samc88
Drivels spiritual representative
- Posts
- 2,838
- Location
- Anglesey, North Wales
Time for the rebuild of the swivels and axle ends.
Part 1 - Removing the hub
First job is removing the Fairey free wheeling hubs.
On the body of these there is a grub screw which is undone using a flat bladed screwdriver. Underneath this you should then see a ring which is attached to the plastic strip. This needs to be gently pulled out to release the FWH.
Using a pair of needle nose pliers we got it out so far and then holding the strip and moving the pliers in a rolling motion across the hub, we got it out undamaged.
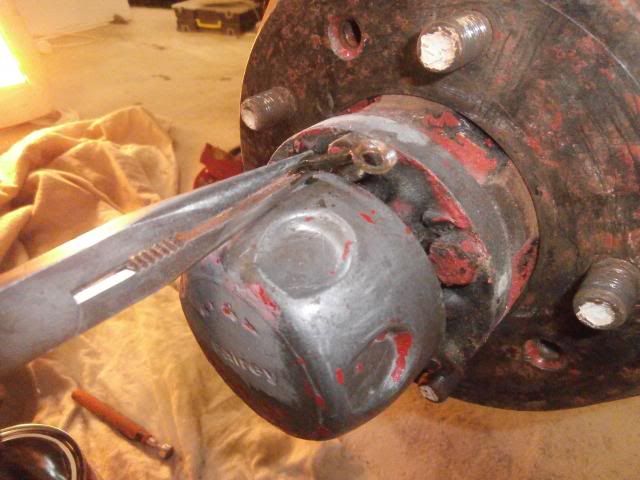
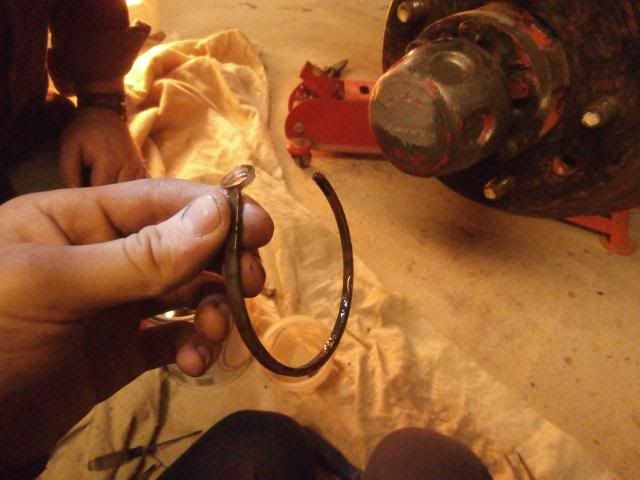
Once this strip is out, the outer casing should pop off
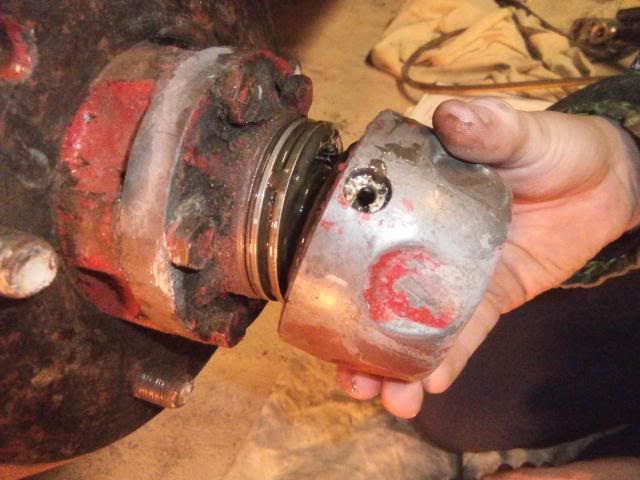

as you can see in the previous photo, there is a castle nut with a split pin running through it. Before this was removed, I twisted the drivers side FWH to the 4x4 position and moved the transfer box into low range and selected first gear to lock the diff, preventing the shaft from turning.
