LincolnSteve
Well-Known Member
- Posts
- 1,224
- Location
- Lincoln
Very little progress due to weather/darkness/cold/can't be arsed.
First of the brake pipes went on. It's a long time since I've done any of these but I think it went well. Just got to get the feel for how tight is right.
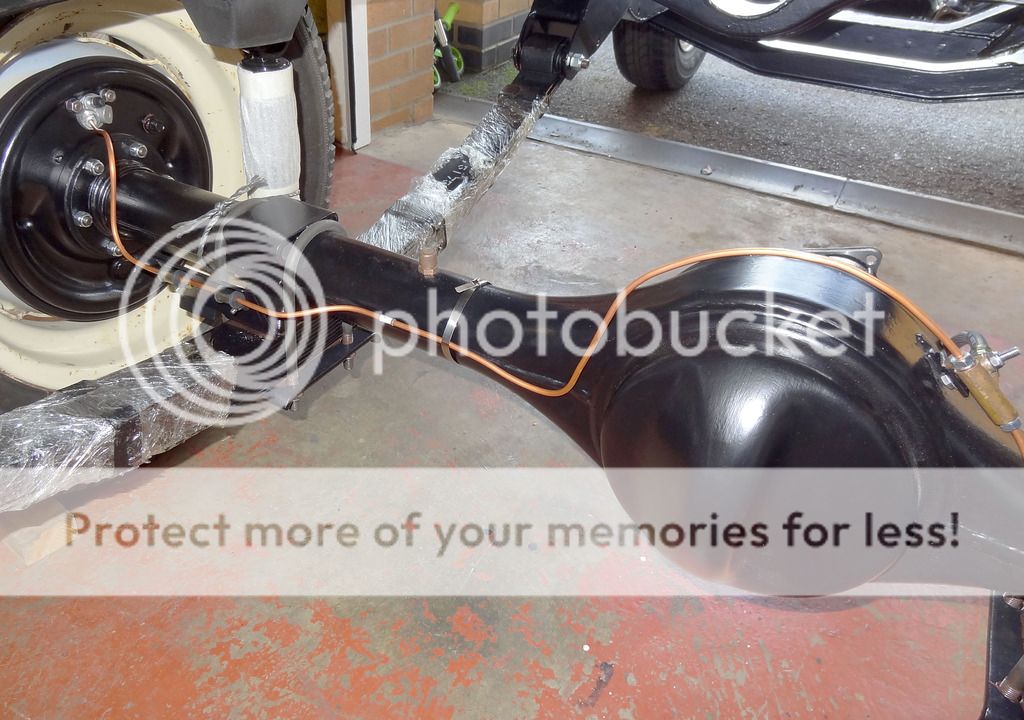
Next major bit will be the body tub. This was removed two years ago last October, stashed away and forgotten about. I started by removing the seal and retainers for the bottom of the back door.
