Alibro
Well-Known Member
I thought I'd post my experience here of reconditioning a VCU by flushing it out. I don't believe this can ever be as good as cutting the top off and properly cleaning every disk but my experience so far is extremely positive. Many of us don't have a welder or the skill to use it so without spending hundreds this is your only other choice, this is copied from other threads so may be a bit disjointed.
1. Drill two holes in the end the appropriate size for the tap and bolts or grease nipples you intend to use. I used M10 Extra fine as I hoped the extra number of threads would make it stronger. I think the drill was around 8.9mm but it's easy to find tables showing the correct drill size for your tap.
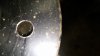
2. Leave it overnight for some of the gunge to ooze out
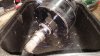
3. Tap the holes now so that any swarf will come out with the gunge as you clean it (use a 1/4" extension bar from a socket set to extend the tap).
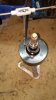
4. Clamp it in a vice and using a syringe or a small funnel pour in as much white spirit as it will take.
I used a syringe last time
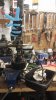
5. Put the rear propshaft onto the splines and stick a long crow bar (or similar) through the UJ and start turning to mix the white spirit with the fluid still in the VCU. Note, this might be hard work.
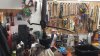
It might be a good idea to tidy your bench before taking photo's and posting them on the internet.
6. Repeat points 2 through 4 many many times over a week or so until there is more white spirit pouring out than gunge and the VCU is quite easy to turn.
7. Once happy it is as clean as your going to get it then leave it to drain for a few days turning repeatedly to try and get rid of as much white spirit as possible. I also blasted it with compressed air and got a lot more out.
8. Once drained start injecting new fluid in with a big syringe. You'll need to keep turning the VCU to get the fluid right down and in between the disks. You might find the fluid wants to come back out so screw in the bolts to stop it.
This process can take several days.
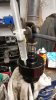
9. Repeat until you have approx 150mls of 100,000 cst fluid in the VCU. This bit is easier said than done due to the amount that spills.
10. Screw in your bolts, refit to the car and drive for a few miles to really mix everything up.
11. Do the one wheel up test and if too slack squirt in a wee bit more fluid (easier said than done) or if too tight let some out then drive for a bit more and test again.
Note, It might be worth putting in a little more than 150mls of fluid as it will be much easier to let excess out than put more in. I plan to add another 10 - 20mls on top of the 150 for that reason. Also a little ends up spilling out so it's hard to measure exactly how much made it into the VCU.
Tips
If using grease nipples they are very shallow so no problem but if using bolts you'll need to cut them down to approx 9mm. I cut mine to 10mm as I'm using a copper washer which is probably unnecessary but I have them so why not.
Drill the holes as near centre as you can (half way between the shaft and the edge) Too near the edge and you'll hit the side wall and too near the shaft and your bolt head will foul the curve at the shaft.
Buy a good quality tap and tap handle. I have a cheap tap which is useless and a reasonably good one which is great. I used metric extra fine M10 but fine or even normal would be OK if using bolts instead of grease nipples. Grease nipples are very shallow so don't have much thread to grip and if your tapping isn't perfect you could easily strip the threads.
Get a good big syringe with a large nozzle.
Weigh the fluid before you start and at the end to confirm you have the right amount in.
Pour the fluid into the syringe. Trying to suck it into the syringe will introduce so many air bubbles you wont be able to use the markings on the syringe to measure it (and its painfully slow).
Both cleaning and filling are very very messy jobs. Be warned and have appropriate gloves and cleaning materials.
To find the silicone fluid go to ebay and search for 100000 cst
Disclaimer
I'm not claiming this is the correct method or saying this is how you should do it. I'm only posting this to show how I did it and to show it can be done.
Edit
VCU is back on the car and giving a OWU time with 5kg weight and 1.2m bar of approx 20 seconds. This is pretty close to OEM I believe so happy it isn't too tight. As pointed out by others, the OWU test cannot confirm the VCU works as a VCU so I tested it in a muddy field and happy to say all four wheels were spinning at the same time. Also tried to spin the wheels pulling away on a wet road and no wheel spin. Still to test on a steep stony hill so can't confirm how much torque will be transferred to the rear wheels but the three VCU's I reconned before worked perfectly for over a year before I sold the cars. If this one is as good as them then we can say this is a valid method for reconditioning your VCU virtually to OEM.
The only concern I have with using this method to refurb your VCU is that there is bound to be residual old fluid mixed with white spirit which is now mixing with the new silicone fluid. This may or may not have an effect on the performance or useful life but it seems to work just fine for now. BTW I went with the grease nipples in the end as they are smaller, lighter so less likely to cause vibration also makes it possible to inject more fluid if necessary with a grease gun.