the split pin was removed and the castle nut was removed using a normal socket.
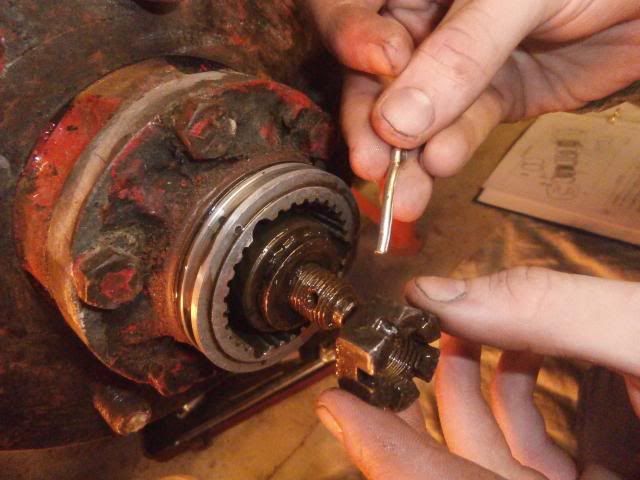
The six hub bolts were then removed (these should have a spring washer)
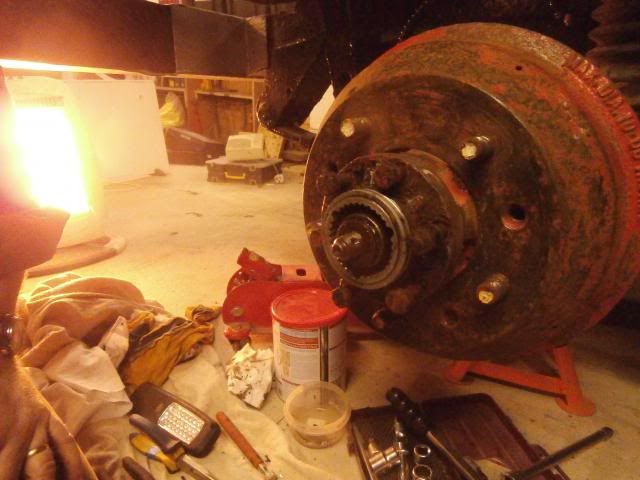
Behind the castle nut should be a washer
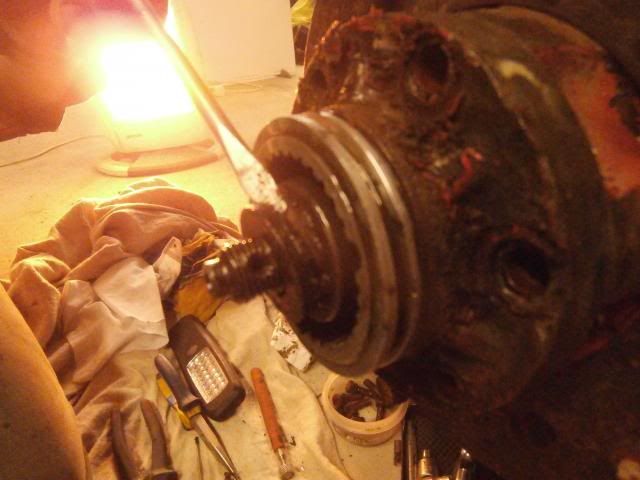
And behind this is a felt seal which has de-laminated on mine
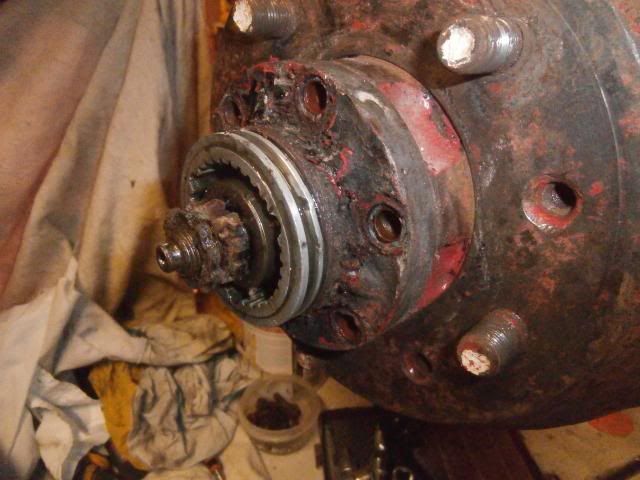
A centre punch was used to make a mark so we could align everything back up afterwards.
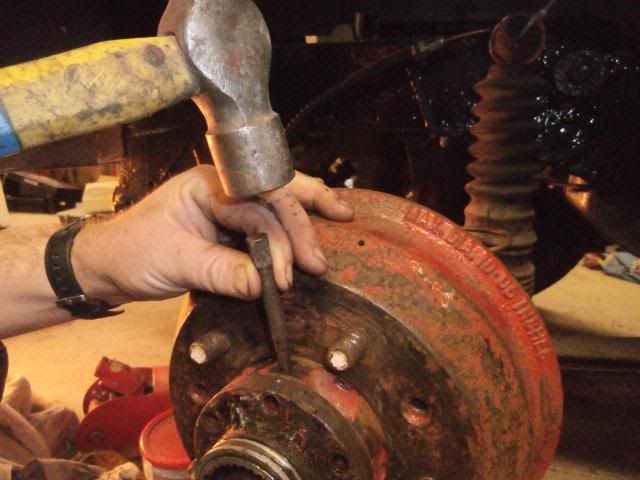
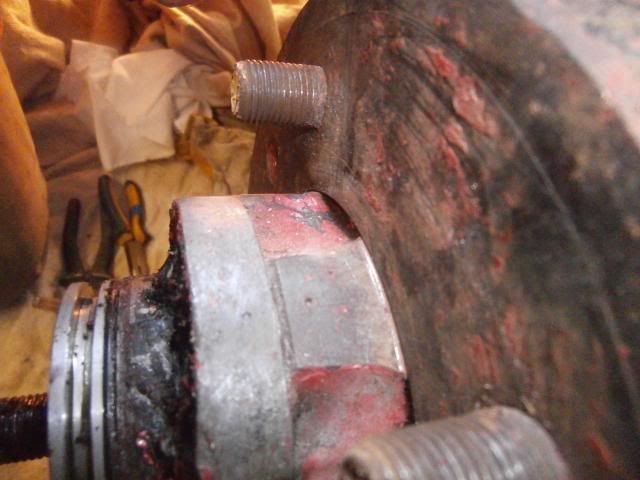
The drive flange could then be removed
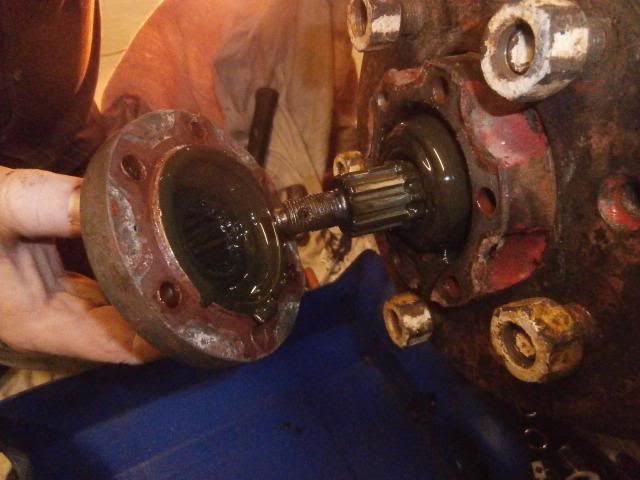
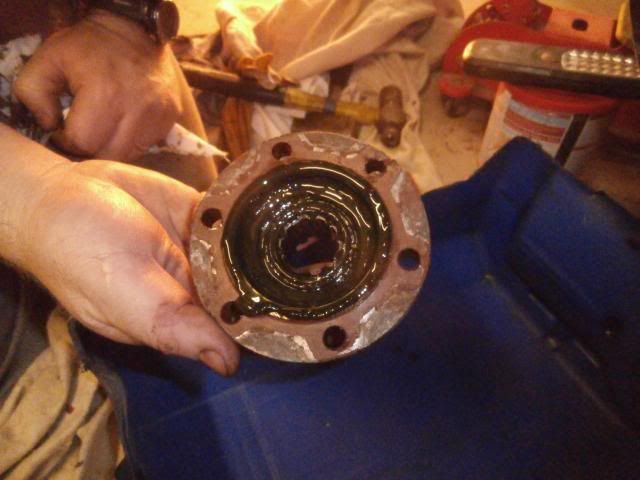
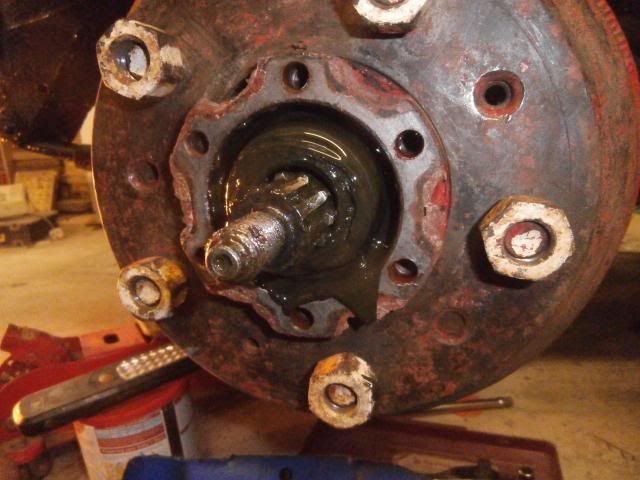
The old oil was cleaned up, revealing the bearing nut.
