Hard Drive
Active Member
Hi everyone.
Having replaced my low pressure fuel pump filter twice, with the last one recently, and knowing it has to be fitted the correct way around I thought to do an exposure.
The correct way is indicated by an Arrow on the filter's body and also on the plastic holder.
I wondered what the filter's internals looked like, in that it should be fitted the correct way.
See the pictures.
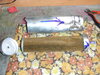
The blue arrow indicates the fitted/flow direction.
I originally tried cutting the filter open with snips, hence the initial battleground appearance.
I used a hacksaw next, which worked.
When fitted the correct way, the maximum surface area for filtering is in use.
Filtered fuel then flows through to the inner chamber and out through the spout.
Reversed, the filtering is more limited as the level of exposed area is very small, especially when compared to the correct way.
I hope this helps some. It also says, to me, that if fitted incorrectly it will still pass enough fuel for running.
Having replaced my low pressure fuel pump filter twice, with the last one recently, and knowing it has to be fitted the correct way around I thought to do an exposure.
The correct way is indicated by an Arrow on the filter's body and also on the plastic holder.
I wondered what the filter's internals looked like, in that it should be fitted the correct way.
See the pictures.
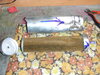
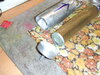
I originally tried cutting the filter open with snips, hence the initial battleground appearance.
I used a hacksaw next, which worked.
When fitted the correct way, the maximum surface area for filtering is in use.
Filtered fuel then flows through to the inner chamber and out through the spout.
Reversed, the filtering is more limited as the level of exposed area is very small, especially when compared to the correct way.
I hope this helps some. It also says, to me, that if fitted incorrectly it will still pass enough fuel for running.