1. Drill two holes in the end the appropriate size for the tap and bolts or grease nipples you intend to use. I used M10 Extra fine as I hoped the extra number of threads would make it stronger. I think the drill was around 8.9mm but it's easy to find tables showing the correct drill size for your tap.
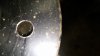
2. Leave it overnight for some of the gunge to ooze out
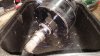
3. Tap the holes now so that any swarf will come out with the gunge as you clean it (use a 1/4" extension bar from a socket set to extend the tap).
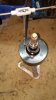
4. Clamp it in a vice and using a syringe or a small funnel pour in as much white spirit as it will take.
I used a syringe last time
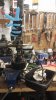
5. Put the rear propshaft onto the splines and stick a long crow bar (or similar) through the UJ and start turning to mix the white spirit with the fluid still in the VCU. Note, this might be hard work.
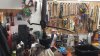
It might be a good idea to tidy your bench before taking photo's and posting them on the internet.
6. Repeat points 2 through 4 many many times over a week or so until there is more white spirit pouring out than gunge and the VCU is quite easy to turn.
7. Once happy it is as clean as your going to get it then leave it to drain for a few days turning repeatedly to try and get rid of as much white spirit as possible. I also blasted it with compressed air and got a lot more out.
8. Once drained start injecting new fluid in with a big syringe. You'll need to keep turning the VCU to get the fluid right down and in between the disks. You might find the fluid wants to come back out so screw in the bolts to stop it.
This process can take several days.
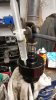
9. Repeat until you have approx 150mls of 100,000 cst fluid in the VCU. This bit is easier said than done due to the amount that spills.
10. Screw in your bolts, refit to the car and drive for a few miles to really mix everything up.
11. Do the one wheel up test and if too slack squirt in a wee bit more fluid (easier said than done) or if too tight let some out then drive for a bit more and test again.
Note, It might be worth putting in a little more than 150mls of fluid as it will be much easier to let excess out than put more in. I plan to add another 10 - 20mls on top of the 150 for that reason. Also a little ends up spilling out so it's hard to measure exactly how much made it into the VCU.
Tips
If using grease nipples they are very shallow so no problem but if using bolts you'll need to cut them down to approx 9mm. I cut mine to 10mm as I'm using a copper washer which is probably unnecessary but I have them so why not.
Drill the holes as near centre as you can (half way between the shaft and the edge) Too near the edge and you'll hit the side wall and too near the shaft and your bolt head will foul the curve at the shaft.
Buy a good quality tap and tap handle. I have a cheap tap which is useless and a reasonably good one which is great. I used metric extra fine M10 but fine or even normal would be OK if using bolts instead of grease nipples. Grease nipples are very shallow so don't have much thread to grip and if your tapping isn't perfect you could easily strip the threads.
Get a good big syringe with a large nozzle.
Weigh the fluid before you start and at the end to confirm you have the right amount in.
Pour the fluid into the syringe. Trying to suck it into the syringe will introduce so many air bubbles you wont be able to use the markings on the syringe to measure it (and its painfully slow).
Both cleaning and filling are very very messy jobs. Be warned and have appropriate gloves and cleaning materials.
To find the silicone fluid go to ebay and search for 100000 cst
Disclaimer
I'm not claiming this is the correct method or saying this is how you should do it. I'm only posting this to show how I did it and to show it can be done.
Edit
VCU is back on the car and giving a OWU time with 5kg weight and 1.2m bar of approx 20 seconds. This is pretty close to OEM I believe so happy it isn't too tight. As pointed out by others, the OWU test cannot confirm the VCU works as a VCU so I tested it in a muddy field and happy to say all four wheels were spinning at the same time. Also tried to spin the wheels pulling away on a wet road and no wheel spin. Still to test on a steep stony hill so can't confirm how much torque will be transferred to the rear wheels but the three VCU's I reconned before worked perfectly for over a year before I sold the cars. If this one is as good as them then we can say this is a valid method for reconditioning your VCU virtually to OEM.
The only concern I have with using this method to refurb your VCU is that there is bound to be residual old fluid mixed with white spirit which is now mixing with the new silicone fluid. This may or may not have an effect on the performance or useful life but it seems to work just fine for now. BTW I went with the grease nipples in the end as they are smaller, lighter so less likely to cause vibration also makes it possible to inject more fluid if necessary with a grease gun.
Last edited: