NiallRussell
Well-Known Member
so today didn't get much done. But started to cut.
the irony of all this is the top part of the bulkhead which I thought was going to need attention is starting to look like a scratch compared with whats happening in the footwells.
much more rust on the panel than I thought yesterday, have a replacement foot box coming. It's an awkward place to get the cutter into as the brake lines are right there as well as other buggers. So i've cut out the rusty crap, and will make it neater later, or maybe neat enough to then shape the new part to. We'll see. I have just got the floor panel off to get the last of the crap out (the lip that joins under it) and then will maybe have some more room.
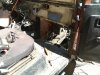
the irony of all this is the top part of the bulkhead which I thought was going to need attention is starting to look like a scratch compared with whats happening in the footwells.
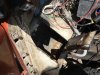
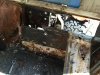
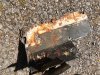
much more rust on the panel than I thought yesterday, have a replacement foot box coming. It's an awkward place to get the cutter into as the brake lines are right there as well as other buggers. So i've cut out the rusty crap, and will make it neater later, or maybe neat enough to then shape the new part to. We'll see. I have just got the floor panel off to get the last of the crap out (the lip that joins under it) and then will maybe have some more room.
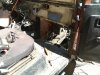