samc88
Drivels spiritual representative
- Posts
- 2,838
- Location
- Anglesey, North Wales
Righty ho, I know this is covered in my series rebuild thread but thought it may be helpful to others (especially those with early 90/110's and stuff) if I posted the relevant bits of the engine rebuild in this section. (if thats alright?)
Few pics of hoisting the engine out of the landy
First job when working on the engine was to remove the clutch by undoing the bolts that are located around it. These came off fairly easily
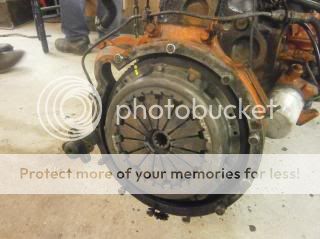
With that out of the way, the next task was removal of the flywheel which is a very heavy peace of kit. This was removed by the bolts in the centre. The yellow marker was on the clucth so that we knew which way to put it back on when it came to refitting. We also did the same to the flywheel but this time with a centre punch
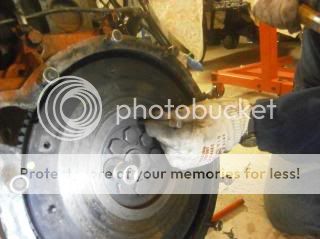
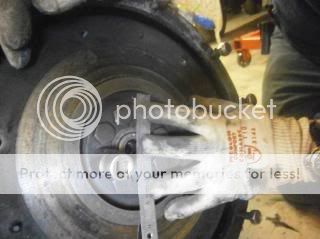
To undo the bolts, you need to stop the flywheel from turning. We did this by using a pry bar against the teeth of the flywheel ring gear. The bolts are tight so we used a breaker bar. If anyone's wondering, this has to be done if the engine is going to be fitted to an engine stand.
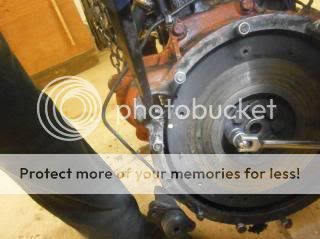

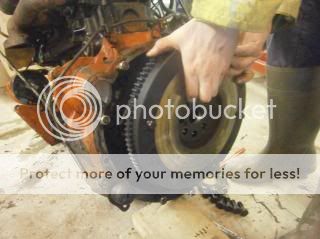
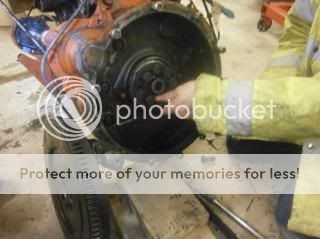
After removing the flywheel, to be able to place the engine on a stand the flywheel cover needs to come off
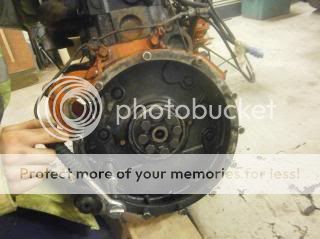
Before removing, there was a bracket holding some wiring and piping near the fuel lift pump which was removed just to give a bit more access.
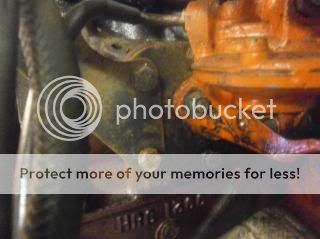
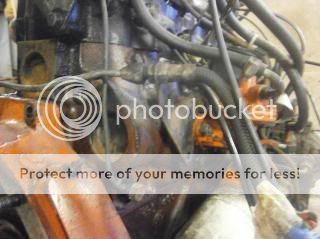
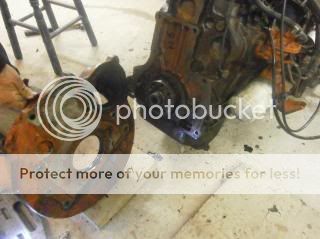
On this engine, the rear crankshaft oil seal was leaking so will be replaced. While we were at this stage it was decided to remove it.
