BigJock2005
Active Member
Guys,
I am putting a nice set of steelies onto my Defender in place of the alloys and when I went to fit them I realised the black steel nuts I ordered are the wrong size. Will have to send them back.
Now the alloy bolts have a bit of a collar on them as the alloy wheel is thicker.
While they don't look great, do you reckon I am okay to use these nuts torqued up to the right level until the the correct black steel nuts arrive?
As I say, the don't look great but they seem to grip down on the wheels okay.
Couple of pics attached.
Thanks for your comments.
Jock
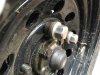
I am putting a nice set of steelies onto my Defender in place of the alloys and when I went to fit them I realised the black steel nuts I ordered are the wrong size. Will have to send them back.
Now the alloy bolts have a bit of a collar on them as the alloy wheel is thicker.
While they don't look great, do you reckon I am okay to use these nuts torqued up to the right level until the the correct black steel nuts arrive?
As I say, the don't look great but they seem to grip down on the wheels okay.
Couple of pics attached.
Thanks for your comments.
Jock
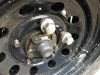
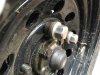