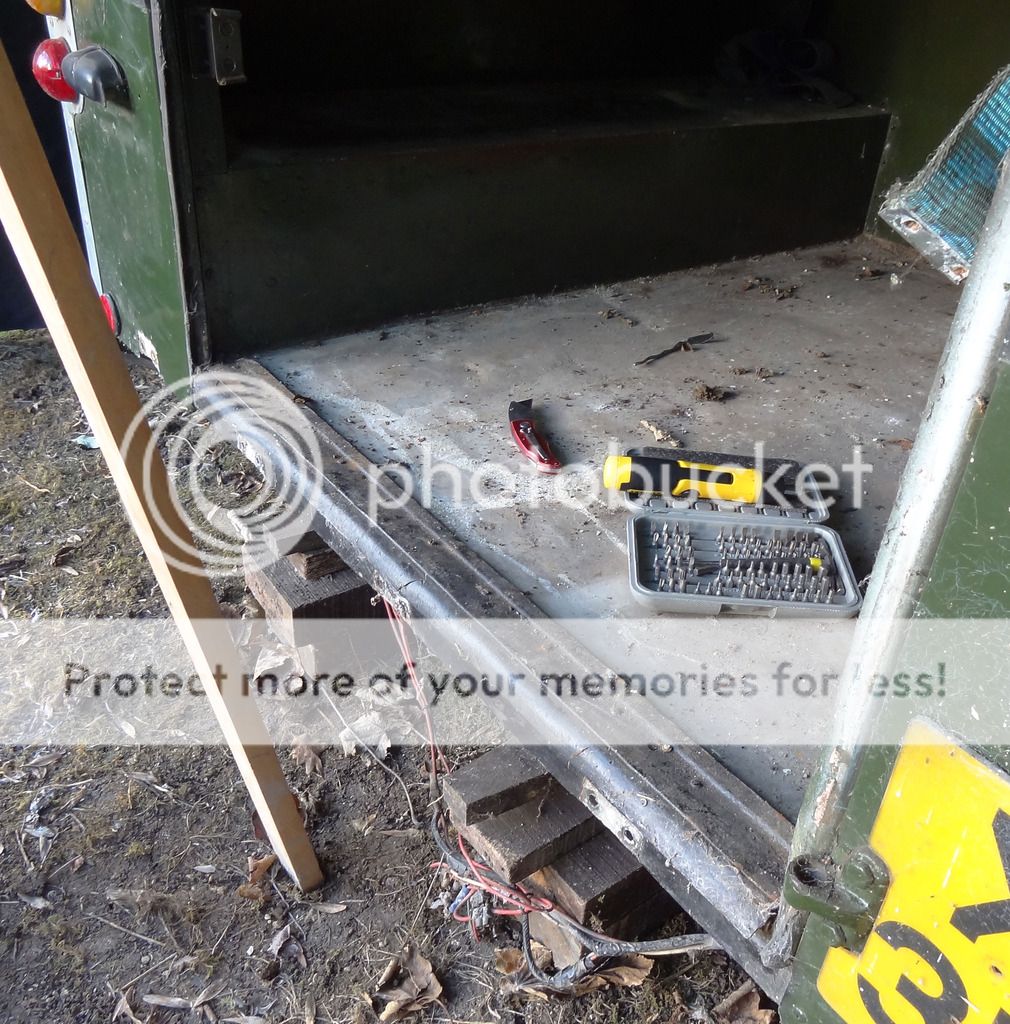
I'm starting to get very familiar with this horrible, white, powdery corrosion. No surprise that it's everywhere.
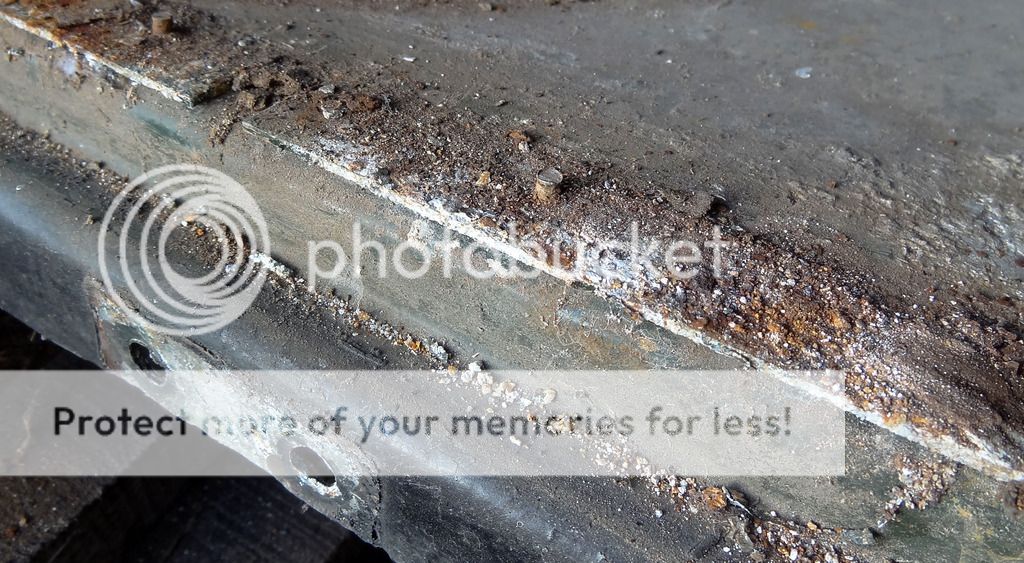
So it's all well and good saying i'm going to sort out the body tub but what do you do if you've run out of room to work on anything. Here is my solution.