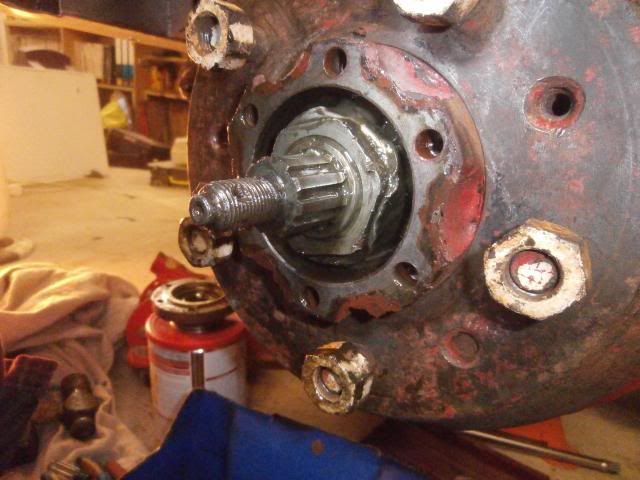
Before taking this off, I took off the brake drum. It is best to adjust the brakes right back so as not to bing the drum with the shoes. Putting a couple of wheel nuts on will help to catch the drum, preventing it from falling on the newly exposed shaft.
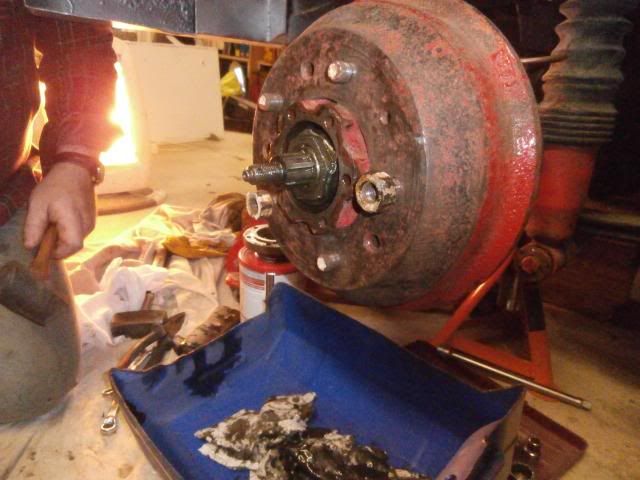
To remove the nut the locking washer must first be knocked flat using a punch.
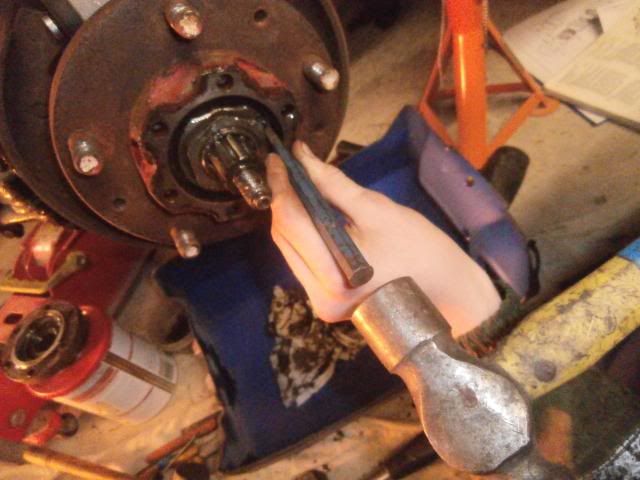
Once this is flat, you can then use the hub nut spanner to undo it. If you look at the above pictures, you can see where a previous owner has used a chisel to tighten/ undo the locknut instead of using a hub spanner.