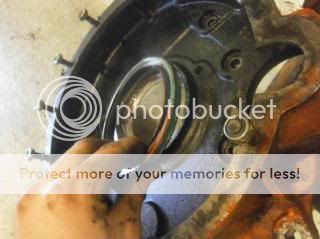
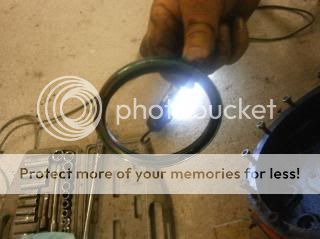
With all that out of the way, we then bolted the engine to the engine stand
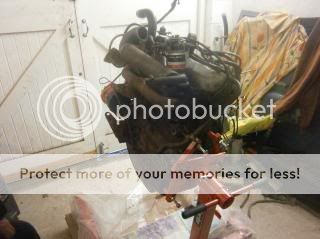
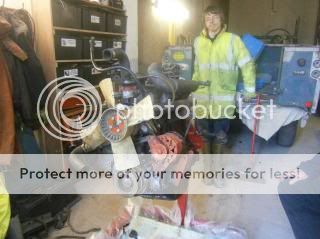
After the engine was bolted to the stand the first thing we did was to remove the fan, fanbelt and the alternator. The fan (a type of plastic on this) is bolted the water pump pully with 4 bolts which were pretty simple to undo once the fan was stopped from rotating.

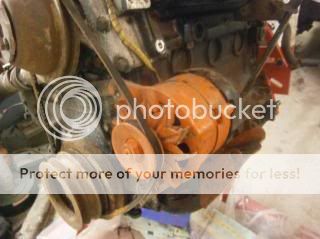
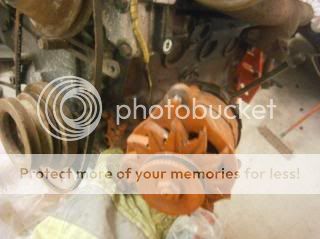

This pipe was the next thing to be removed. To do this, all thatwas needed was to loosen the jubilee clip closest to the engine block
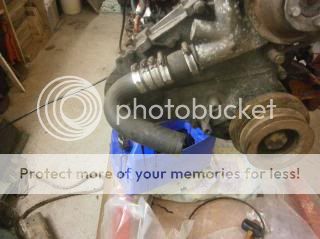
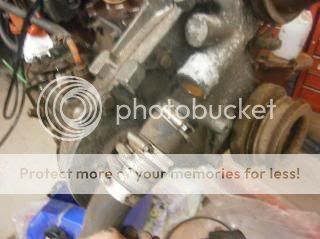
The engine mount brackets were then the next thing to be taken off (well the passenger side one at least, I left the other one for a while to do something else)
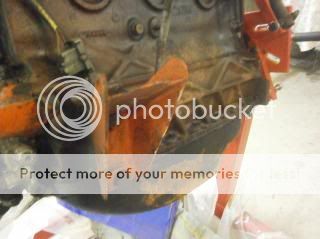
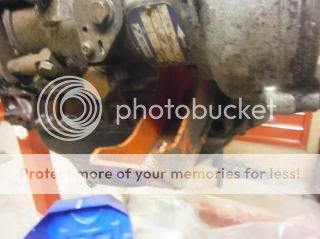
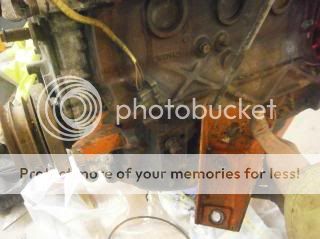
Next to be taken off was the inlet and exhaust manifold. These are 2 separate parts so if you undo all the bolts make sure one does not fall.