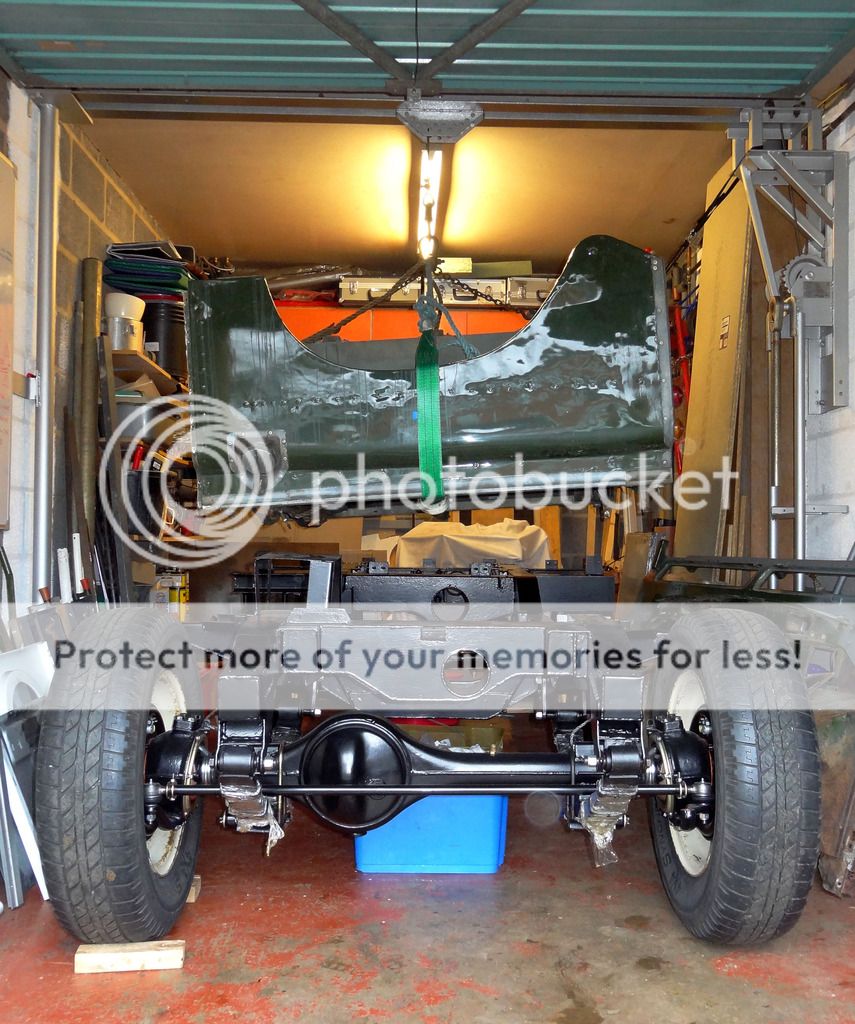
Dangle the tub off the engine hoist. Now I can work on it until I've had enough then I just lift it up, shove the chassis back in under it, shut the door, go in the house and ask myself why I didn't take up a sensible hobby like knitting.