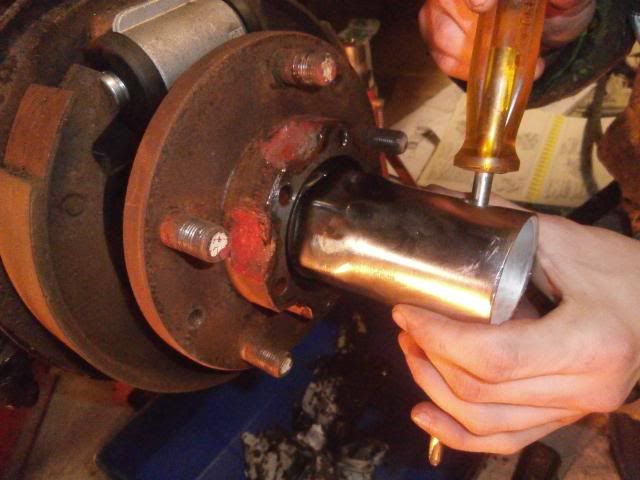
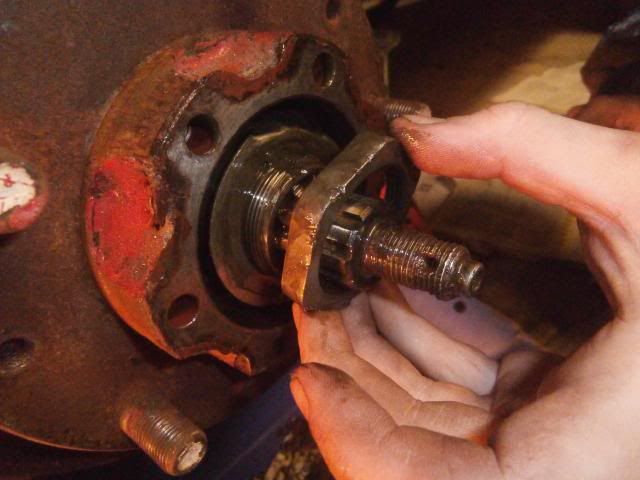
The locking washer is then removed
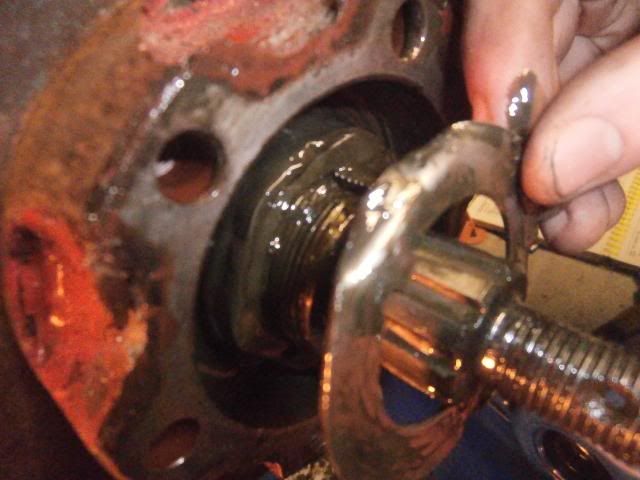
There is another nut behind this (again undone with the hub spanner) and behind this is a thrust washer which is thicker than the locking washer.
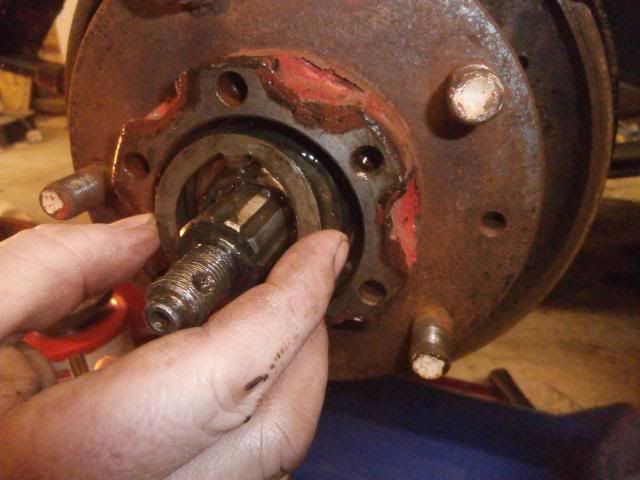
The hub itself can now come off. Be careful, the bearing inner race on mine was loose and could fall out. Its best t keep these clean so no grit/ dust can get in there.
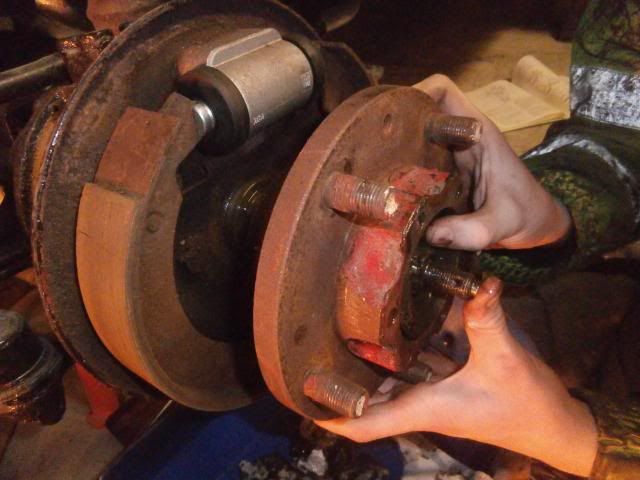
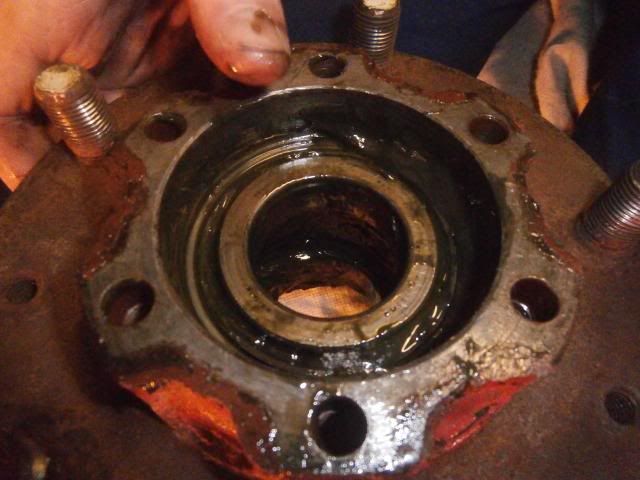
The nuts washers and hub were all cable tied together in the correct order to help keep them in order and so we dont loose anything.
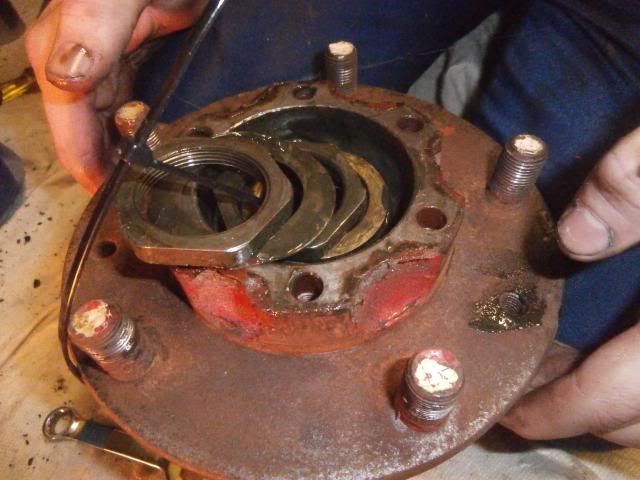
This was then placed in a carrier bag to keep the bearings clean (these are good so will not be replaced)
Part 1 - Removing the hub
First job is removing the Fairey free wheeling hubs.
