My mod’s to the motor of a st’d K series 1.8 with about 183k on the clock. Everything is bog standard.
I bought mine as a non-runner - the cam belt had jumped causing a piston to bend 2 exhaust valves.
As the head was coming off I took the opportunity to do some other things.
My main focus was to make an easier breathing engine, better gas flow = better torque/power and hopefully better economy to boot.
The basics were done, replaced w’pump, cam tensioner and belt. New H’ bolts and gasket of course. I fitted a strengthened bottom oil rail and as the sump was off I took off the oil pump too and mod’d as per the Kengine site suggestions. Rounding off sharp right angle turns in the oil flow path. Fitted a new pressure relief valve spring seal and ‘o’ ring seal.
Inlet manifold: I bought a Dremel and used it and a TC burr to trim out the plastic flash that’s about 100mm up each of the plastic runners. The flash is a left over from manufacture. I checked that the inlet ports matched those of the inlet manifold - the plastic ones were slightly smaller on mine so I left them alone as their wall thickness wouldn’t allow much to be removed [ if any].
Exhaust manifold: Using my Dremel I ground off any welding splatter and sharp edges that the gas flow would encounter. I did this at each joint in the front half of the exhaust system. I also removed the cat converter. I checked the head ports and manifold ports and trimmed a wee bit out of some of the manifold ports to make the size match. The gasket was left alone.
Head: I again used my Dremel and a TC burr and opened up the coolant apertures on both sides of the head. I just took them out to where the casting showed they could go to. Some were poorly opened up at manufacture and so wound up more than twice as big!.
All valves were back trimmed as per the Kengine site suggestions. Only a slight trim was needed. Each valve was ‘enshrouded’ in the head.
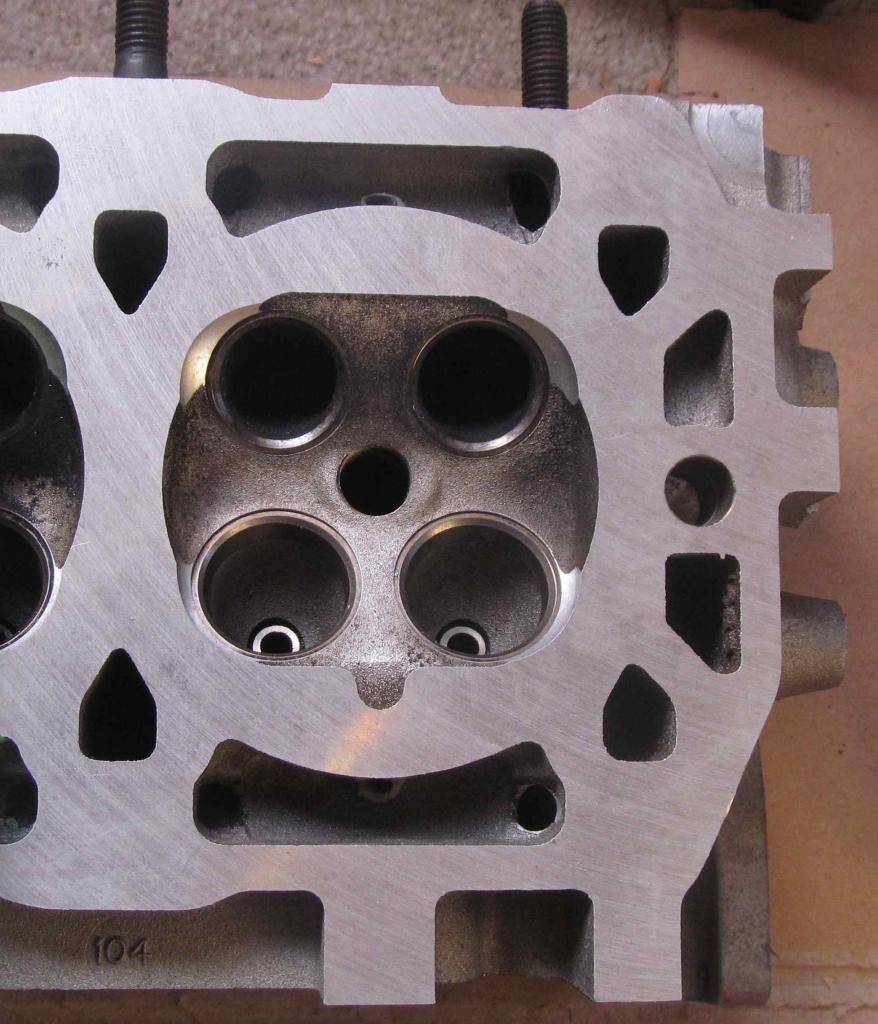
Unshrouded valves!