I will make a frame to go under it when it's suspended and then it's less likely to twist when bits get removed to be refurbed. I wish I had more space.
First of the brake pipes went on. It's a long time since I've done any of these but I think it went well. Just got to get the feel for how tight is right.
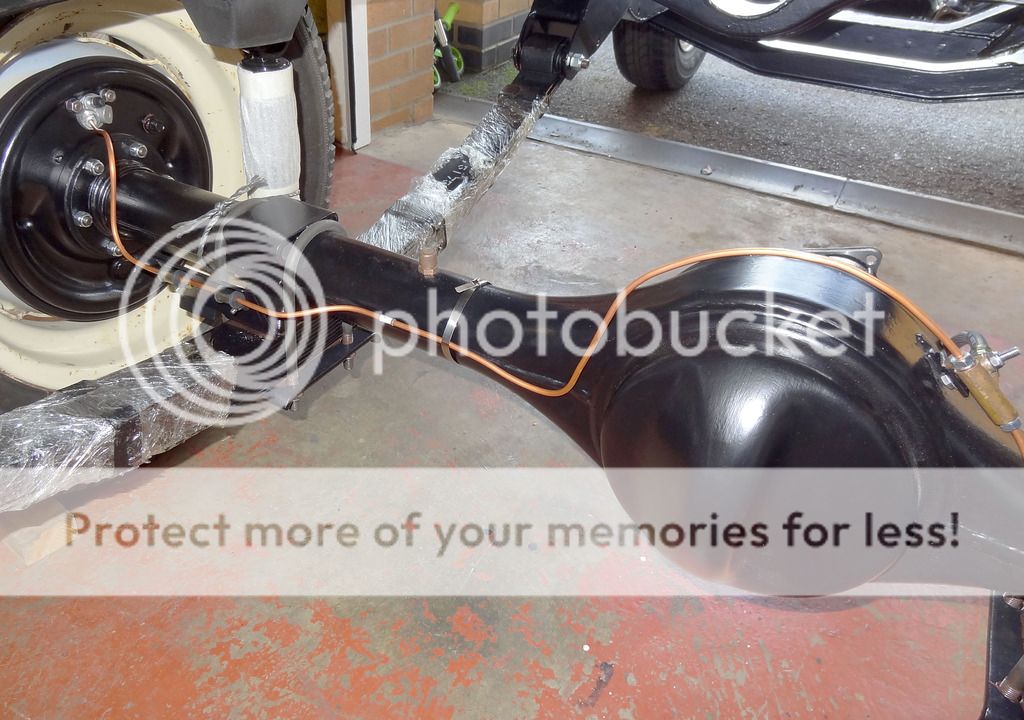
Next major bit will be the body tub. This was removed two years ago last October, stashed away and forgotten about. I started by removing the seal and retainers for the bottom of the back door.