On the body of these there is a grub screw which is undone using a flat bladed screwdriver. Underneath this you should then see a ring which is attached to the plastic strip. This needs to be gently pulled out to release the FWH.
Using a pair of needle nose pliers we got it out so far and then holding the strip and moving the pliers in a rolling motion across the hub, we got it out undamaged.
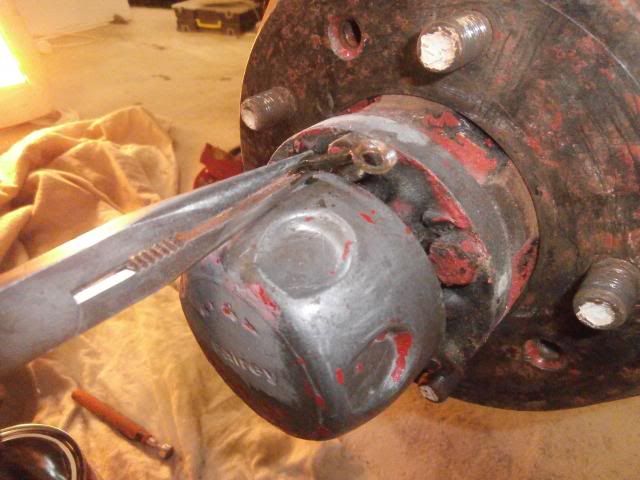
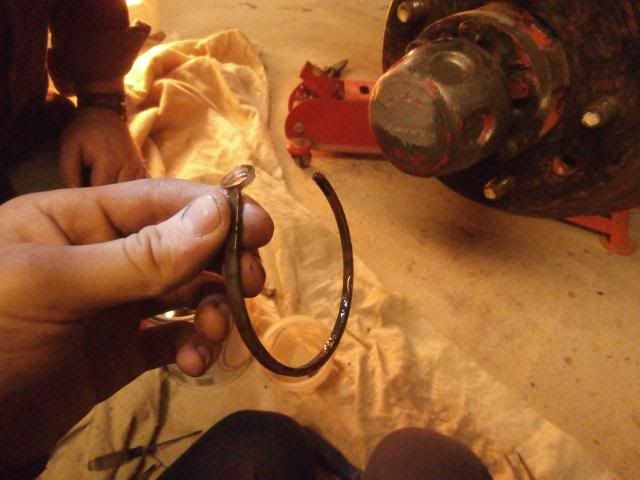
Once this strip is out, the outer casing should pop off
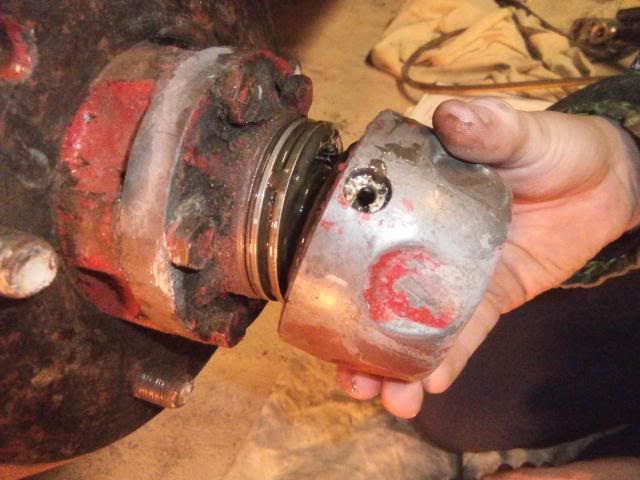

as you can see in the previous photo, there is a castle nut with a split pin running through it. Before this was removed, I twisted the drivers side FWH to the 4x4 position and moved the transfer box into low range and selected first gear to lock the diff, preventing the shaft from turning.
