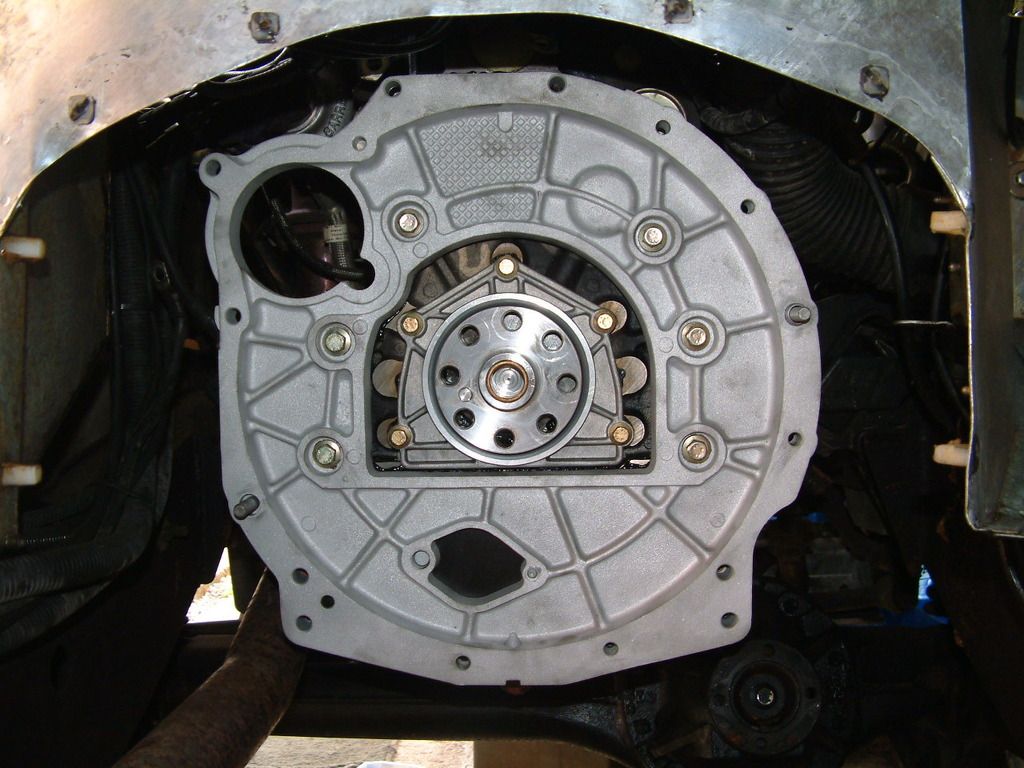
Flex plate fitted.
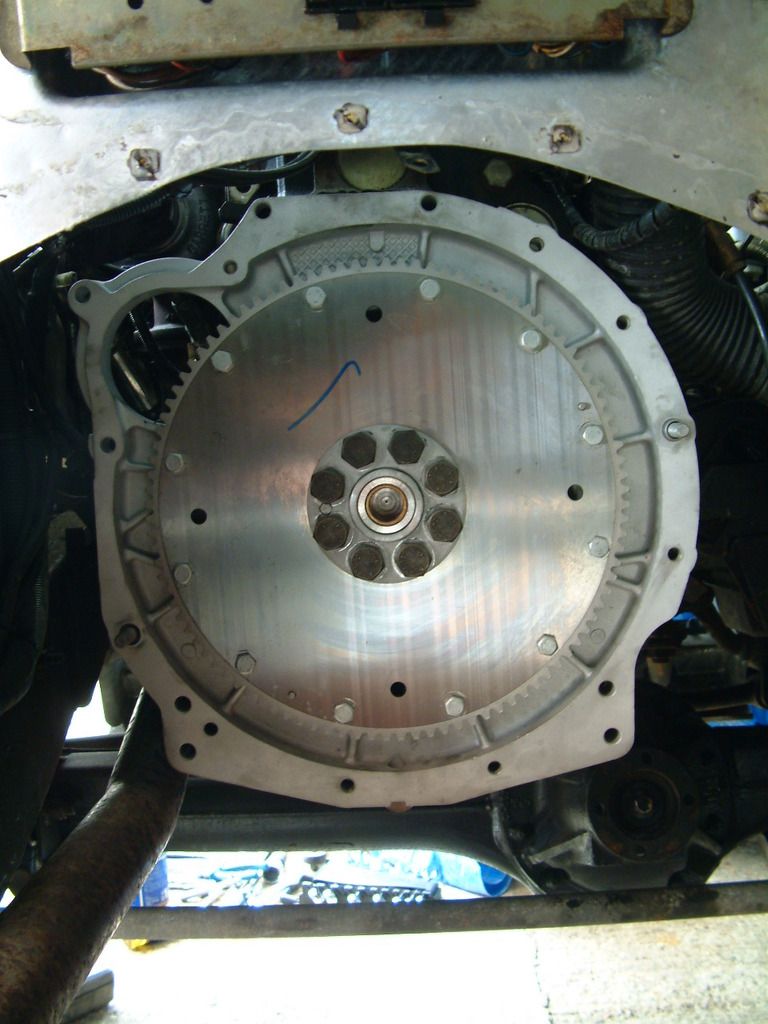
Fitting the gearbox was a pain.