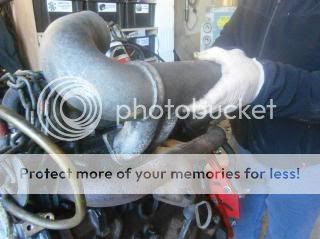
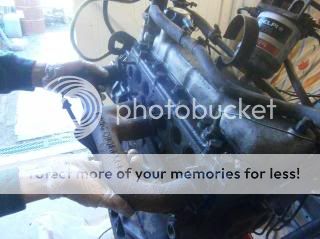
Some of the pipes were then removed as well as the plug for the alternator
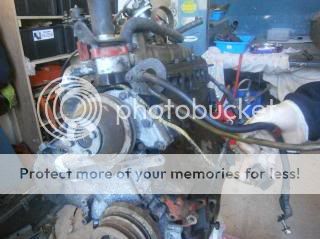
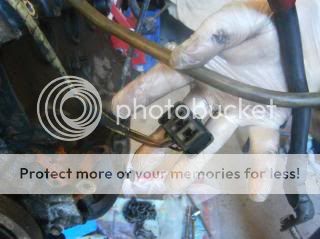
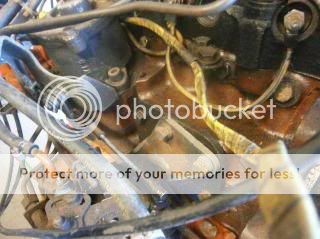
Much better access to work now
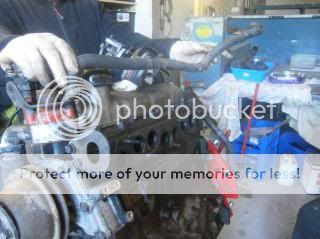
The fuel filter was the next thing to go.
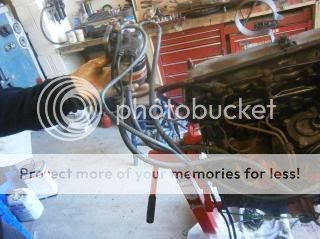
These hoses had to be removed before it could be taken off. When the hoses are taken off the pump, it is important to cover where the hoses fit on to the pump to stop dirt getting in as everything has to be clean.
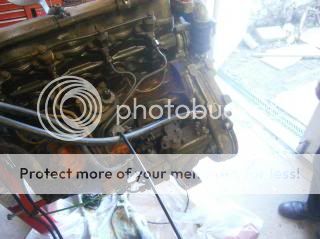
The injector pipes were next. These were removed through the use of injection pipe spanner (like 3/4 of a ring spanner with an open end to slot over the pipe )
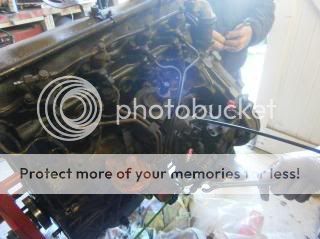
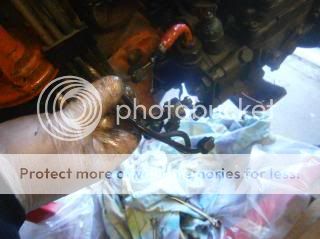
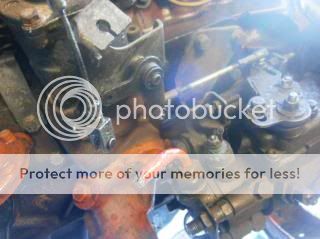
The heater control thing above the thermostat was next to go, this was undone with an adjustable spanner,
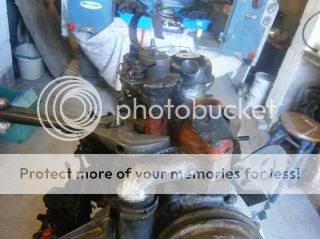
The next thing we did was to remove the injectors. To remove the injectors, the 2 bolts holding them to the block were removed and a brass drift was used to "lift" the injector up to be removed (it makes more sense in real life
). Before removal, the injectors were each numbered so we knew which injector belonged to each cylinder. The spill pipe running along the top of the injectors also has to be removed. Its worth noting that at the bottom of the injectors there is a copper washer, some came out with the injector but another was left in the hole.
