Clarky130
New Member
- Posts
- 3,957
- Location
- Chippenham, UK
Started stripping out the back of my Disco to fit my LPG kit, and found this:
Currently wire-wheeling the edges of the boot floor to find the spot welds so I can drill them out. Boot floor's coming out, but the majority of what's on the side panels is superficial surface rust... what do we think... new side panels, or treat the superficial stuff and plate where necessary?
Where is recommended to get new boot floor?

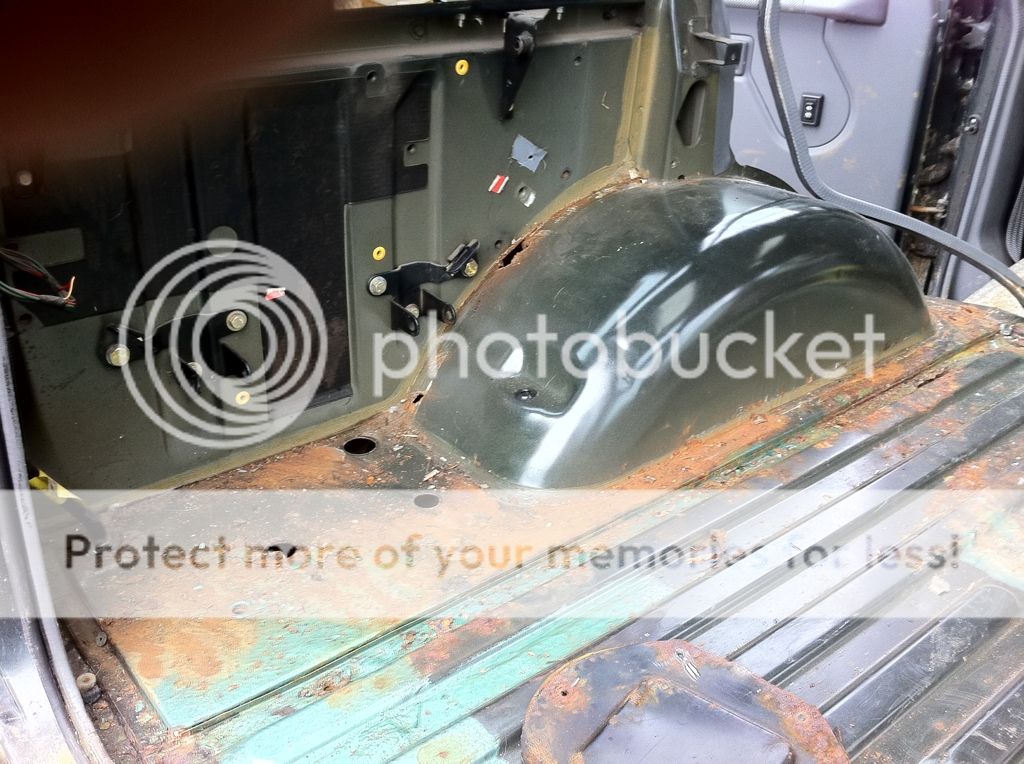
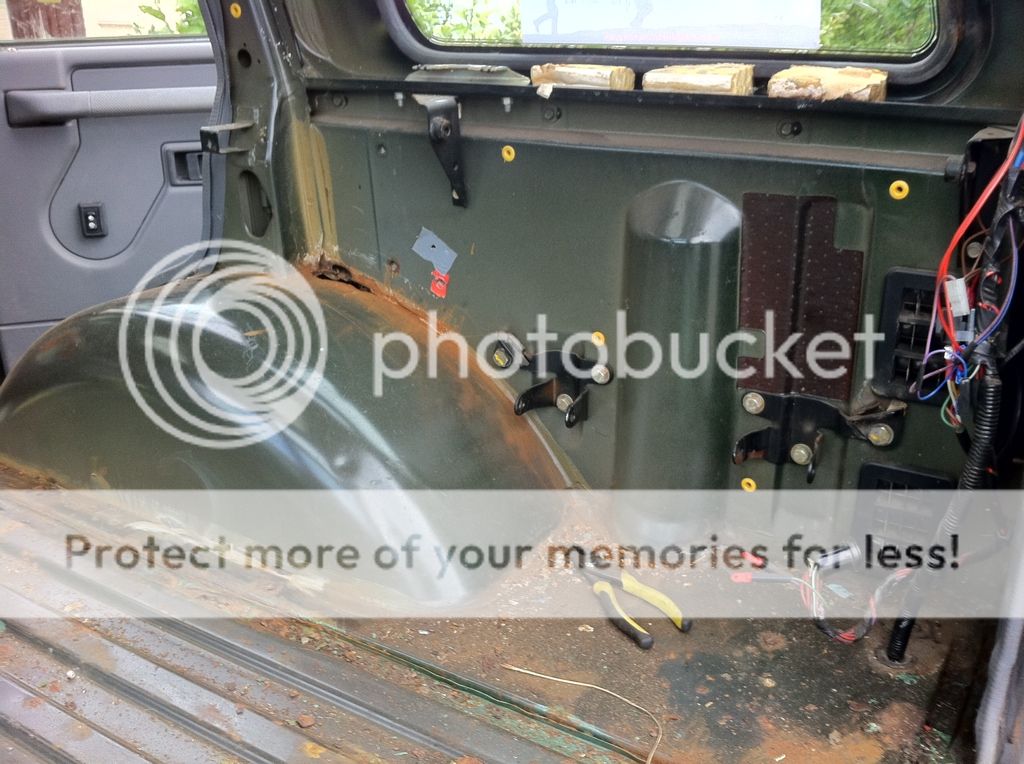
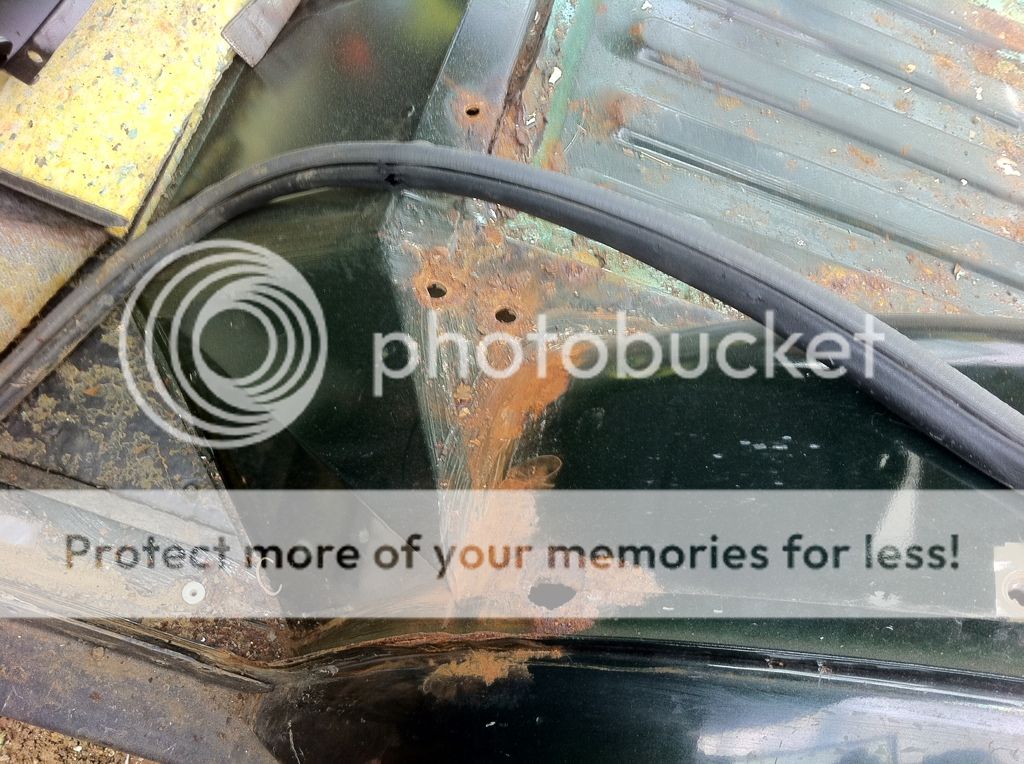
Currently wire-wheeling the edges of the boot floor to find the spot welds so I can drill them out. Boot floor's coming out, but the majority of what's on the side panels is superficial surface rust... what do we think... new side panels, or treat the superficial stuff and plate where necessary?
Where is recommended to get new boot floor?