the split pin was removed and the castle nut was removed using a normal socket.
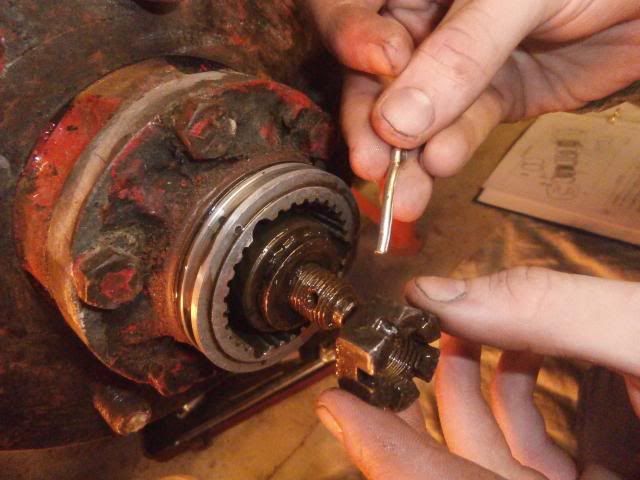
The six hub bolts were then removed (these should have a spring washer)
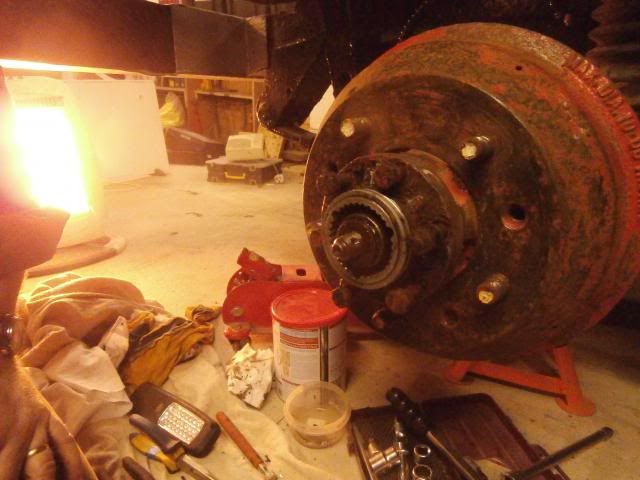
Behind the castle nut should be a washer
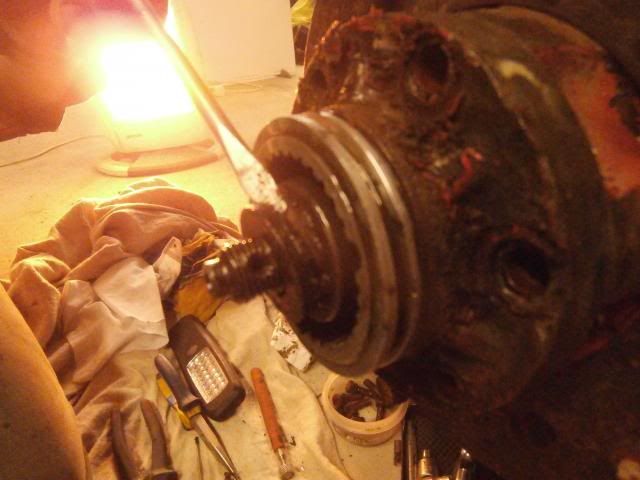
And behind this is a felt seal which has de-laminated on mine
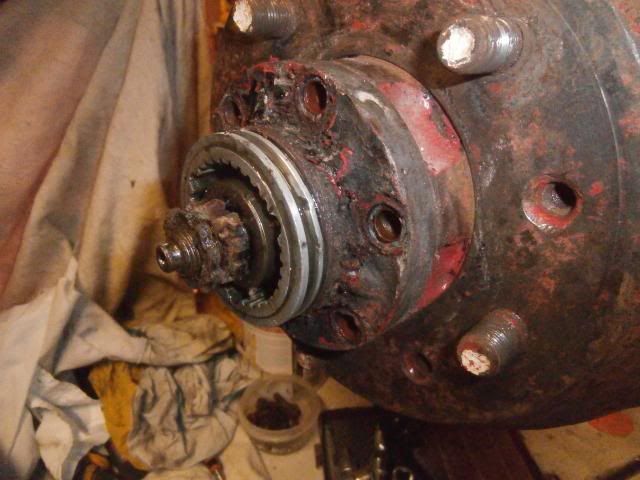
A centre punch was used to make a mark so we could align everything back up afterwards.
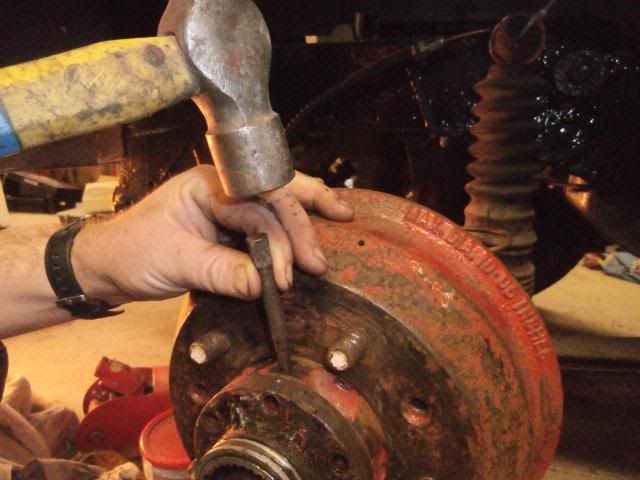
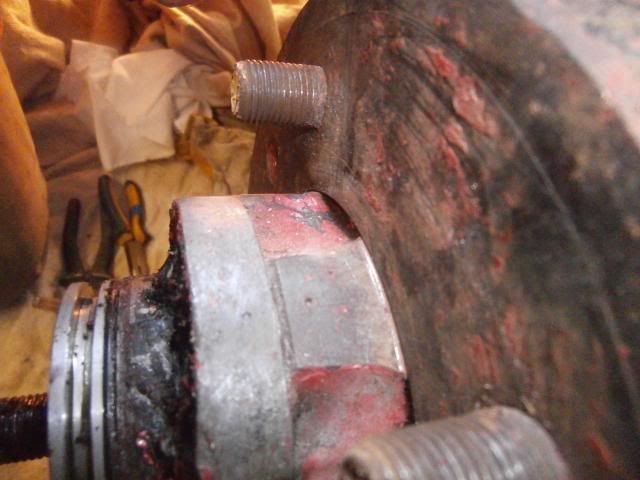
The drive flange could then be removed
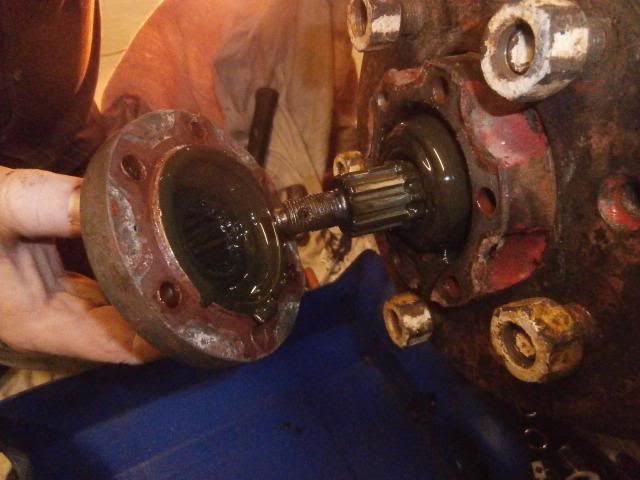
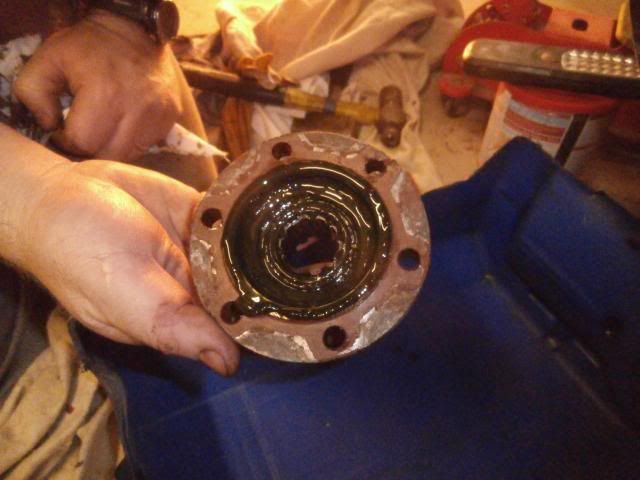
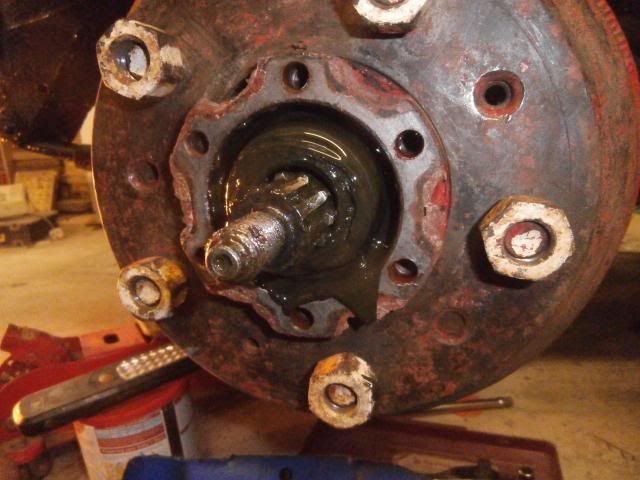
The old oil was cleaned up, revealing the bearing nut.