The Valve seats commonly protrude a step in their respective valve throat. This step was trimmed with my Dremel and smoothed off to a much improved curve.
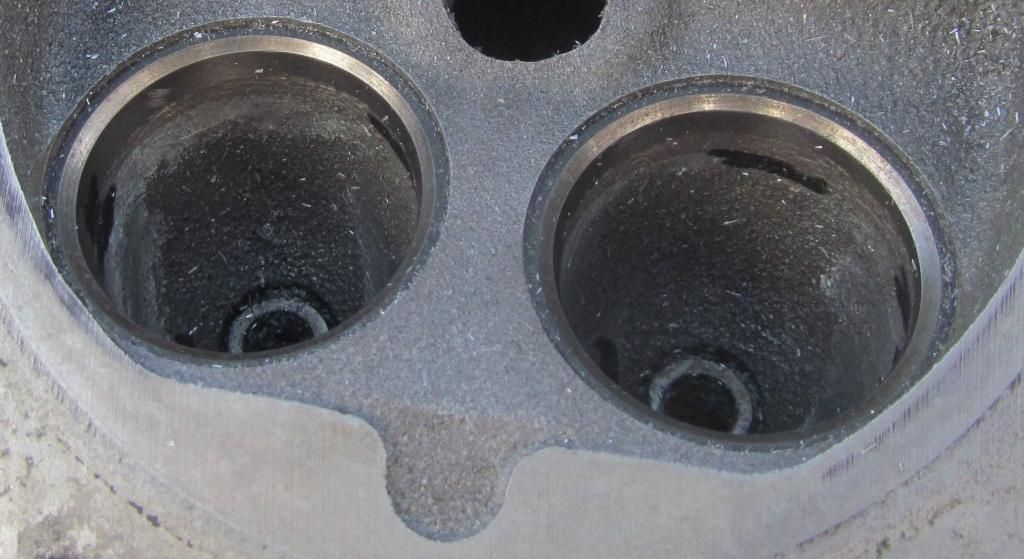
I've trimmed the Inlet valve seat insert here, the black felt pen marks show where a bit more is to come off. Done for exhaust and inlet where needed.
The short radius curves into the valve throats were trimmed a bit too but not a lot, just to even them all up. I also opened up just a small amount in each throat where they transition to their runner. I Removed some material around the valve guide in each throat too but didn’t trim off the guide as some do. On the inlet side I left the surface quite rough with a course sanding drum.
The exhaust runners were opened up a bit too and the hump on the ‘roof’ was lowered by about 1mm. The biurifacation in each runner on the exhaust side was trimmed and the visible edge wound up quite sharp which is ok on the exhaust but should be avoided on the inlet side - leave it blunt. Valves were lapped in. A thorough clean and then reassemble.
I fabricated a
cold air feed. It comes from under the left wing and up through the hole left over when the resonator box is removed. I used 65mm plastic down pipe and fittings!.
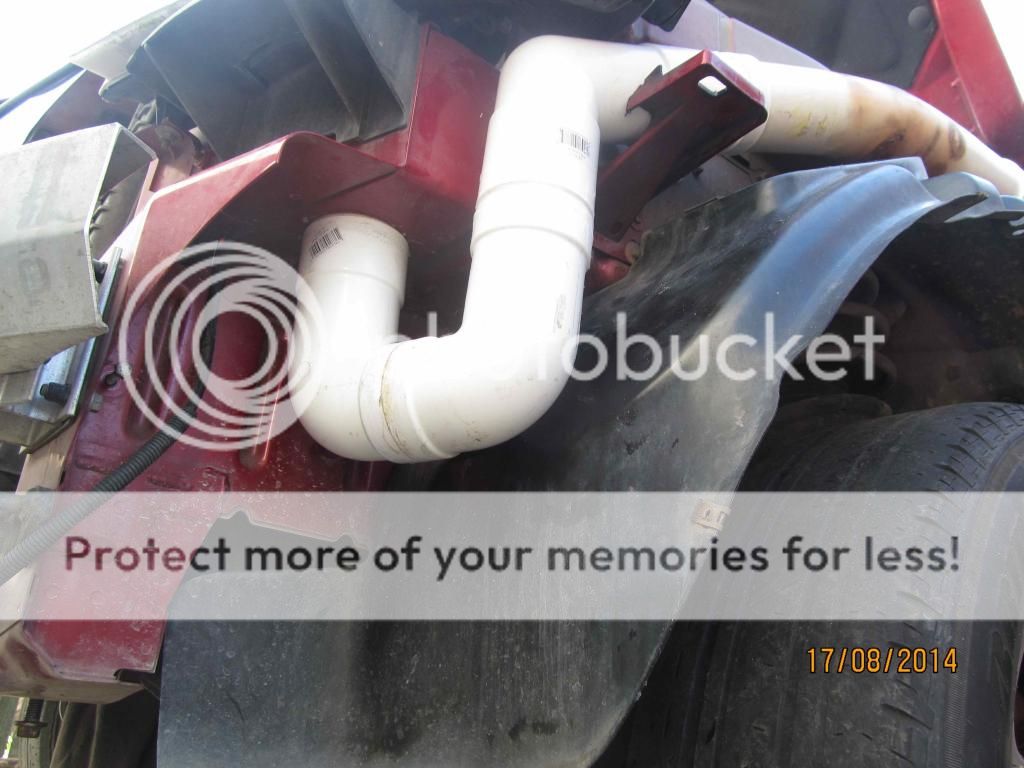
Some flexi ducting is needed either side of my air filter which is a K&N Apollo.
I added three other things: an oil pressure gauge,

a coolant level sensor
[a la Hippo]

and an engine oil cooler. The cooler operates via a thermostat plate that fits over the spin off filter mounting plate.
Result: It runs pretty well. I seem to average about 30 to 31 mpg and can easily get 35. My best is 38! It pulls well in top gear from about 40km/h - albeit slowly. Top speed - don’t know and not really important to me. Under hard acceleration it makes quite a sporty noise, a combination of a free flowing exhaust but the CAF and K&N filter allow for some noise too.
If I had the time /MONEY I’d rebuild the motor and have the crank, pistons and rods carefully balanced to smooth out the motor more - not that it’s rough.
Next step: I want to explore cam timing to ensure / achieve optimal performance.
However, I recently acquired a VVC 143 motor with only 105km on it. I would make an ideal transplant and would bolt straight in. I find the electrical side of things the most worrying. That's where I'd like guidance and advice.
Links:
K Engine page
Hippo's coolant level sensor