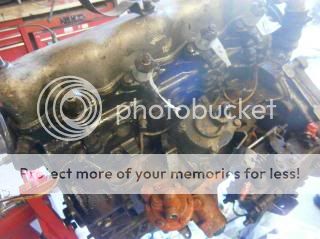
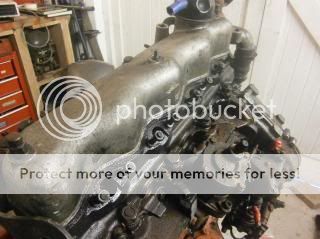
Few pics of hoisting the engine out of the landy
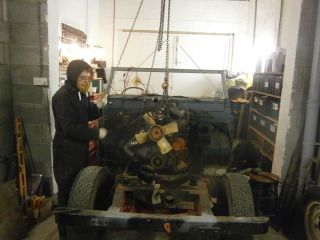
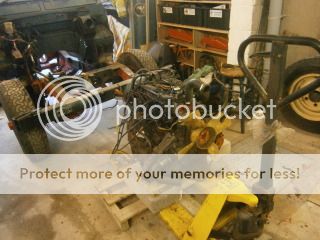

First job when working on the engine was to remove the clutch by undoing the bolts that are located around it. These came off fairly easily
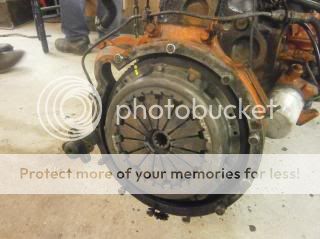
With that out of the way, the next task was removal of the flywheel which is a very heavy peace of kit. This was removed by the bolts in the centre. The yellow marker was on the clucth so that we knew which way to put it back on when it came to refitting. We also did the same to the flywheel but this time with a centre punch
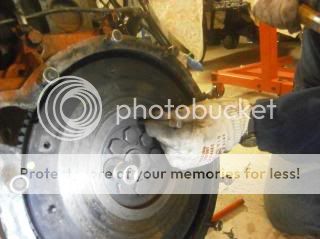
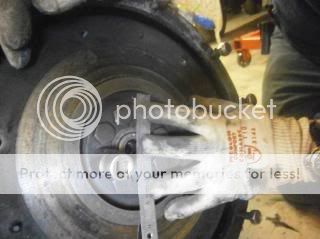
To undo the bolts, you need to stop the flywheel from turning. We did this by using a pry bar against the teeth of the flywheel ring gear. The bolts are tight so we used a breaker bar. If anyone's wondering, this has to be done if the engine is going to be fitted to an engine stand.
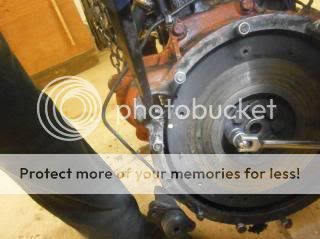

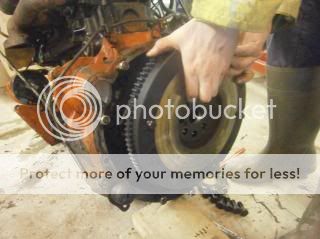
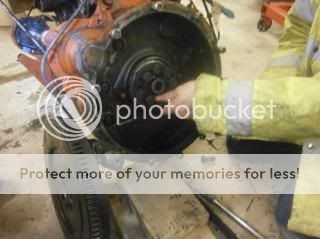
After removing the flywheel, to be able to place the engine on a stand the flywheel cover needs to come off
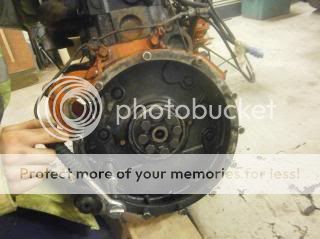
Before removing, there was a bracket holding some wiring and piping near the fuel lift pump which was removed just to give a bit more access.
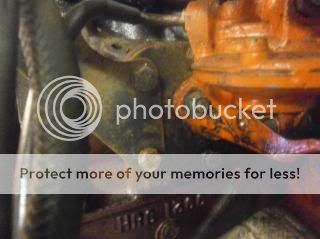
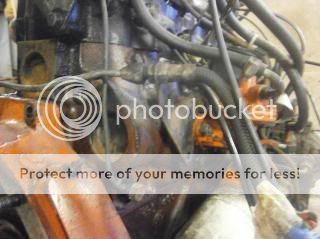
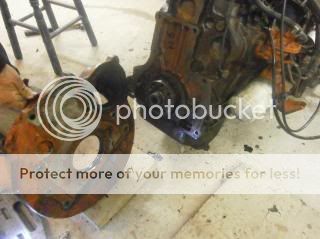
On this engine, the rear crankshaft oil seal was leaking so will be replaced. While we were at this stage it was decided to remove it.