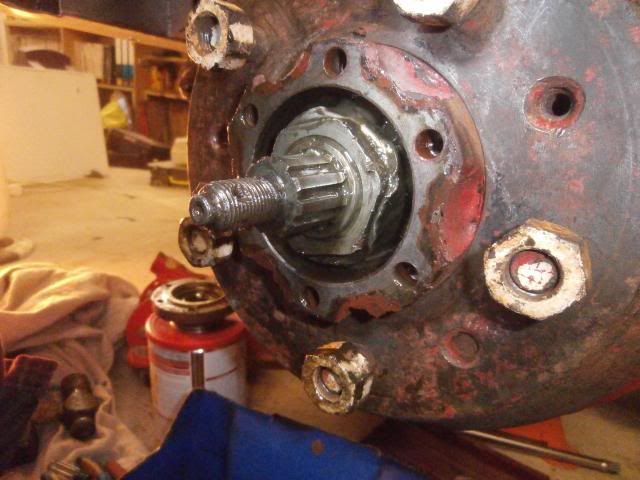
Before taking this off, I took off the brake drum. It is best to adjust the brakes right back so as not to bing the drum with the shoes. Putting a couple of wheel nuts on will help to catch the drum, preventing it from falling on the newly exposed shaft.
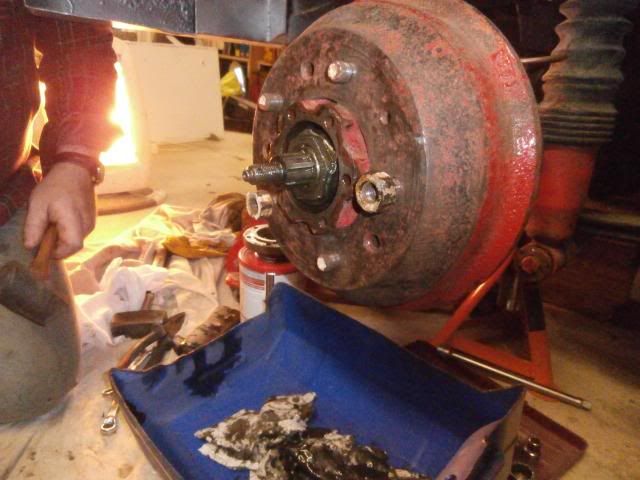
To remove the nut the locking washer must first be knocked flat using a punch.
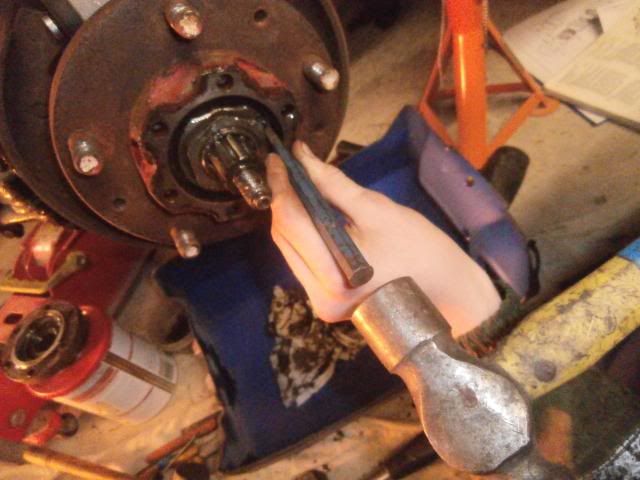
Once this is flat, you can then use the hub nut spanner to undo it. If you look at the above pictures, you can see where a previous owner has used a chisel to tighten/ undo the locknut instead of using a hub spanner.