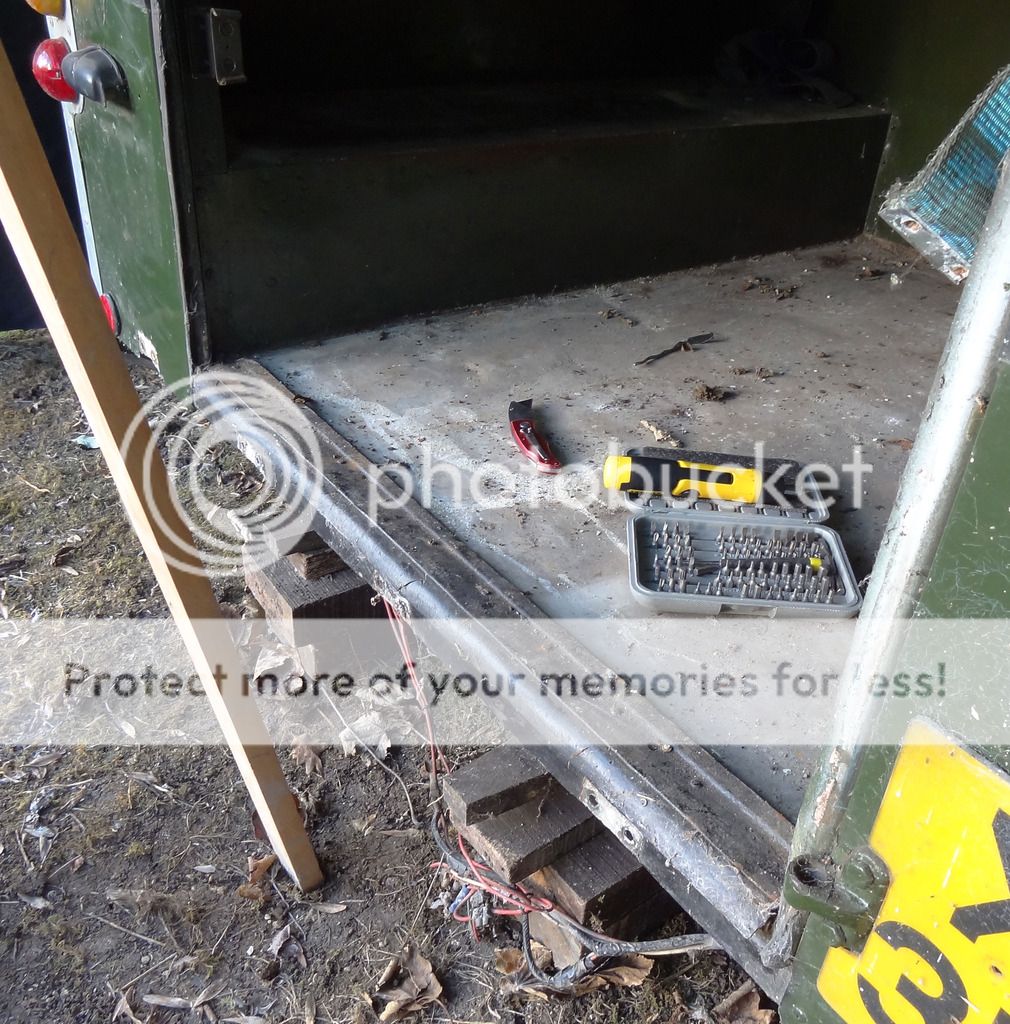
I'm starting to get very familiar with this horrible, white, powdery corrosion. No surprise that it's everywhere.
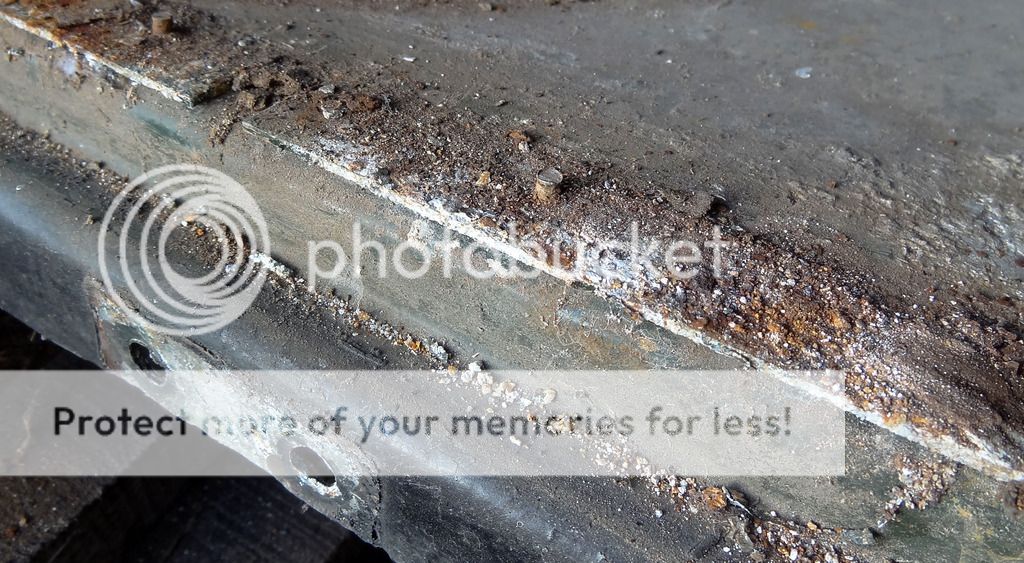
So it's all well and good saying i'm going to sort out the body tub but what do you do if you've run out of room to work on anything. Here is my solution.