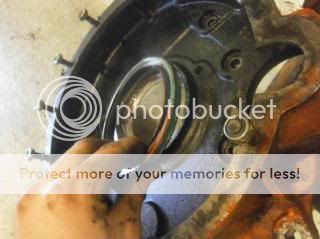
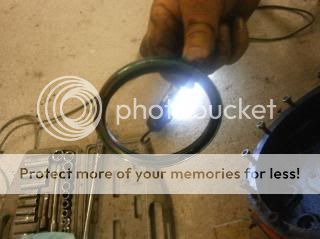
With all that out of the way, we then bolted the engine to the engine stand
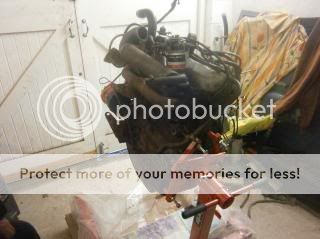
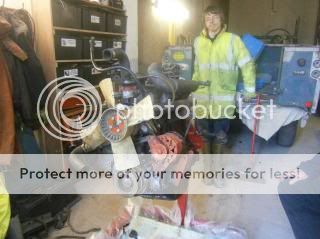
After the engine was bolted to the stand the first thing we did was to remove the fan, fanbelt and the alternator. The fan (a type of plastic on this) is bolted the water pump pully with 4 bolts which were pretty simple to undo once the fan was stopped from rotating.

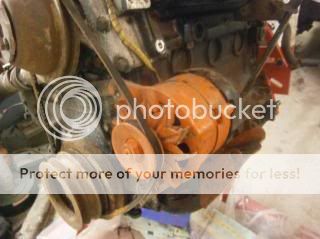
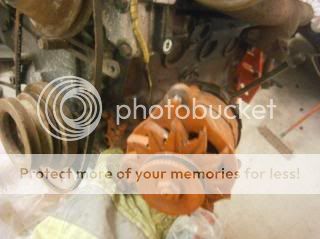

This pipe was the next thing to be removed. To do this, all thatwas needed was to loosen the jubilee clip closest to the engine block
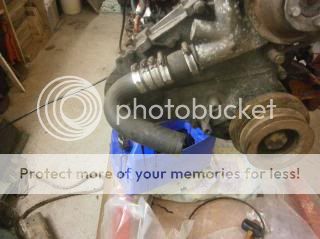
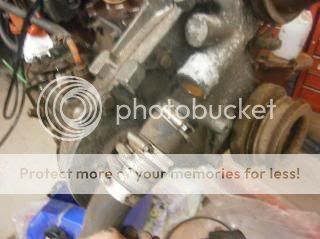
The engine mount brackets were then the next thing to be taken off (well the passenger side one at least, I left the other one for a while to do something else)
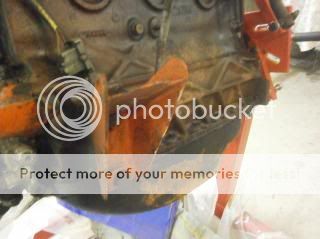
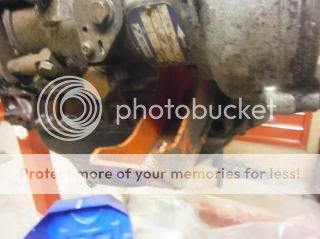
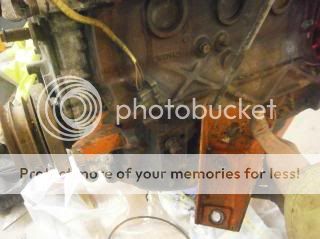
Next to be taken off was the inlet and exhaust manifold. These are 2 separate parts so if you undo all the bolts make sure one does not fall.