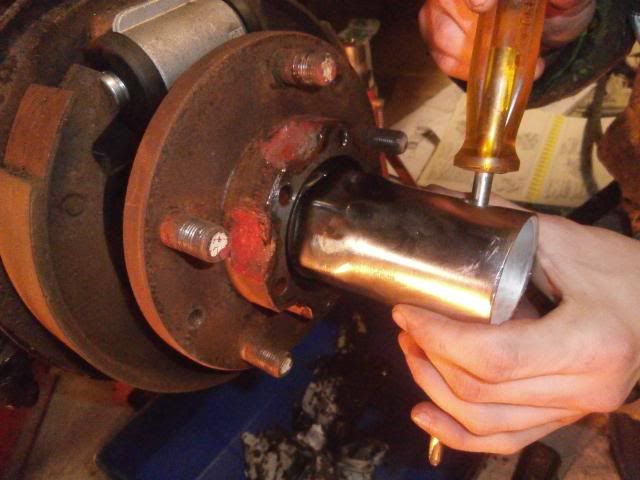
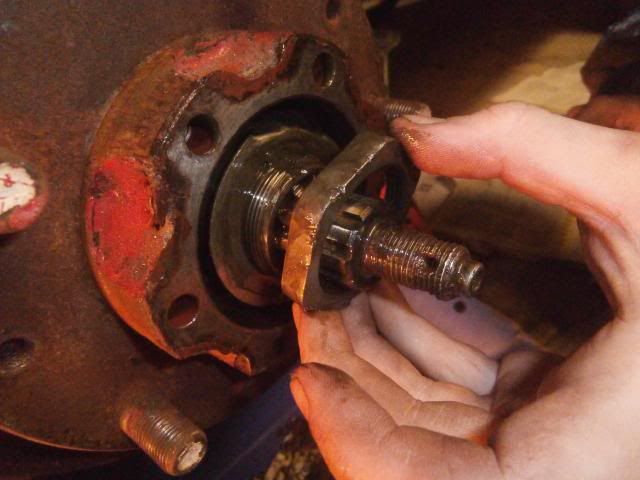
The locking washer is then removed
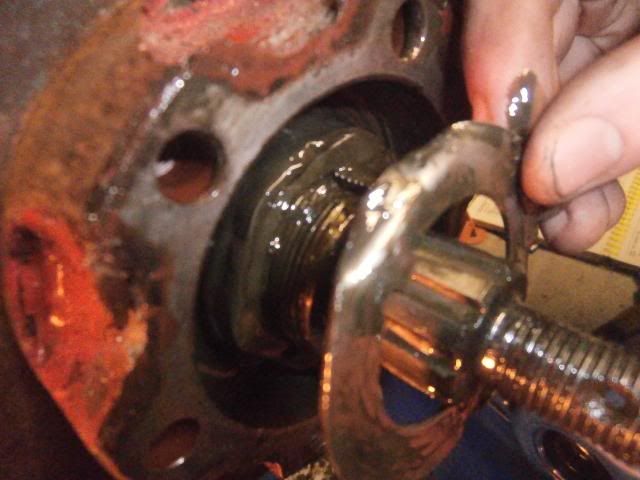
There is another nut behind this (again undone with the hub spanner) and behind this is a thrust washer which is thicker than the locking washer.
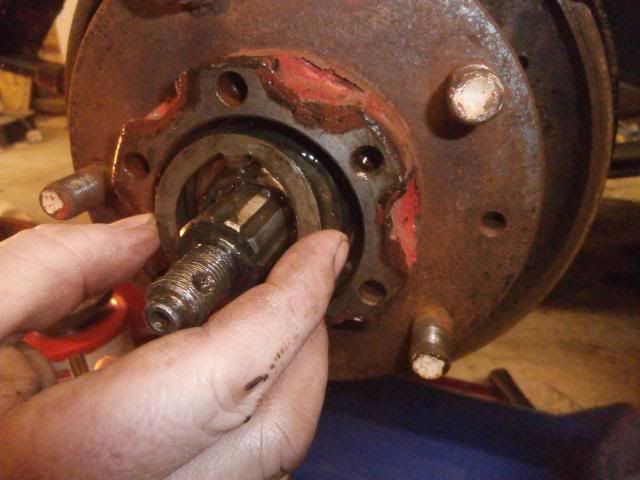
The hub itself can now come off. Be careful, the bearing inner race on mine was loose and could fall out. Its best t keep these clean so no grit/ dust can get in there.
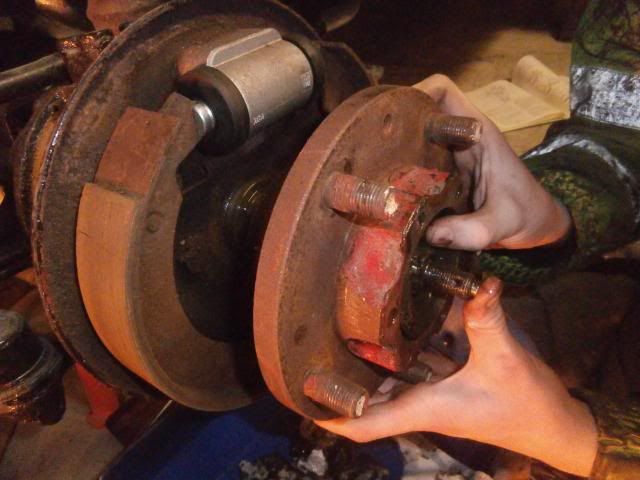
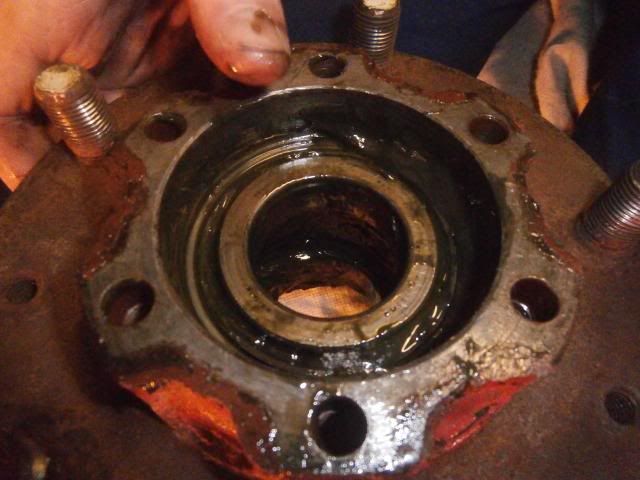
The nuts washers and hub were all cable tied together in the correct order to help keep them in order and so we dont loose anything.
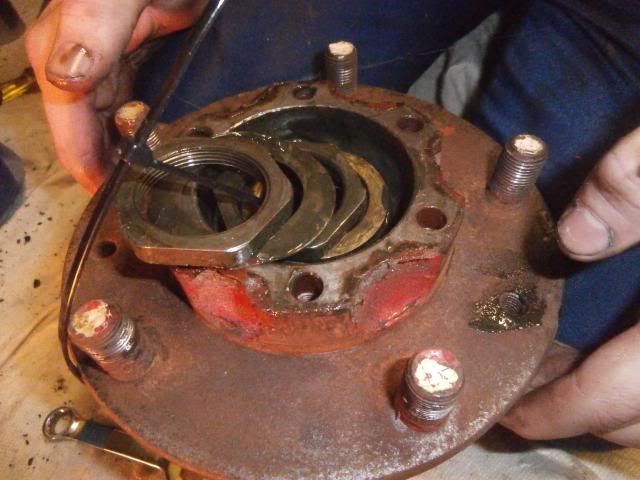
This was then placed in a carrier bag to keep the bearings clean (these are good so will not be replaced)
Last edited: