Right, so here we go!
I wont go over why I am doing this, I think that's clear enough and the pics speak for themselves. Suffice it to say that I felt the need to change my nozzles in my 1997 Range Rover DSE with 119,121 miles. I wanted to go all technical and reference everything right down to who I spoke to and when but that's pushing it so I'll only reference the important bits however, I can reference the rest.
My research and efforts have led me to believe that this is something that all of you can do without worry. There is nothing scary in there! (to quote myself and I'll prove it!)
The first thing to do is get the right injector socket. It is 27 mm (thank you wammers ref this forum) It looks like this:
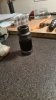
the reason for the hole in the socket is for the sensor wire you will see later.
After you have removed the injectors, you will need to place them in a vice and open them. If you look at the injector, there is a section that has two flats and then there is a section that is six sided bolt type. You place the two sided flat section in a vice and use the injector socket to open the injector like so..
Be careful in how you place the injector in the vice. You should center the injector over the threaded bar in the middle of your vice to obtain the best grip and to protect your vice from damage.
Then you use the socket and a breaker bar to open the injector. You may find that one or two of the injectors refuse to open. This is caused by corrosion that is preventing the two parts from turning. This happened to me and I solved it like so....
Remove the injector from the vise and close the vise. Place the injector on the top of the jaws of the vice and tap the injector repeatedly on the flats of the six sided section turning the injector to a new side between taps. Make sure you hit it flat on the flange and don't hit it like you are Thor! Just give it a tap on each of the six sides.
The next thing to do is disassemble the injector. There are a few pieces in here and one that is specific to each injector. The shim is the one that looks like a washer, for all intents and purposes it is, however,
it is a specially measured washer and must stay with the injector body that it came from in order for my claims to remain true! Only disassemble one injector at a time to prevent making a mistake that will cost you! The shim is located closest to the injector body(the bit that the fuel pipe from the FIP is attached to or the Fuel Injector Pump for the normal folks and the black leak off pipes or the cloth covered rubber hoses that run between the injectors if you prefer, and the two flats that get put in the vice as piced above) Then you have the compression spring, the needle pin,the nozzle spacer (this is the round oddly shaped one with the two holes in it on one side and a trench turned around the center on the other), the needle ( the short pointy bit), the nozzle (the shinny thick bit with three holes on one end and a very narrow hole on the other. the needle fits inside this), the heat shield ( pay attention to how this is placed in the injector) and the nozzle retainer(this is the big metal bit that forms the outside of the injector and has the 6 sided bolt section). The pic bellow shows them as they belong in order. (be advised! the 4th injector is slightly different!)
You now have taken apart your injector and it is ready for cleaning CONGRATULATIONS! The world didn't end and you are still alive.

hehehee
I have no idea what the limit is so ill start a new reply. Have a cup of tea and feel proud you got this far.