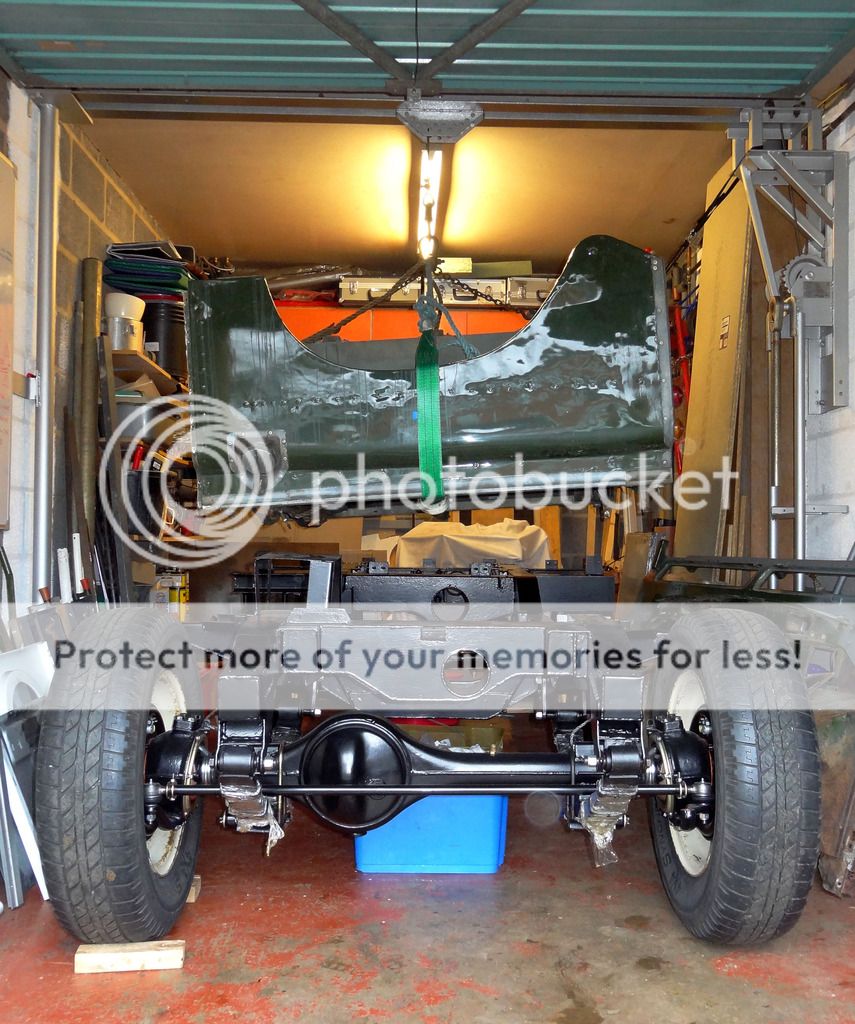
Dangle the tub off the engine hoist. Now I can work on it until I've had enough then I just lift it up, shove the chassis back in under it, shut the door, go in the house and ask myself why I didn't take up a sensible hobby like knitting.
I will make a frame to go under it when it's suspended and then it's less likely to twist when bits get removed to be refurbed. I wish I had more space.