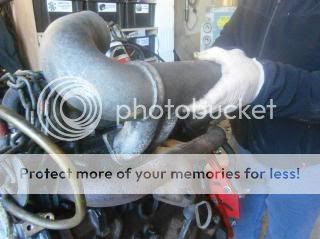
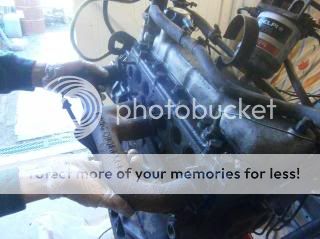
Some of the pipes were then removed as well as the plug for the alternator
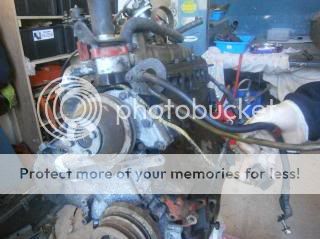
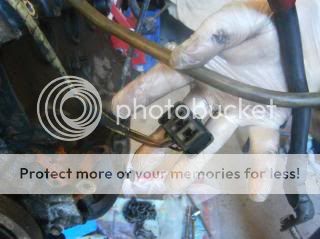
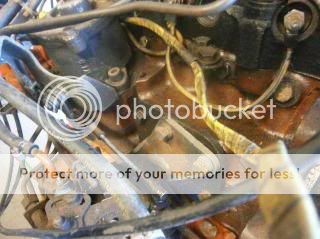
Much better access to work now
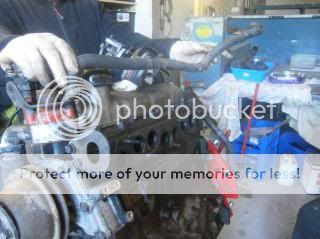
The fuel filter was the next thing to go.
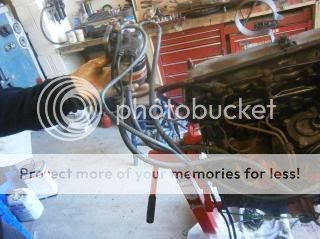
These hoses had to be removed before it could be taken off. When the hoses are taken off the pump, it is important to cover where the hoses fit on to the pump to stop dirt getting in as everything has to be clean.
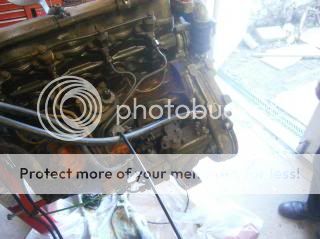
The injector pipes were next. These were removed through the use of injection pipe spanner (like 3/4 of a ring spanner with an open end to slot over the pipe )
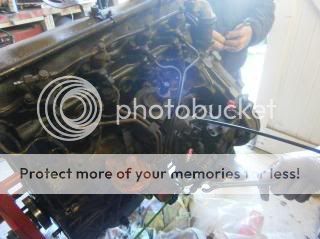
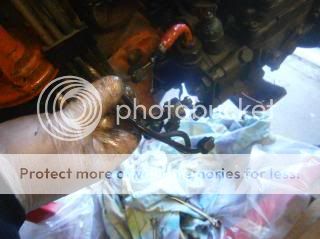
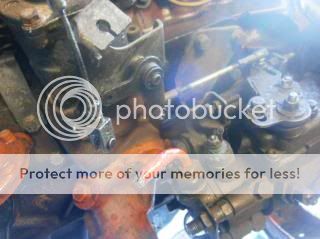
The heater control thing above the thermostat was next to go, this was undone with an adjustable spanner,
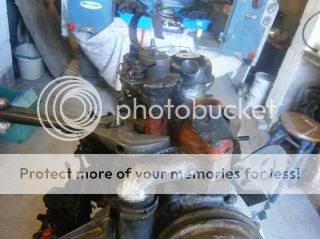
The next thing we did was to remove the injectors. To remove the injectors, the 2 bolts holding them to the block were removed and a brass drift was used to "lift" the injector up to be removed (it makes more sense in real life
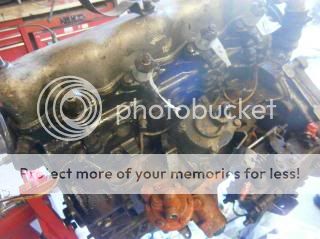
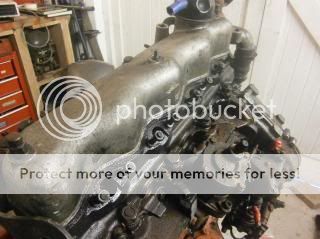