Didn't want to go on at first and this turned out to be a locating dowel that wasn't a perfect fit. After that I bolted it together and went to bolt the flex-plate to the torque converter (you have to do this through the starter-motor hole) and I found that the torque converter would not spin to allow me to align the holes. I know it hadn't come dislocated when fitting as I left the clamp in situ right up until the last moment (I had the gearbox sliding fore & aft on four M10 long smooth-shank bolts and supported at the end by the crane so it was very stable). I pondered and eventually found that if I just backed off the bellhousing bolts a turn it was possible to spin the torque converter and align the holes, after that I nipped the bellhousing bolts up again and it turned over ok.
Did some online reading later and discovered that this is very common (just doesn't mention it in the manual).
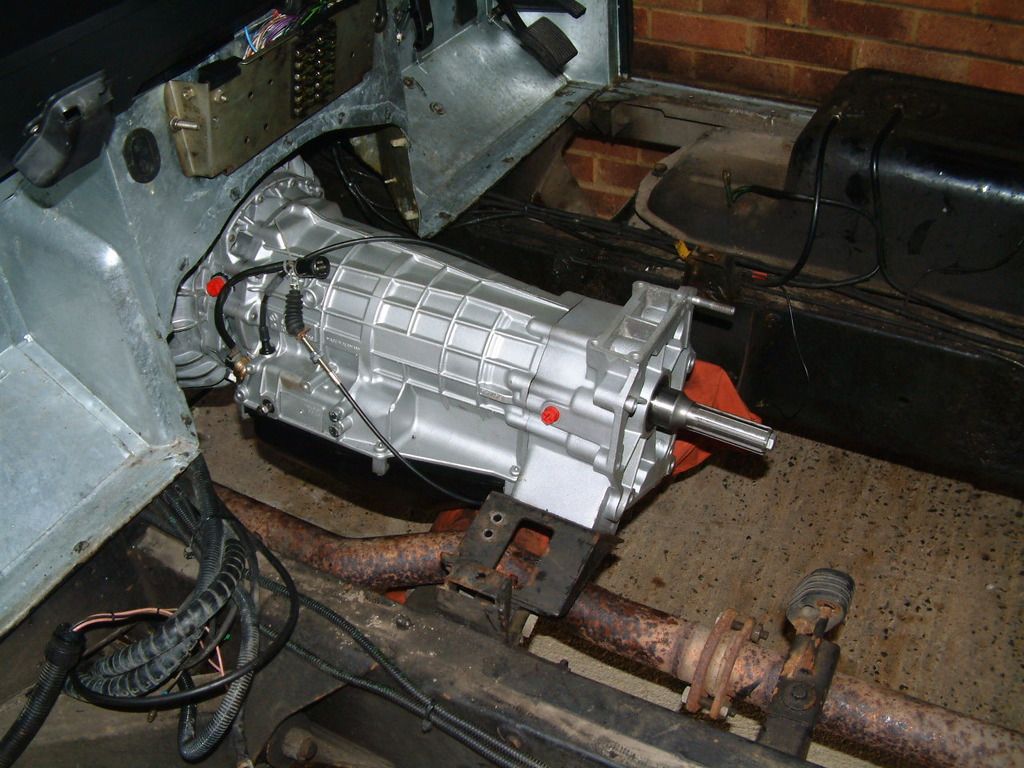
Final insult was when I went to fit the transfer-box.
I am familiar with my old R380 & LT230 as I had them off 3-years ago when I was having my bulkhead galvanised and made use of the time that it was away to remove the transmission to fit a new clutch and replace a couple of seals. It wasn't really necessary but I had time on my hands and with all that access so it seemed foolish not to. I know how they separate but could I move them apart, could I hell !. It is not RTV, there is the slightest movement and I have inserted a blade so it is not suction, it is a physical lock (and yes, I HAVE removed all the bolts / nut before anyone asks). Thought I would remove the input gear to see if that helps but that is stuck fast as well so I guess that is the culprit. Splines look to be in good order (it is cross-drilled and I can see through the bottom inspection cover that there is no rust holding them together) so I gave it up as a bad job and will look at it again next week.
In the mean time, if anyone has any ideas they will be greatly appreciated.